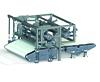
Medical and Hygiene Products
Evidentially, such a medical crisis has increased the need for medical and hygiene nonwoven products which resulted in new orders for machine systems for fibre preparation and web forming of hydroentangled products. In this sector, DiloGroup traditionally stands for large card working widths and high web speeds. In Asia, there is an increased demand for higher cross strength in this kind of product, which can be realized by using the classic random web carding technology or – even better – by combining these production lines with high-speed crosslappers.
In the general field of hydroentangling lines, DiloGroup has had no partnership with a hydroentangling equipment specialist. For this reason, we have not been able to deliver complete hydroentangling production lines as general contractor starting from fibre preparation to the end of line equipment such as cutting, winding and packaging.
Cooperation with SICAM s.r.l., Italy
However, since mid-2020, there has been a close cooperation with SICAM which enables us to engineer and deliver complete production lines including all components of hydroentangling, drying and end-of-line systems. This cooperation makes DiloGroup a general contractor for hydroentangling lines for the production of lightweight nonwovens from fine fibres with high production capacity. A first project has already been contracted. This marks the beginning of our increased activity in the lightweight and hygiene sector complementing the classical needling and will help to improve our worldwide position in this special field of application.
Sustainable Nonwovens
In addition, the demand for sustainable nonwoven products is increasing. Political demands for sustainability and for reducing the energy and water consumption in the production phase are well defined. Nonwovens used as disposables should be biologically degradable. This is where we return to the beginning and where DiloGroup with results achieved in the specialization of processing natural and viscose fibres can now gain further experience based on the development work with “MicroPunch”-technology. The cooperation with partners in the development work has led to successes that also impact the improved lifetime of the needle modules in the intense needling technology. In the meantime, the improved economy of our intense needling process has been confirmed.