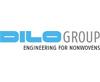
Manufacturing technologies for the nonwoven sector, Dilo Group heads towards the energy and raw material saving opportunities for the entire textile production chain in the light of the increases in the energy and raw material costs. Having recently focused on developing new machines which lead to positive outcomes in all stable fibre processes and increase process efficiency and web quality and homogeneity, Dilo Group reduces fibre consumption with its products. It has also focused on Dilo isomation process aiming at creating evener web.
Since the processes used by Dilo in web creating and connecting are mechanics-weighed, Dilo ensures significant savings in the production costs. Standing out with the high production speed and efficiency that it provides to its clients, Dilo achieved a great success with the Isomation process offering the opportunity of more evenness in the nonwoven fabrics.
Homogeneous Production
The dosage unit (DON) which feeds the fibre to the card feeder in a continuous and homogeneous manner, the card feeding unit (MultiFeed) designed by Dilo Spinnbau which can operate up to 5 meters of width in another step to improve evenness and Twinflow card feeding system ensuring an operating capacity above 400 kg/hour in the production with 1.7 dtex fibre in the Isomation process are used. Thus, Twinflow which offers the high tech feeding solution for the flat production card lines ensures a more homogeneous doubling effect.
Spinnbau Multicard developed by Dilo offers high production suitability thanks to easy and fast access for maintenance and cleaning in addition to a potential speed up to 200 m/min. and thus, provides economical solutions for nonwoven fabric production in all card operation width and fibre fineness values.
Fibre Saving
Entry speeds up to 200 m/min and 160 m/min can be reached in the HL series and DL series, respectively, in cross lappers. Since DL series are also equipped with Dilo Machines Webguide ensuring high homogeneity in high speeds at the same time, it ensures a considerable fibre saving. Vertical and horizontal cross lappers with laying sensitivity up to laying width of 16 meters ensure that high quality is obtained in the production.
In the isomation process, the machines having the feature of single-side needling and both-side needling can needle and manufacture nonwoven fabrics for various product usage areas with different needling machines with nonwoven fabric production and patter features. Thanks to elliptical and circular movements, shrinkages in the needling area can be controlled in the system and high-speed nonwoven fabric production is ensured in the small width range.
Use of Less Energy
Machines manufactured by Dilo for the use of natural and biologically recyclable fibres stand out with the recycling of textile products and fibres as well as the use of fibres made out of bio-plastic materials and therefore, the use of less energy. Since the machines used in the web creating and connecting processes are mainly mechanical, the use of less energy is in question when compared to the non-mechanical processes.