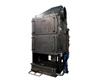
The finishing treatment of woven and knitted fabrics includes the usage of stenter frames. But stenter frames are causing high energy consumptions as well as creating high amounts of hot fumes, containing oil smoke, fibrous materials and a valuable amount of waste heat from production processes. Therefore, KMA Umwelttechnik GmbH - located in Germany and specialized in industrial air purification - is now introducing on ITMA 2015 in Milano a new developed solution for exhaust gas treatments of stenter frames.
The new KMA ULTRAVENT® exhaust air treatment system is pursuing three objectives: on the one hand, KMA ULTRAVENT® exhaust air filtration systems ensure the highly-efficient cleaning of the waste air before it is lead outdoors to avoid nuisance and pollution by emissions. In addition, it recovers the heat contained in the airstream. The recovered heat can be used for heating the supply air or the service water. As a third objective, the oily particles contained in the exhaust air can even get discharged and deposited by a drainage outlet.
Special Design
KMA heat exchangers are fin tube heat exchangers, which enable highly efficient heat recovery of process heat from the exhaust air. Double-module finned tube heat exchangers are used when the air temperature is high. Exhaust air less than 130 °C can also be treated with one module of the fin tube heat exchanger. The recovered heat can be used to heat up the stenter´s incoming air or for heating domestic water (e.g. in laundry or dyeing). For the use of the recovered energy supply air devices and water/water plate heat exchangers are available.
The KMA electrostatic precipitators are industrial electrostatical filters for highly efficient separation of oily or sticky substances (e.g. smoke, mist, dust and greasy particels). The filter cells are characterized by the particularly robust design: frame and carrying bars made of stainless steel, insulators in oil-resistant ceramics. Due to the unique design the exhaust air can flow through the electrostatic filter with almost no pressure loss. Clogging of the filter cells by dirt and fibrous materials is thus impossible and filter replacement is not required. Separated materials, such as oil, can continuously drained into an oil collector tank and be recycled again. The cleaning of the filter takes place automatically in regular intervals.
CIP
Below the filtration machine there is a water tank and a pump for the CIP washing device. It allows the regular and labour-saving cleaning both of heat exchangers and electrofilters. Washing time and all other parameters are programmable by a PLC controller. The automatic ULTRAVENT® washing system is unmatched in terms of comfort and cleaning results. The clean gas quality with KMA ULTRAVENT® systems is according to EU standards. Therefore, the clean gas emissions of the company are below 10 mg/m3. The KMA filtration system operates with low energy consumption. The consumption of electric energy is less than 0.1 kW/1000 m3 exhaust air. There is an energy recovery with the heat exchangers of max. 650 kW/h.
The above figures show, that environmental protection does not necessarily entail excessive additional costs. On the contrary: this smart solution is an ideal link between ecology and economy, as it leads to a huge improvement of the air quality and the company´s carbon footprint. At the same time it brings a significant cost advantage by cutting energy costs and recovery of oil. When operating in 3 shifts, the investment of the above project will pays back in less than 1.5 years.
First Filter System in Kırayteks
Kirayteks, a leading textile manufacturer in Bursa/Turkey, purchased one of the first filter units of the new KMA ULTRAVENT® systems. Kirayteks is operating with a 6-field stenter, which creates an exhaust air volume of approximately 18,000 m3 per hour. The exhaust air contains high concentrations of oil fumes and has a temperature of up to 180 °C degree. In most cases, companies lead the valuable waste heat outdoors without recovering and reusing it in an economical way.
At Kirayteks the new ULTRAVENT® exhaust air filter system is placed on an assembly platform above the stenter frame and linked with the already existing exhaust air pipework of the plant. If there is no place above, the KMA ULTRAVENT® filter system can also be installed beside the stenter machine or outside of the factory building. The exhaust air flows from the bottom of the filtration system to the top, while passing two steps of heat exchangers and two electrostatic precipitator sections. Due to the low pressure loss of the filtration system the original ventilator of the stenter frame does not need to be replaced.
Close Up: KMA Umwelttechnik GmbH
KMA produces filtering systems for the use in many different industrial sectors. Filters and controls designed by this company show a low energy consumption as well as an ability to remove pollutants completely. Over the years this techniques have been awarded with several environmental prices. Every year, the firm invests a major part of its resources into further developments of its products. Close collaborations with customers have a high priority at these developments. Customers are seen as important providers for new ideas and inspirations, who can actively support developing processes. In addition, it cooperates with public research institutions and universities.