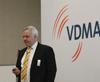
Monforts developing technologies in technical textiles finishing process supports considerably the Bluecompetence approach. Monforts focusing on technological solutions to increase customer’s energy efficiency made a presentation titled “Profitable coating technologies for automotive textiles” at VDMA’s conferences in Istanbul and Gaziantep. The presentation made by Monforts New Business Development Manager Juergen Hanel dealt with the functionality of Monforts machines in the production of technical textiles in the automotive industry. Hanel is known for his experience dating back to many years in the research and development of textile coating and emulsion polymerization.
Monforts being one of the most important companies in textile machinery production and export since 1884 signed numerous patents and leading studies in textile finishing. The company, that is in a strong position in the global market in continue dyeing and textile finishing, developed new technologies for technical textile with dense R&D studies. In general Juergen Hanel highlighted the energy efficiency application systems, coating, Eco Applicator, Heat Recovery, Eco Booster, Energy Recovery and Energy tower issues in his presentation.
Hanel indicating that textiles are present by 19% visibly within automotives underlined that composite products are not included within this rate. Hanel also drew attention on coating issue in application systems for energy efficiency. Hanel stating that many machines were developed for coating continued; “A Coating machine can be installed in front of a stenter. The cost is approximately 70.000 – 180.000 Euros in different suppliers. The energy savings of coating machines are quite high. New products can be developed by adding to these machines,” he said. At his presentation Hanel explained the operation of a multi-functional coating machine for automotive, carpet and vehicle furniture. Hanel indicating the energy savings in textile, padder, pasta coating and foam coating issues expressed that in textiles like vehicle seats only vaporization happens and that there is an energy of 555 kj in padder and 16 kj in foam coating.
The Eco Applicator Creates Difference in Coating
Juergen Hanel informing about Matex Eco Applicator developed by Monforts indicated that it has a unit reducing significantly the inferior humidity content in the drying process. Hanel; “The Eco Applicator is used to expand the water based liquor applications and reduce energy costs. The reduction in the consumption of finishing chemical is not the goal of this development, but can in individual cases be a positive side-effect,” he said. Hanel providing information about the Eco Applicator’s interior layout and working principle indicated that ECO Applicator has been developed as an alternative to the impregnation system with a history of 70 years.
Hanel summarized the technical features of the Eco Applicator as follows; “While there is around 65 percent chemical use during the processing of cotton in the impregnation system, only required amount of chemicals are available in the Eco Applicator system. Due to the high volume of bath in the impregnation system, more chemicals have to be used for the fabric. However, the amount of chemicals can be controlled precisely depending on the prescription in the new system. Thus, providing 20-30 percent less chemical usage, the system also saves energy by 40 to 45 percent. In this system, the liquor can be applied to the fabric in 3 different ways, on one side of the fabric, on both sides of the fabric, two different chemicals on the two sides of the fabric. Using Trough (Flat) and cylinder techniques, the system applies only required amount of liquor / coating contacting with the fabric with a new cylinder,” he said.
Energy Efficiency Increases with the Eco Booster
Juergen Hanel providing information about the new heat recovery module, the Eco Booster HRC drew attention that the system is designed as a fully automatic system. The new module actually cleans automatically the stenter during operation thanks to its design; eliminating standstill times for maintenance. Hanel; “Consuming less material, showing a stable operating performance and failing less thanks to the cleaning filters, the system can be integrated into the roof of Montex. The system does not need extra ventilation assembly,” he said. Hanel indicating that the system pays back itself in a year underlined that the system cleans itself in 20 minutes.
Hanel mentioning about the heat recovery system integrated to a Montex 6500 stenter indicate that eat recovery systems became a standard feature in Monforts machines. Hanel introducing Energy Tower 7000 informed that this tower has a versatile and flexible design and is used within the frame of heat recovery principle. Hanel underlined that the module drews in the exhaust air from the drying process and returned it via heat exchangers to the range so that the air was preheated to around 90°C and only had to be heated to 150°C, therefore the high drying temperature was reached more quickly and energy costs were reduced. Hanel added that The Energy Tower 7000 is not suitable for the following processes with VTG and Thermex.
Juergen Hanel ended his words as follows; “Choose the best technology in terms of both technical and economical aspect. By using the Eco Applicator for foam coating you can reach your goals. Heat recovery systems require a new machine. Calculate the energy savings to reinforce old lines.”