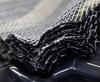
Carbon fiber receives high demand in the automotive industry due to its durability, anti-corrosive features, low weight and thermal expansion and consequently this let SGL Automotive Carbon Fibers and BMW to act. The two giant names of the automotive and carbon fiber production industry made an investment of 200 million dollars in order to inaugurate the world’s largest plant in this field. Thanks to this investment, it is planned to increase the production capacity to 9 thousand tons from 3 thousand tons. The fiber yarn to be manufactured here will be processed in Germany.
A Smart Material Mix
CEO of SGL Group, Dr Jürgen Köhler stated that the new investment realized with BMW will re-define the standards in carbon fiber and underlined that the carbon fiber is very important for the future of the automotive industry. Technology Development Responsible and Board Member of BMW, Klaus Draeger indicated that sustainability is more important nowadays and the interest for lighter and more economic vehicles in terms of petroleum consumption in order to reduce carbon emissions has increased considerably. In that sense, Draeger pointed out that carbon fiber gained more importance and said that they want to use carbon fiber which is 50% lighter than steel and %30 lighter than aluminum but stronger in their sports models and electricity cars. Draeger reminded that BMW manufactured a steering wheel, a single part drive shaft made of carbon fiber and a carbon fiber alloyed hybrid wheel rim and noted that they are researching ways to make use of carbon fiber in serial vehicle production more and more. Draeger also said that they are trying to reduce the vehicle’s weight with the effect of the automobile manufacturers’ strict fuel consumption economy and emission regulations and added that they will prefer a smart material mixture including strong steel, aluminum and carbon fiber.
3 Times Stronger than Steel
Carbon fiber, which is frequently mentioned with its production by Aksa in Turkey, is now preferred intensely for aircrafts, satellite systems, personal protective equipment, pressurized containers and automotive industry and their use increase in the world. Carbon fiber is among the world’s most durable elements and has a very high added value and is a strategic product. The main compounds of carbon fiber are carbonized acrylic fiber, tar and nylon. The molecular structure of carbon fiber is like a honey comb and thus it is 3 time stronger than steel although it is 5 times lighter than steel.
The need for carbon fiber in the whole world is expected to increase to 80 thousand tons by 2015 and to 160 thousand tons by 2020. Carbon fiber being a light, anti-corrosive and nonflammable is a nominee for being the main material of daily products. Carbon fiber, which is also the raw material of composite industry, rapidly increases its use especially in the automotive industry. In the Electric Vehicles (EV) named as “city car” and hybrid consuming 1 liter in 100 kilometers, carbon fiber is heavily used.
It is Possible to Transport 400 Passenger Without Cost
Aviation industry is among one of the industries heavily using composites. The use of composites in the production of new generation aircraft bodies increases rapidly. This rate can increase by 50% today for A380 from 10%. Helicopters carrying load and the back gates of aircrafts are made of composite. It is seen that the use of composite increase in marine industry, especially in yacht industry. In Norway, a ferry boat manufactured of composite material is 40 tons lighter than similar ferry boats. 40 tons mean carrying 400 passengers without cost. Carbon fibered weavings combined with phenol resin are used in thermal shields and rockets and ballistic vehicles as they are fire-resistant. Carbon fiber and carbon composites are preferred in rocket motor parts, beds and nuclear applications as they perform better mechanical features than graphite.