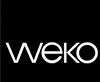
Textiles and nonwovens can be optimally retouched depending on the application of liquid functional materials: hydrophilic / hydrophobic or oleophilic / oleophobic finishes, softeners, flame retardants and anti-microbial products, etc. provide the desired properties.
WEKO’s Fluid Application System (WFA) offers the right solution for sustainable textile and weaving. This technical system developed in Germany can apply non-contact functional fluids with fast rotating rotor discs that spray ultra-fine micro drop droplets into the material web. The encapsulated WEKO ProTec offers an ultra-clean precision to prevent undesired escaping of aerosols and a working environment.
Contact-free Application
The contactless spray application developed by WEKO is handled very carefully because it does not apply any mechanical stress on the fabrics by squeezing between the rolls. There is no need for expensive post production during high quality textile production. WEKO Liquid Application Systems (WFA) only applies the required amount of textile chemicals. Significant reduction of chemical auxiliaries is particularly important for a continuous production of textile and nonwoven surface treatments. WFA can be saved with liquid application systems, because it is possible to use one-sided and surface application when required.
Cost Reducing System
By contrast to the buffering procedure, an amount of damp about 70% is held by the fabric even after it has been tightened. In comparison, WEKO's non-contact application system provides cost savings around 15% to 25%. Consequently, the textile finishers require significantly less drying energy and energy savings up to 60 % are feasible. Alternatively, the reduced energy required during drying allows obvious increasing machine speeds, sometimes even up to 100 %.
Also, depending on the required processes, some fabrics need to be cut several times (two or three times).
To reduce this waste and on the other hand increase the material output, WEKO has developed his cutting system Cut-it 2.0. With special fabric guiding, decurling and stabilization solutions, the cut selvedge can be reduce up to 80% compared to common cutting systems.