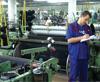
Yünsa launched the Total Productive Management project to increase productivity and profitability. The organisation was held with the slogan of “Kickpoint of TPM” in Çerkezköy factory of Yünsa and hosted Cem Çelikoğlu- General Director of Yünsa, A.Derya Kınık - Technical Vice-General Director, Harun Açıkgöz - Production Executive of Arçelik Factory, Türker Bozunoğulları - TPM Consultant, Sema Kırkoyun - TPM Coordinator, factory workers and the guests.
Senior executives of Yünsa who supported the TPM activities in the event delivered speeches concerning the issue. Taking the floor first, Cem Çelikoğlu, General Director of Yünsa, expressed that this method would strengthen them in the global competition environment. Stating that Yünsa has always become prominent with its ever-growing structure, Çelikoğlu continued his remarks by saying: “We are elevating our targets with TPM efforts. We continue on our way by increasing our turnover amounting to 2 billion dollars in 1998 each year. While we ranked third place among the Turkish wool manufacturers in 1998, currently, we are the biggest manufacturers of Turkey. Besides, we achieved significant sales figures with our export spurt starting at early 1990s. Today, we are the company selling the highest amount of fabric. We are exporting fabric to more than 60 countries. We gained this success with timely and quality production.”.
Our Target is Productivity and Profitability Increase
Emphasizing that they put the TPM activities into practice to ensure productivity and profitability increase, Çelikoğlu also expressed: “Our prioritised target is to eliminate all kinds of loss of our company. We also aim at improving the enterprise parameters and increasing productivity and profitability at the point where the losses are minimised. First of all, these activities should be spread and integrated. This process will last for 3 years.”.
Underlining that TPM activities constitute a corner stone for Yünsa, Çelikoğlu said: “Since 1970, about 100 firms have started to operate in the fabric industry throughout the world. If we had not worked with Germans, we could not achieve this success. We will maintain this success that we caught with this driving force. This will be our most important success tool. In this period, firms should be fast, qualified and cost-effective to survive. In this period marked by competition and timely production, I believe that we will reach success owing to the efforts of all employees.”
Technical Vice-General Director, A.Derya Kınık who was among the executives participating in the organisation also made important explanations. Stating that they decided to continue the quality and productivity journey that they started with EFQM working model in 2006 with a new model in 2012, Kınık also added: “Our aims are to encourage all employees and contribute to the products, production processes, quality and competitiveness.”.
As Production Executive of Arçelik that is one of the firms previously implementing the TPM model, Harun Açıkgöz also expressed his experience in his speech. Reminding that they have been working with this application for 10 years, Açıkgöz expressed that new firms could also raise to a success level in a short time. Emphasizing that success requires patience, Açıkgöz stated that: “We had the same questions in our minds as you have now. Aims are fulfilled after you work. You only desire. The most important part of the work is the administration’s approval. Overcoming the other problems will be the most enjoyable part for you. We believe you will succeed. When Arçelik factory initiated this model in 2001, it was manufacturing 2800 engines. It raised this number to 9 million engines by minimising the investments and without establishing additional plants within the same closed area. Even our employees had not imagined the point we reached today. I wish success for you in the TPM activities and efforts. We will do our best to support you.”.
Autonomous Maintenance Started in Yünsa
Yünsa took the first step concerning the TPM studies. Autonomous maintenance efforts started in the slenter 2 machine, which is a critical machine in the production. Taking on the philosophy of “Who makes a job is the one knowing it”, Yünsa is planning to implement this model in 600 more machines at the end of 6 months.
Giving information about autonomous maintenance, firm executives explained that workers have the competence of dealing with certain processes of equipments and products including maintenance, repair and quality on their own without needing the relevant support teams all the time. While it was stated that autonomous maintenance has 7 steps, field operators and support teams were also expressed to be subject to intense trainings and practices.
Whereas it is thought that the first three steps of autonomous maintenance will be completed in 6 months, 100.000 error cards are planned to be hung with autonomous maintenance activities by the end of 3 years. Besides, Yünsa targets at eliminating almost all occupational accidents, short interruptions, pollution, quality errors etc.
What is the Target of TPM Activities?
TPM is known as a maintenance approach which requires complete participation of employees within daily production activities, envisages autonomous maintenance, prevents breakdowns and maximizes the equipment efficiency. As an original Japan management system, TPM emerged with the name of “Total Productive Maintenance” in 1971 after Japan Institute of Plant Maintenance developed the protective maintenance principles. Used as a tool in the development of industrial production in Japan, this system was even more developed and after 1990s, it was renamed as “Total Productive Management”.
The first firm to introduce and implement TPM in Japan is known as Nippon Denso; the firm received PM Excellent Plant Award owing to its activities. Spreading to the world from Japan, this system was especially implemented successfully in Toyota group. Having two fundamental targets, TPM activities focus on increasing the competitiveness and creating a working place with easygoing environment and high performance. According to the practice, 16 big losses should be eliminated to ensure high productivity. These themes include Breakdown, Set-up (model change), Team Change, Starting, Short Interruptions and Waiting, Pace, Error and Maintenance, Closing, Management, Production Movement, Line Organisation, Logistics, Measurement and Adjusting.