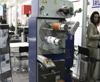
Starlinger, one of the most important textile machinery manufacturers in the global market, keeps standing out with its successful works. The company produces successful technologies on easy usage, high productivity, and low cost and turns out complete production facilities of bag made of polypropylene and polyethylene, PE-hair net and bag production machines, PP container weaving machines, machines required for regeneration facilities of PP-PE and polyester, laminated product facilities, laboratory devices, AD-starKON complete production facilities made of polypropylene, CB-starKON shopping bag, PP-starKON pinch bottom bags, SSP facilities for polyester.
Gaining a successful speed recently especially with Twinstar II automatic winding machine, Starlinger makes a name for themselves with FX 6.0 weaving loom introduced in ITM Istanbul exhibition. Starlinger reached a successful rate at the exhibition held in April and attracted attention of textile manufacturers in the region. Hermann Adrigan, Starlinger Manager, provided evaluations especially for Textil Dünyası Magazine.
Stating that Turkey is closely following the developments, Hermann Adrigan emphasized that the demand of Turkish companies for technology is gradually increasing. He underlined that Turkey stands out as a high quality market and continued as follows; “Turkish demands are based on quality. The companies have been investing in high quality technology for the last 30 years. So whenever we launch a new product, Turks are one of the first coming manufacturers. They are in a key position among the firms with which we are in contact. In this respect, we should support them as well. To give some related recommendations, the companies should head for more automation and high productivity equipments. Because local prices are increasing, labour expenses are growing, environmental standards are raising in the field of weaving packaging and this leads producers subject to certain extra expenses” .
Today the Focus in on Machine Efficiency
Underlying that they are one of the leading manufacturers in the global market, Adrigan provided important explanations on FX weaving loom introduced at ITMA Barcelona as well. Adrigan stated that they have significant experience due to the work carried out for long years, and thus they produce machines according to customers’ expectations. Reminding that Starlinger developed the first circular weaving loom for polypropylene in 1972, Adrigan explained that today focus is not only on speed.
He emphasized that the works for optimization of machine efficiency are taken as basis and pointed out; “It is meaningless to always push for higher production speeds, without these results. FX 6.0 combines high speed with reliable production. To work at high speeds, we needed to make certain technological adaptations as well. Because the models prior to FX were restricted in terms of technical capacities. In fact, these technologies reached the highest speed level possible (approximately 1000 picks). Yet afterwards energy consumption grew rapidly, the service of looms and consumption of spare parts increased, thus operating costs became expensive. So we have developed FX technology to ensure less energy consumption and need of spare parts and achieve higher productivity compared to the previous product even at the highest speed (1150-1250 picks).”
FX is also Tested in Turkey
Adrigan said that they use a technically different technology, and explained that the machine ensures cerylic with the weaving comber organized for production at high speed. Adrigan said that the machine is designed for fabrics in the weight range of 50 g/m² to 130 g/m² and reported; “The use of long-living ceramic elements and heddle wires in the warp compensation, contributes significantly to cut down service and maintenance costs. FX ensures high efficiency and constant fabric quality through electronic tension control and the structure reducing production waste”. Adrigan explained that the loom is being tested now and said; “A certain number of customers chose applied test. They are running the loom under actual production circumstances. As Turkey is a major market for us, there are two customers testing this new technology, here in Turkey. This shows Turkey is an important market for us.”
Demands are for Reducing Expenses
Evaluating the types of machines requested by manufacturers globally, Adrigan emphasized that the customers want to reduce expenses. He said that companies have a lot of demands varying from lower energy consumption to less labour, raw material usage in low quantities, and production of fabric with less weight and reported; “If the adhesion of a single silver is much enough, you can reduce the weight of fabric down to 65 g/m² instead of 70 g/m². And this means tones of raw material saving per customer. Other than these demands, the basic issue is the environment. If we consume fewer resources, less energy, all these components correspond to a lot of positive effects. Thus we consider many realities for our development, this is not a single port or section, we always look at the big picture. I think this is the point.”
Our R&D Studies Set Everyone an Example
Adrigan pointed out that successful machinery production is based on R&D studies and stated “We make assessments in accordance with the demands. We carry out our R&D studies according to the studies performed by us and to market researches”. He underlined that they are operating with 80 employees in total in R&D department and said; “We spend 5% of our annual turnover for reach and development. The equipments of our rivals in operation worldwide are so similar to Starlinger’s. We push this sector. In this respect we keep setting everyone an example.”
Our Market Share is Low in China and India
He reminded that the ultimate aim of quality product produced with R&D studies is sales and provided important information on markets. Adrigan explained that they divide the world into four sections while making evaluations and they are Asia, Africa, China, and India, deemed as a separate region itself. He reported that there are some regions they call as ‘the Rest of the World’ and said; “We consider Turkey in this group. This section covers around 20% of market share. Here the competition level is formed differently. As the equipments used particularly in China and India are of cheap, our market share remains in a relatively low level. Yet there are areas where we are very strong. They are; Africa where we have a market share of 55%, South-eastern Asia countries Indonesia, Malaysia, Thailand. The lowest countries, as I have mentioned before, are China and India. Though, we keep working at full steam. We have activated a production facility in Shanghai close to the center.”
Stating that Turkey is among the first three countries recording the highest turnover, Adrigan said; “We therefore place a particular importance to Turkish manufacturers. In accordance with their demands, we supply our machines from Austria as well”. Adrigan informed us that the annual turnover is realized as around 14 million Euros every year and said; “We have significant targets within 2012. This is based on a turnover target of 190 million Euros. Every year, we have estimated figures showing our possible actions. In this context, we are working hard; yet, there are many factors affecting this. With respect to weaving packaging products, export from Turkey to surrounding countries is very high every year as the production capacity in Turkey is approximately 50% more than the amount that can be consumed by domestic market. So a lot of weaving packaging products is sold outside Turkey. They go to all surrounding countries, to Azerbaijan, Russian countries, Uzbekistan, Kazakhstan, Syria and Iran. Ultimately, this influences the investments. We are glad particularly for that the investments are increasing. We determined a turnover target of 190 million Euros this year, for the whole world.
Recycling Equipments are 25 Years
Starlinger recycling equipments are celebrating their 25th year. In the 25th year of recycling to be celebrated on 18th-19th June 2012, all players of plastic industry are invited. The organization will be held in the factory building in Austria where technical presentations and live tests will be performed. The world’s biggest plastic bottle recycling line currently recoSTAR PET 330 İV+ and, recoSTAR universal 165 VAC designed for fiber and nonwoven junk recycling will be seen in working status during the organization. Many experts, suppliers and representatives from all over the world will be present at the organization in order to obtain first-hand impressions of the technology required for quality plastic recycling.