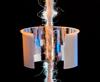
Quality expectations of textile and fabric manufacturers for fiber yarns continue increasing. Foreign matters found in the fiber during the production process or raw material selection lead people to question the quality of the products. Highness of contamination rate of yarn or cotton triggers the process which ends up with the cancellation of orders by the firms. Measurement of yarn parameters which are of great importance in terms of textile production also enables firms to elevate their graphics in sales.
Researches regularly conducted by the International Textile Manufacturers Federation reveal that cotton production is still maintained with a high contamination rate. Problems encountered in collecting and transporting raw materials and and lack of full controls over preparation processes cause undesired contamination problems in yarn production in enterprises. Synthethic, animal and plant wastes of different colors which can not be eliminated completely through the process of bleaching and the resulting contamination lead to serious problems in especially white fabrics manufactured out of cotton yarns. The presence of foreign matters from 13 % to 35 % even in the cotton manufactured with machine indicates the severity of the problem.
A Definite Solution for Contamination: Loepfe Brothers
Additional sensors are needed to clean the contamination on the yarn. Swiss-centered Loepfe Brothers Ltd. which has introduced innovative technologies in this field continues adding new products to the Yarn Master family which drew a great interest from yarn manufacturers. The firm meets quality requirements of yarn manufacturers with Zenit C series, in particular. Color controlled “ZenitFC” and additionally synthetic foreign matter controlled “ZenitFCP2” cleaners offer solutions for quality problems in cotton, viscone, polyester, melange, acrilic yarns and their white and colorful blends. Since 1991, Loepfe has been one of the leading companies in detection of foreign matters. It detects foreign matters safely and reliably with its latest technology product YarnMaster ZENIT FP. In its latest product, the cleaned raw material is dyed with melange discontinuous yarns. This feature also enables all the dark and light colored matters to be removed.
Defect Frequency is an important parameter
In addition to its innovations, it also provides a foreign matter cluster channel with ZENIT FP yarn clearers. When the need to cut out the remaining foreign matters in the yarn arouses, the additional clearing tool is used. While the frequency of such problems poses an important obstacle for quality yarn production in firms,the F Cluster Channel offered with ZENIT FP ensures controls over lines. Observation length can be chosen between 0.1 and 80 m and this feature brings the advantage of adjusting the maximum fault number in accordance with the market requirements.
Offering solutions for removing white polypropylenes (PP) in cotton yarns, Tribo-electric yarn clearing technology is among the most popular products for users owing to Loepfe’s ZENIT yarn clearers. The effect of tribo-electric is defined as a type of communication electrification where certain materials which come into contact with a different material get charged with electric and then get separated. In blended cotton yarns, white PP faults can be detected through Tribo-electric sensor. Thus, Yarn Master ZENIT FP yarn clearer can detect foreign matters including polypropylene, polyetilene, polyamide etc. With its 3 sensor technology, ZENIT FP makes a slight abrasion effect on the yarn even at high speeds while any processed material passes through the yarn route. 7-segment indicator also provide cost saving in addition to a fast intervention. The new generation ZENIT C FP2 yarn clearers continues being leader in the market in its successful sales figures in the global market.
Real Benefits to Clients with P2 Sensor
It is known that synthetic foreign matters are removed mostly through P2 sensors integrated to the system. Having no connection with the color measurement sensor, this sensor acts completely independently. Not affected by the settings of the color measurement channel, the sensor works on the basis of measuring the static electricity generated through friction. P2, the second generation polypropylene sensor developed with intense R & D activities, almost removes the unnecessary cuts and at the same time, increases clearing performance by almost 3 folds. This feature allows a clearing of 80-95 %.