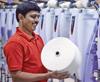
The new Autocorner 6 equipped with the improved process intelligence developed by Saurer Schlafhorst ensures higher productivity and energy saving. The most significant feature standing out in the sixth generation of Autoconer is that it is able to develop itself thanks to the automatized process flows. In this way, efficiency, resource productivity, quality and process assurance are obtained.
Smart working style of the new Autoconer ensures stable productivity at the maximum level while allowing 6 % higher productivity. Autoconer 6 which can speed up without running idle owing to the acceleration improved with the technology developed by Schlafhorst reaches the maximum bobbin winding speed in the shortest time possible. In Autoconer 6 where unproductive piecing times are minimised, anti-patterning is designed in a manner to improve productivity.
Another striking feature of Autoconer 6 which has a material flow system is that it ensures 100 % work labour on the bobbin winding units even though fluctuations occur in the material flow. Ensuring a more reliable, faster and thus, more productive cop change in RM machines with 9+1 cops found on each bobbing winding unit thanks to its innovative cop change system, Autoconer 6, with its maximum 80 bobbin winding units, can increase productivity per square meter by 9 % when compared to a machine having only 60 bobbin winding units.
More Productive Production
Thanks to its high-productive new suction system motors, Autoconer 6 reduces energy consumption with such components as smart control systems and aerodynamically improved suction tubes and minimises yarn waste. Consuming 6 % less resource in this way, Autoconer 6 offers apparently high resource efficiency thanks to its new suction tube while offering such features as fast and reliable upper yarn pick-up, reduced operation frequency and period, automatic and self-regulating suction tube position equalisation to the use of the textile sector. In Autoconer 6 where FlexiCycle intensifies upper yarn search, various parameters including the suction tube distance, intensity and extent of vacuum or the search time can be adjusted flexibly.
In Autoconer 6 which pressure mechanism controlled by sensors generates only required amount of pressure, suction system switches automatically between the need-oriented higher operation pressure and energy-saving static pressure for more reliable yarn pick-up. Autoconer 6 where parameters can be adjusted individually ensures an additional saving in pressure air since blowing impulses aimed at cleaning the bobbin winding unit through Multi-Jet are adjusted via Informator in accordance with the actual contamination degree.
Smart Material Flow
The smart system in Autoconer 6 which does not require manual adjustments distributes the carriers to the bobbin winding units in a totally independent manner and ensures that the number of spare cops range between 1 and 3 depending on the situation. When feeding falls short for a while in one of the bobbin winding units, Autoconer 6 can pass to high-speed feeding under the control of sensor if needs be. Balancing the fluctuations in the material flow 100 %, Autoconer 6 accelerates feed change by 25 % since each bobbin winding unit is fed by the first cop necessary for the start of the production without continuing the loading of spare cops.
X-Change, the cross bobbin changer found in Autoconer 6, has unique smart functions in the market with its multiple bobbin manipulation feature and smart empty bobbin strategy. Autoconer 6 learns on its own how to best grip the bobbins in the first practice and records this information on Informator and in this way; process assurance can be improved by minimising the outfitting durations. Autoconer 6 stands out with its change capacity thanks to X-Change changer which has smart movement path improvements, smart pre-demand mode, relatively short positioning time and 10-seconds sensational change time.
Autoconer 6 is the only machine in the market having two systems for electronic yarn pull force control with TensionControl and Autotense FX. TensionControl detects the course of a typical yarn pull force in the cops of an actual lot in a reference bobbin winding unit and can calculate a yarn tension graph for the lot data in the Informator by using the measurement data. Following this calculation, appropriate control instructions are transferred to the whole bobbin winding units. In this way, Autoconer 6 obtains much more homogeneous bobbin intensities and higher productivity when compared to the machines not equipped with yarn pull force control and ensures the appropriate performance level for commodity applications.