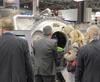
Being one of the biggest dyeing and finishing machines in the world, CHTC Fong’s exhibited its latest technologies with the brands of Then, Goller, Xorella and Fong’s at ITMA Milano.
All of the innovations offered to the interest of the visitors include one-stop sustainable solutions and automation solutions ensuring smart and e-solutions management at the same level.
FONG’S JUMBO TEC 3 2T
JUMBO TEC 3 2T which is TEC series high temperature dyeing machine exhibited by Fong’s offers low cost, high quality and sustainable production process to the manufacturers. It can also be used in the dyeing processes of natural and man-made fibres.
Offering efficiency, energy saving and environment-friendly solutions, JUMBO TEC 3 2T has 40S/2, 26S/1 and 20S/1 models and they can be used in dense knitted fabrics and can prevent crease marks in sensitive structures. Ensuring a high level of energy saving, JUMBO TEC 3 2T can perform reactive dyeing process for cotton fabrics with light colours in 248 minutes. In TEC series which include such options as JUMBOTEC for 300 kg, MIDITEC for 250 kg and MINITEC for 200 kg, enterprises can choose a machine with arrangements from 1 to 12 depending on their capacities. Performing different and various dyeing processes like natural and man-made fibres and blended products, the machine was specially designed for tight, break-less and delicate fabrics. With various new functions, the machine completes the cotton reactive dyeing process in a relatively short time.
Thanks to F 30 coloured and multi-function controller, the temperature deviation in the dye could be minimised at +/-0.3° C. Besides, Lint Collector – the fibre collection system is one of the most important features of the series. With the patented design, such loose fabrics as terry and fleece can be processed and the lint can accumulate under the collector and can be discharged during draining and thus, there is no need to clean the filter manually.
FONG’S SUPERWIN 145
Developed as a result of the works conducted for the increasing environmental sensitiveness, SuperWin high temperature single flow package dyeing machine consumes less water compared to the traditional dyeing machines. Its efficiency in the dyeing process has been increased with the pump and motor system specially developed for the machine.
Introduced at ITMA Milano, SUPERWIN offers an environment-friendly production process and is also suitable for all material types like package, warp beam and loose fibres. During an inside-out flow process, dry liquor discharged from the pump enters into the carrier and passes through the spindles. A small level of water is required at the bottom of the kier to maintain the regular working of the pump. There is no need to immerse all packages with liquor. Besides, revolutionary wavy dyeing ensures that pumping frequency is kept at a highly specific period. This creates a wavy pressure difference leading to the effect made actually by the dual flow concept in packages. In this way, dyeing process could be realised at a lower liquor ratio of 1:3.
In the machine where dehydration technology under pressure is used in order to reduce production costs, the moisture rate is low and saving is ensured in drying. At the same time, it shortens the process by 30 minutes when compared to its rivals and saves a significant amount of cooling water.
THEN SUPRATEC LTM
Another innovation exhibited by CHTC Fong’s at ITMA, THEN SUPRATEC LTM can realise the dyeing process of delicate and heavy fabrics through the water technology it is based on. The machine was manufactured as an innovative model as a result of the technology and experience of Then and Fong’s. THEN SUPRATE LTM is a hydraulic long tube dyeing machine with a varying liquor ratio from short in semi-dry mode to long in wet mode.
Bringing new standards to long tube dyeing with its varying angle, defined plaiting without winch and liquor ratio, the machine can realise the dyeing process of all woven and knitted fabrics made out of man-made fibres and blends. The machine, whose weight can range from 25 gr to 380 gr, saves significant amounts of water and energy owing to its liquor ratio. Depending on the fabric type, the machine has a speed range from 80 m/min. to 600 m/min. as well as the following features:
- Liquor ratio ranging from 1:5.5 to 1:15 depending on the angle of the kier;
- Low energy consumption depending on the angle of the kier;
- Up to 3 jets with 1000 meters of fabric each per tube depending on the fabric weight;
- Varying nozzles.
THEN-AIRFLOW® SYNERGY 8
THEN AIRFLOW® SYNERGY 8, the high temperature aerodynamic piece dyeing machine exhibited by Fong’s makes a significant energy saving. THEN AIRFLOW® SYNERGY 8 where each tube is manufactured as having a separate frequency controlled blower requiring less installed power has an outstanding liquor ratio. THEN AIRFLOW® SYNERGY 8 reduces water consumption, shortens cycling and ensures a high level of reuse. While up to 12 tubes can be found on the model, it offers advantages of flexibility, quality and ergonomics in numerous different fabrics.
Redesigned Automatic Chemical Dispensing System (CHD)
Redesigned Automatic Chemical Dispersing System (CHD) takes less space in the dye house thanks to its compact structure. Patented dispersing system and Colour Kitchen Manager (CKM) ensure completely automatic measurement in CHD where transporting, dispersing, and weighing and storing of liquid and powder auxiliaries as well as dyestuff can be carried out.
Detecting and preventing all possible errors beforehand, CHD allows transferring chemicals in small or large amounts. Using extrusion pumps to ensure automatic dosing and best reproducibility from batch to batch, CHD also saves water thanks to its low liquor ratio.
Capable of reducing chemical costs by 202 %, CHD also prevents contacts of operators with the chemicals threatening human health in addition to reducing labour force costs. Thanks to its redesigned structure, its environmental risk has been minimised and CHD can optimize the chemicals used and ensure control.
Coriolis flow meter used by CHD provides a high accuracy level of ±0.3% when compared to the magnetic inductive flow meter having a level of around 1 %. Dosing chemicals and liquid dyestuff in quantities from 50 ml to 100 litres, CHD ensures repeatability thanks to the computer system.
GOLLER ECONOMICA
The new Goller Economica Dye Padder introduced by Fong’s at ITMA offers pad-batch dyeing technique for the knitted fabric without any creases and breaks. Guaranteeing the highest standards in reproducibility and handling as well as a smooth and clear fabric surface after dyeing, Goller Economica operates in line with the principle of swimming rollers with its deflection controlled rollers. Large fabric guiding rollers ensure a safe transport with little tension. Guaranteeing an even dyeing at the end of the dyeing process, the machine helps keeping the temperature of the dye bath appropriate thanks to the thermal plates. Owing to pre-mixed dyestuff-alkaloid precise dosing, Goller Economica ensures precise and homogeneous pick-up application and linear nip of the deflection controlled rollers. It can give the best results for open width knitted fabrics.
GOLLER SINTENSA
GOLLER SINTENSA by Fong’s that changes the standards in the textile sector offers the most appropriate production process for the technical textiles in addition to carrying out continuous processes of the knitted fabrics. Thanks to the drum-rotor system forming the basis of the newly developed concept, it produces more washing mechanics than the other drummed washers. This leads to shorter process times and less use of water. Also having a higher washing capacity than the other washing drums, GOLLER SINTENSA pioneers short process time as well as washing power and ensures high washing efficiency in the transport of delicate fabrics.
XORELLA XO TREND
Exhibited by Xorella manufacturing yarn conditioning and heat-setting machines, XO TREND series consists of XO SMART and XO SELECT. Complementing one another, these two machines have small capacities and manual handling feature for fully automatic vessels integrated in transport automation and packaging systems from various suppliers. Equipped with the waterless vacuum system, the machines save a significant amount of energy when compared to their rivals through the XO-heating system.
For low temperature applications, XO TREND series ensures 20 % space saving thanks to its structure. Being suitable for pin trolleys and pallets up to 1800 m height, the series significantly reduces the energy consumption thanks to its cylindrical vessel. It can also optimize all components thanks to the improved isolation and coating.