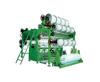
**
Having an important place in the warp knitting and warp preparation machines in the global textile market, Karl Mayer offers innovative solutions to the textile manufacturers with its machines.
Taking important steps after buying LibaGMBH, Karl Mayer introduced its new portal working with the principle of zero waste.
Targeting to increase its share market thanks to the weft insertion portal that it developed in an environment where production costs are high for the high performance yarns demanded by the fast-growing technical textile market, Karl Mayer offers efficiency and flexibility in the weft preparation owing to its portal. With the new portal, yarns can be manufactured as 90º – or 0º- and 90º. A significant amount of money is also saved in terms of production costs owing to this portal allowing for processing such highly resistant polyester fibres as carbon, glass and aramid.
Multi-Speed
Thanks to the new portal, maximum material yield is ensured and the most important systemic innovation was made in the yarn clamps. In this system, any waste occurring during weft insertion is prevented and the weft can be inserted into the machine on both sides in the direction of the stitches. Therefore, the creel found on both sides of the machine is prevented from making empty runs during the weft insertion process. In the system where a transport chain in integrated to synchronisation between 20” weft yarns and creel, additional feeders are also integrated between the stitch line and weft line in order to avoid cutting-off of the creel. In this way, detailed settings can be made during the weft insertion process. With this flexibility of the process, MultiSpeed function can also be used without stopping the process.
Thanks to the configuration process made in the electronic environment, it enables the values for feeding in the knitting and 0º reinforcing yarns, the take-off values and the movement of the transport chains is adjusted to suit the requirements of the pattern. The distance between weft yarns and transport chains that can be operated continuously or at intervals can be adjusted separately.
Production Costs Are Minimised
When the new portal is compared to the traditional version operating with continuous weft, this system minimises the production costs with zero waste weft insertion. Offering more flexibility in comparison to the conventional systems, the new portal offers a wide range of products. When using the portal weft-insertion machine compared to a 138"-wide machine with an 18 x 3/4" weft insertion, the amount of waste prevented is approximately 9%.
Electronic guide bar can be added upon demand in the new portal operating with a touch-screen operator console and servo-controlled take-off system. Another feature of the new portal is that the number of additional process steps is reduced and production process is facilitated.
Making explanation about the issue, Marcus Kube stated that Karl Mayer which constantly develops its structure as a family company has reached to the leading position in the warp knitting machinery sector and added that new standards were set in relation to warp preparation equipment in warp knitting and weaving. Stating that the optimum yarn tension reaches up to 45cN from 2cN thanks to the developed portal, Kube expressed that they are working on new innovations in this field.