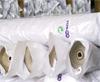
Yünsa, which is the Europe’s greatest manufacturer of worsted fabric and one of the leading companies within the global worsted fabric sector, attracts attention with its production process, total efficient management activities, R&D studies and the success it achieved. At its production facility in Çerkezköy, we, as Textil Dünyası, visited the company, which sits at the summit of the worsted fabric market of Turkey and Europe. We received information from Muhammet Eken, Production Director at Yünsa and from Sema Kırkoyun, Specialist of Quality Systems, about the company’s production, quality management and its objectives.
Muhammet Eken, Production Director at Yünsa, answered our questions about the production process beginning with supplying wool and yarn production. Eken remarked that they supply wool from Australia (Merinos) after the washing process is completed and he added that with their yarn preparing line, they manufacture 12 tons of yarn per day. Eken stated that they meet 90 percent of their yarn need through their own production and the remaining10 percent through the imports. Eken underlined that Yünsa has 4 preparation line and continued by saying; “We’ve established our lines mostly of the high-tech combing machines and drawing frames of NSC. Since yarn gains its quality after the preparation process, we keep our machines technologically up to date as much as possible.”
Eken remarked that with 4 preparation machines separated according to colors, they avoid the quality problems in production. Eken added that Yünsa has also separated the division of the mill where ring machines are located according to the colors. Eken stated that due to the excess number of machines, they separated the strayhgam and kamgam facilities. “By this was the we removed the crowd within the facilities and consequently their productivity rate increased. At strayhgam facility we produce between 500 kg and 1 ton of yarn a day between Nm 10/1 and 16/1 scale,” said Eken.
We Gained a Different Vision at ITMA
Eken underlined that in 1999 the company gained a different vision. “At ITMA, we met a compact machine that offers solutions to prevent yarn breakages. In addition to our existing Zinser machines, we purchased 5 Suessen compact machines and became Turkey’s first compant to produce yarn in compact machines. Over years, we integrated all of our machines to this compact system. Now all of our machines have been applied Suessen compact modernizations. The capacity of our spinning mill has reached 32 thousand spindles and our production capacity has increased to about 12 tons per day,” said Eken.
Eken also mentioned their winding department and stated that they mainly use Oerlikon Schlafhorst machines. Eken added that USTER® QUANTUM 2 and 3 model control and test devices are located on machines being used. “We can follow the whole production process online. On the other hand with our Xorella fixing machine we can perform the winding production process without any problem,” said Eken.
We Achieved Flexibility with the Diversity of Our Weaving Machines
Eken stated that they use Benninger warp machines in the weaving department and added; “We use Benninger warp machines and Uster automatic drawing-in machine and TMT sizing machines in the weaving preparation system. “ Eken continued by saying; “Yünsa also has Picanol and Dornier rapier machines. With the additional weaving investments we made the previous and this year, our worsted fabric production capacity has reached 50,000 meters per day and we became Turkey’s and Europe’s greatest woollen facility that performs production within its own body.”
Eken also mentioned their weaving looms. “In addition to the rapier looms, we also have air jet looms. We’ve been the first company to use air jet loom in worsted fabric prodcution since 1992. As we’re engaged mostly in wide-width weaving, we buy machines suitable to lycra. In the following years, we preferred Picanol looms in order to ensure flexibility,” said Eken and added; “With our various looms we’ve got the chance to evaluate each customer’s distinguishing characteristics according to the qualities we’ve developed.”
Eken emphasized that the company, which is able to perform dyeing processes also on fibers, yarn and fabrics separately, has not difficulty in ensuring color continuity. Eken remarked that their yarn dyeing capacity is about 5 tons per day and fabric dyeing capacity is around 15 thousand meters. Eken stated that they aim to increase this figure to 20.000 meters in 2012. Eken underlined that in dyeing, there are multiple choices available such as fiber dyeing, yarn or fabric dyeing.
In Addition to the Domestic Brands
Kranz ve Thies Stand Out in Dyehouses
Muhammet Eken also mentioned the machines used in the dyehouses and stated that in addition to Kranz and Thies, Dilmenler, which is a domestic brand, are the machine brands they mainly use in the dyehouses. Eken added that in the yarn dyeing department they mainly use Kranz, Dilmenler and Thies machines. “We use mainly MCS in fabric dyeing department. We currently have 15,000 meters of fabric dyeing capacity, 5 tons of cone dyeing and 5 tons of tops dyeing capacity,” said Eken and added; “In our finishing line we use Zonko washing machines featuring wool felting which is called rope washing and milling.” Eken also stated that they use multi-deck stenters of Brückner.
After these processes, fabric goes to the dry finishing unit, in which it gains its functional features. Eken siad that after the dry finishing process, in which the fabric gains its antibacterial characteristics and brightness, the fabric is scoured in the Birlla and TMT KD machines and is provided with dimensional stability. “At this point the strength of the apparel increases, its form is not distorted and wool life is gained,” said Eken and added that in the final step the fabric is taken into several tests according to the demands of the customers and it becomes deliverable.
We Focus on Exports in Production
Sema Kırkoyun, Specialist of Quality Systems, stated that they focus on exports in the marketing process. “70 percent of the production is carried out for the exports and the remanining 30 percent is for the domestic market,” said Kırkoyun and added that Germany, England and America are their main export markets. “We perform exports to more than 60 countries. We perform 62 percent of the exports (75 percent in total) to Europe. On the other hand Japan, China, Brazil, Argentina and Uruguay are our new markets. We have our own sales offices in America, Germany and China and we have 5 Chinese employees in China. We have more than 20 representative offices in various countries,” said Kırkoyun.
“China has already been producing cheaper goods, therefore we’re conducting studies on luxury consumption, which tends to increase and which the country is in need of. We’re following this strategy, which had been practicing by the Italians by building up factories, without establishing any mills. We continue to sell our fabrics, included in our product segment called A Plus, to China,” said Kırkoyun about their activities in China.
Kırkoyun underlined that Yünsa operates as a subsidiary of Sabancı Holding and it performs production in viscose wool blends, polyester blends, cotton blends, and linen segments. “We supply the fiber used in these products generally from the domestic market,” said Kırkoyun.
We will Increase the Efficiency of Our Plants in 2012
Sema Kırkoyun stated that 2012 they will continue to focus on efficiency in every fields such as ra materials, labor force, machinery and energy. Kırkoyun underlined that they began the Total Productive Management (TPM) activities in February 2012. Kırkoyun said that the products, of which carbon footprints are not calculated will no longer be able to pass the European customs. Kırkoyun also reminded that with the law that will be enacted in 2012, the amount of carbon emission will be followed by the governments.
“The European customers have been more careful about the ecological and organic products. The brands such as Marks & Spencer or Hugo Boss, want us to report the chemical ( such as natural gas and electricity ) amount we consume in order to be able to calculate their own carbon footprints. The final consumers in Europe tend to use the least damaging products for the environment. In Germany, a project has been started by Systain consulting company in order to determine CO2 Performance, energy costs and the amount of potential energy savings. Hugo Boss has also been included in this project. The first pilot implementation of the project has been made in Germany. The second one will be made in Turkey and Hugo Boss has suggested to include Yünsa in this project. They will pay a visit to our mill and machiery park and will conduct studies in order to develop projects on declining the carbon emission amount and energy savings potential studies,” said Kırkoyun.
R&D Activities Continue at Full Speed
Yünsa’s R&D center has been providing service since October 25, 2010. At the center, which has a staff of 60 people, studies are carried out in order to develop innovative products, to expand the company’s patent portfolio, to predict, evaluate and to ensure the implementation of the advanced technologies that may affect the balance in the sector. The company’s strategies are also determined at this center, where market researches are made. The center, which has been through a rapid growth since 2011, conducts significant studies. Yünsa R&D center organizes seminars in contact with 12 Turkish universities and conducts studies together with 7 international universities and R&D centers.
Yünsa 2011 in Figures
Total Fabric Sales; 12 million meters with an increase of 10 percent
Turnover; 214 milyon YTR with an increase of 36 percent
Operating Profit; 21,9 milyon YTR with an increase of 112 percent
Net Profit; 14,2 million YTR with an increase of 173 percent