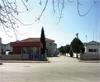
İplik üretiminde Türkiye’nin önde gelen firmalarından birisi olan İpliksan A.Ş, 1932’li yıllara uzanan köklü bir geçmişe sahip. Küçük bir işletme şeklinde el halıcılığı tesisi ile sektöre giren firma, bugün yıllık ortalama 5.000 ton iplik üretiminin yüzde 80’lik kısmını 35 ülkeye ihraç ediyor. Kalan yüzde 20’lik kısmı ise Bravo el örgü yünleri markası ile iç pazara sunan İpliksan’ın ihraç pazarları arasında; İngiltere, Almanya, Fransa, Amerika, Danimarka, Brezilya, İtalya ve Kanada öne çıkıyor.
Küçük bir halı işletmesi olarak Isparta’da faaliyetlerine başlayan İpliksan, yıllar içinde geçirdiği değişim ile farklı bir yapıya büründü ve yüksek oranda yurtdışı odaklı üretimini sürdürdü. İlk olarak 1950 yılında Mehmet Gürkan tarafından kurulan, Gürkan Kollektif Aile Şirketi adıyla, halı ipliği üretimine başlayan firma, 1971 yılına kadar bu isimle üretimine devam etti. 1971 yılında firmayı fesheden Mustafa Gürkan, Gürkan A.Ş’yi kurdu ve daha sonra 1973 yılında İpliksan olarak devam eden süreci başlatmış oldu. 1986 yılında yarı kamgarn tesis yatırımı ile el örgü imalatına başlayan İpliksan,1991 yılında, Türkiye’nin ilk TSE belgeli el örgü ipliği unvanını kazandı.
Üretimini Sertifikalandırarak Büyüdü
İpliksan A.Ş., 1997 yılında kamgarn iplik, 2004 yılında ise fantezi iplik yatırımlarıyla devam ederek büyümesini sürdürdü. 2006 yılında ise İpliksan, ISO 9001:2000 belgesini alarak Türkiye’nin kalite sistem belgesini alan ilk el örgü ipliği üreticisi oldu. 2010 yılında belgesini yenileyerek 9001:2008’e geçiş yapan firma, 2008 yılında ise OEKO-TEX Standart 100 ve Global Organik Standart Sertifikalarına sahip olarak üretimlerinin çevreye ve insan hayatına zararlı olmadığını kanıtladı.
Süre gelen yatırımlar ile günden güne büyüyen bir şirket olan İpliksan, 110.000m2 alan üzerine kurulmuş olan, 42.000m2 kapalı alana sahip bulunuyor. İplik üretiminde Türkiye’nin önde gelen firmalarından olan İpliksan, 5340 iğli kamgarn, 888 iğli yarı kamgarn, ve 368 iğli straygarn tesisleri ile yıllık 5000 ton üretim kapasitesine sahip entegre bir grup olarak öne çıkıyor.
İplik Üretimi Dört Gruba Ayrıldı
Firma bünyesinde günlük 25 ton kapasite ile elyaf boyama yapılırken, elyaf boyama dışında çile boyama, püskürtme boyama ve baskı boyama makinelerinde günlük 6 ton kapasite ile boyama işlemi gerçekleştiriliyor. Faaliyetlerine tüm hızıyla devam eden İpliksan’ın üretim süreçleri ve uygulamaları hakkında İpliksan Genel Müdürü İsmail Şen’den önemli bilgiler aldık.
Fabrika da üretilen ipliklerin dört gruba ayrıldığını ifade eden İsmail Şen, 5000’e yakın farklı ürün çeşidine iplik yaptıklarının altını çizdi. Fantezi, straygam, yarı kamgarn ve kamgarn olarak iplik üretimi yaptıklarını söyleyen Şen; “Kazak, hırka, atkı, şapka, şal, örgü, battaniye, elbise, çorap, tozluk, her türlü bebek ihtiyacını karşılayacak el örgü iplikleri, trikotaj iplikleri, nakışlı pano ve halı iplikleri üretimi gerçekleştiriyoruz” dedi. Şen ayrıca hammadde tedariğini yerli üretimle birlikte Güney Amerika ve Avustralya’dan karşıladıklarını belirtti.
Makine parkını genellikle yabancı firmaların makinelerinden oluştuğunu ifade eden Şen, şöyle devam etti; “ 70 adet boyama hattı makinesi, çile boyama, püskürtme boyama ve iplik baskı boyama şeklinde makinelere sahibiz. Uzun elyaf iplik üretimine uygun 65 adet makineden oluşan iplik hazırlama parkımız var. İplik yapma sürecinde ise 41 adette repco makineyle faaliyetlerimiz sürdürüyoruz. Firmamızda 38 adet yumaklama ve paket ünitesi yer alırken, 10 adet straygam iplik ünitesi de üretimimize katkı sağlıyor. Marka anlamında bakıldığında ise, Zinser, NSC, Wolkman, Saurer Allma, Bellini Campanını, Then, Ekinoks, Croon Lucke’un dışında birkaç tane yerli üretim makineleri bulunuyor.”
Ek Vergilerden Etkilenmedi
Genel anlamda sektörde kullanılan makinelerin yerli üretim olmaması ve Türkiye’ye gelen ikinci el makinelerin yerli üretime göre daha ucuz olması nedeniyle ithal makine kullanıyoruz diyen Şen, yerli üreticilerin krizlerden etkilenen yapıda olduğunu ifade etti. 2008 yılında yaşanan krizin sektörü talep ve üretim olarak yaraladığını savunan Şen; “İhracatta ciddi bir düşüş yaşanmadı, ancak stok tutan müşteriler ihtiyacı olduğu kadar ürün almaya başladılar, bu da zamanlarda sıkıntı yaşanmasına neden oldu” dedi. Son dönemde yaşanan ithal tekstil ürünlerine ek vergi tartışmaları ile ilgili olarak Şen, İpliksan’ın bu uygulamadan etkilenmediğini, pazarda herhangi bir değişme görmediklerini söyledi. 2012 yılı içerisinde küçük makine yatırımları dışında herhangi bir yatırım yapmayacaklarını vurgulayan Şen, sözlerini şöyle tamamladı; “İthal dokuma kumaşlara getirilen ek vergilerin aynı şekilde her türlü iplik alımında da uygulaması gerektiğini düşünüyoruz. Mensucat ithalatı yapanlar iplik ithal edip, Türkiye’de dokuma yapmaya başladılar. İplik tesisi kurma projesi olan ve dışarında haksız rekabet nedeniyle dokuma ünitesinde kullanacağı iplikleri daha ucuza temin edebildiği için projeyi askıya alan devam etmeyen kuruluşlar olduğunu biliyoruz.”
Adım Adım Fantezi İplik Üretim Süreci
El örgü ipliğinin yanı sıra 59 adet kroşe makinesine sahip olan İpliksan, günlük 1 ton kapasiteyle fantezi iplik üretimi de yapıyor. Fantezi iplik boyalı olarak gelen hammaddenin örülmesi ya da boyasız gelen hammaddenin örüldükten sonra faklı metotlarla boyanması ile renklendiriliyor.
Boyama işlemi tamamlanmış olan elyaflar bir sonraki makine olan, elyaf kopartma makinesinde kopartma işlemine tabi tutuluyor. Kopartma işleminin ardından elyaf bantları iplik eğirmeye ön hazırlık amacıyla seri çekim işlemleriyle gerekli inceliğe ulaştırılıyor. Üretilecek olan ipliğin ince veya kalın olmasına göre iki farklı iplik eğirme sisteminde çekilip inceltilerek ve büküm verilerek tek kat iplik haline getiriliyor. Tek kat haline gelmiş olan iplikler, olası hataların giderilmesi amacıyla bu bölümdeki son kontrolün yapıldığı otomatik bobin temizleme makinelerine alınıyor.
Farklı bir iplik üretim sistemi olan repco makinelerinde elyaf kopartma işleminden sonra, elyaf bantları ovalama ve çekim işlemlerinin ardından tek kat iplik halinde katlama ve büküm bölümüne teslim ediliyor. Katlama ve büküm bölümünde ise tek kat halinde gelen iplikler, farklı kat sayılarında ve ihtiyaca göre farklı renklerde katlanarak büküm makinesinde bükülerek güçlendiriliyor. Büküm işleminden çıkan iplikler satış öncesi son hallerini aldıkları bölüme geliyor. Bu bölümde buhar yardımıyla şişirilip daha dolgun bir görüntüye ulaşan iplikler yumak makinelerinde istenilen gramajlarda yumak yapılıyor.