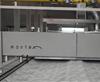
Developing technologies for the technical textile finishing, Monforts completed the installation of the new stenter frame Montex 6500 in the plant of Döhler S.A., one of the leading home textile manufacturers of Brazil. Operating on its plants covering an area of 220 thousand square meters, Döhler S.A. saved a significant amount of energy owing to this investment.
Higher Efficiency
Continuously adding innovations to the stenters it manufactures in line with the developments in the finishing sector, Monforts added such features to Montex series as Masterguide, integrated weft straightener, fabric needling and drive fabric pressure units, moving V steamer unit, fabric centre supporting rope, idle circuit edge starching unit and Glue Flue for fabric edges for optimal adjustment of the treatment process. Montex series can be operated with direct gas heating system, hot oil heating system, steam heating systems, electro-stream combined heating system, hot water heating system and electro heating system and thus, ensures higher efficiency and uses less energy.
Being capable of operating for a long time without lubricating thanks to Hercules chain, Montex series machines can also be supplied with Twin Air Plus which increases the economic performances of the stenters in line with the demands of the customers. In this way, production speed can be increased up to 20 % without a change in the energy consumption.
We Need New Technologies
Making an explanation about this issue, Ingo Döhler, General Director of Döhler S.A., said that they are planning to double their training capacity in 5 years and added that, “In this direction, we need new technologies to improve our production techniques. At the same time, we have to take the increasing energy costs into consideration. Therefore, we preferred Montex 6500. Montex 6500, in its current form, ensured an increase of 30 % in our production with its width of 3.20 by saving energy up to 18 %.”