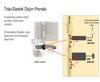
Quality expectation of textile and fabric manufacturers for cut fiber yarns is increasing day by day. Such improvements and innovations as better carding and pileless yarns have improved the appearance of the yarn while this situation has contributed positively to the quality of the fabric. However, problems during the collection and transport of raw materials and the failure to control preparation processes completely leads to undesired contamination problems in yarn manufacturing in enterprises. Agents and colors found on the yarn except for its natural raw material are identified as contamination.
Synthetic, animal,herbal wastes and contaminations of different colors which can not be removed completely through the process of bleaching lead to serious quality problems in white fabrics manufactured out of cotton yarns. Besides, after the fabric is dyed, colorless and white synthetic foreign agents cause costly returns. Foreign matters, from which contamination originates, lead to breaks in yarn by creating weak points. Thus, contamination should be cleaned during winding as much as possible in the high quality products. Although each cut causes production loss theoretically, errors left on the bobbin lead to uncomparably serious harms. In yarns produced out of mixed and dyed fibers, raw materials which can not be opened completely during carding, foreign matters in the raw materials, contamination which occurs during production and flies are reportes as main problems.
Yarn Quality Increases with Loepfe Brothers
Additional sensors are needed to clear the yarn of contaminations. Making innovative technologies in this field, Swiss centered Loepfe Brothers Ltd. company added a new product to the family of Yarn Master which draws great attention by yarn manufacturers. With the Zenit C series, it responses to the quality need of manufacturers. ZenitFC which is the color control of Zenit C series and additionally ZenitFCP2 which is the synthetic foreign matter control of ZenitC series solve the quality problems of cotton, viscone, polyester, acrilic yarns as well as their white and mixed mixtures.
Last fraction of Yarn Master Zenit yarn cleaners, Zenit C has improved microelectronic equipment and self-measurement algorithms and it assures maximum cleaning. With diameter measurement optic having the structure of improved infrared sensor, all the pyhsical yarn errors, yarns with high roughness and pileness are cleaned . detailed cutting and classification information are given about the appearance of yarn and splices and the enterprise is enabled to make the desired settings. Owing to the sensitivity of optic measurement, winding of cops on the bobbin is prevented in compact yarns and quality control is made and thus, yarn machines are monitored more easily.
Correct Referance Correct Cutting for Quality
The measurement principle developed by Loepfe basically reads the color of the wound yarn and records it as reference in the system. Each one of 8 bright led lights placed both sides of the yarn is controlled separately. To enure that sensor chooses yarn as main value, levels of front illumination leds and rear illumination leds are adjuested and balanced separately for each spindle. Thus, the yarn color is equalized to the referance. This process is renewed at each type change and control continues during operation. Thus, contaminations which may occur are considered and a constant correct measurement is guaranteed. Reflection caused by the foreign matter of a different color on the yarn while it passes through the sensor is perceived by the sensitive sensor. As the foreign matter thickens and its color darkens, signal increases in the sensor and with these information, microprocessor decides on the darkness and length of hthe error.
All changes occuring in the yarn color by the system are classified according to the colors tones and lengths and offered to the user. Sensor structure which enables a measurement of the same ratio for all colors guarantees maximum cleaning. On condition that contaminated raw materials are used during production, enterprises are known to use the available systems at the most sensitive settings by being obliged to limit the cuttings. When there is no problem about total cuttings, ZenitC cleaners enables the user to increase the cleaning ratio by increasing the system sensitivity.
As referance yarn is colorful and even the combination of different colors in dyed and mixed yarns, using these yarns is more difficult. Microprocessor uses a different algorithm to determine a correct referance with F sensor which is the product of a long experience and high technology. Sensor which uses 8 led lights in total makes a different calculation from the method used in cotton yarns and enables the system to adjust the yarn as referance. This time, front led light is stabilized but the rear led lights make the necessary adjustments. Therefore, the user can clean the errors completely without imaginary cuttings. For only color and polypropylene cleaning, 16 measurement values taken from the yarn are evaluated by using the improved algorithms.
Blockage to Polypropylene
It is stated that synthetic foreign matters are cleaned at a high level with the P2 sensor integrated to the system. Sensor which has no connection with the color measurement sensor functions completely independently. Not affected by the settings of the color measurement channel, P2 sensor works on the principle that statical electicity caused by friction is measured. While natural fibers lead to very low electrical loads due to friction, such synthetic matters as polypropylene cause excessive loading.
The second generation polypropylene sensor P2 developed by intensive R&D studies eliminates almost all unnecessary cuttings and at the same time, increases cleaning performance by about 3 times. This enables a cleaning of 80-95 %. Inserted instead of the yarn guide used in normal conditions, P2 sensor cleans the statical electrical loads during the production. As the special method is independent from the color, the system detects foreign matters such as transparent,white or colorful polypropylene alone and achieves a high cleaning even in the excessive raw materials.