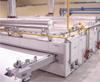
Brückner, which has a history of 60 years of success in the textile industry, is one of the leading German machinery manufacturers. The company that was only a small technical office in 1949, achieved a rapid growth in the field of textile machinery engineering and now it is a family business managed by the second generation in Leonberg, Germany. Brückner, which has offered many innovations to the sector, has obtainedd various patents. Brückner manufactures drying, fixing, sanforizing, continuous dyeing, coationg, heat setting lines for the finishing processes. The company that makes difference with its finishing solutions developed especially for the technical textiles, made varioud innovations with Power-Frame Eco Stenter.
In order to support the textile manufacturers to cope with the high costs and the intense competition, Brückner prepared a generation of strong dryers and energy efficieny. Brückner states that the concept of efficiency, which is applied by the company in the strict sense, is frequently used among the machinery manufacturers. The company has developed a brand new dryer for the finishing processes of woven and knitted fabrics. This new dryer, called INTROFIX, was presented in ITMA Barcelona in September 2011 for the first time. INTROFIX has been presented on a virtual stenter POWER-FRAME ECO by means of an interactive three dimensional presentation. The prototype of the product is running at a German customer.
The heart of the new dryer is described as a special heating system running with an intelligent control system and an integrated heat recovery system. With this combination, the gas quantity required for the stenter reduces considerably. According to the experience gained with the INTROFIX prototype, the production output could be increased while installation and maintenance advantages were obtained.
55 Percent Savings as a Result of the Innovations
It is stated that compared with the other stenters, the new Power-Frame Eco allows to save 5 percent of energy. In addition, with the heat recovery system, 30 percent of energy is saved. In other words, it is possible to save 55 percent of energy depending on the type of the process and on the type of the product. There is also another innovation that provides savings; Up to now, the air needed to be exhausted from the stenters however this is no longer necessary in Power-Frame Eco. As a result, the customers save both time and money for the erection of the plant. Besides, energy losses also decline as no piping is situated outside of the dryer.
The heat recovery system is offered to the customers as integrated in the dryer. This structure on operator level, can be cleaned easily. The newly developed heat exchange unit is smaller and lighter compared to the previous version. It also allows a faster maintenance. This technology used on the woven fabrics, is also suited for the delicate knitted fabrics.
The New Generation of Dryers for Nonwovens
Brückner managed to attract attention with its new generation dryer developed for the spunlace nonwovens. This drum-type dryer was launched by the company for the first time in 2010. The machine ensures a unique temperature accuracy on the fabric and a high energy efficiency. Since the zone temperatures and the air circulation intensity can be varied every 1,5 m, the drying can be made very gently and in low temperatures.
Besides, Brückner’s Supra-Flow BX dryer has been developed for the finishing of the nonwovens with weight of up to 6000 g/m2 and a thickness of 300 mm. The homogeneous air and temperature distribution across the complete fabric length and width ensure a high-quality end product. Since the optimum air control system of the machine requires less electrical energy, it provides cost savings. This pilot system will be available as soon as possible.
The solutions Brückner provides for the high-loft nonwovens, which are included in the technical textiles, are the other innovation of the company. A new application unit for the direct coating of bi-elastic knitted fabrics is one of these innovations. This new unit called Techno-Line, is integrated in the stenter entry. New developments allow a simultaneous coating of the upper and lower side of the textile web in one dryer passage.