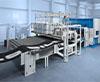
The machine manufacturer DiloGroup provides production lines for any nonwoven process and all types of staple fibre products. In its long-standing history, with DiloSpinnbau, DiloTemafa, DiloMachines and DiloSystems, DiloGroup delivers the complete range of machinery needed to produce needled nonwovens, and together with partners, thermobonded and hydroentangled nonwovens. We interviewed with the CEO’s of Dilo Group Mr. Johann Philipp Dilo in March issue of our magazine about the topics regarding company operations, specific technologies and customer solutions.
Q. Would you give some information on the innovative technologies produced by Dilo Group for the non-woven industry?
A. Mr. Johann Philipp Dilo, CEO- Apart from a constant development process for the standard range of machinery with regard to capacity, product quality, reliality and efficiency, development of new technology is in focus for the next two years. Additive manufacturing will play a particular role for lightweight automotive moulded parts to be shaped on the basis of a 3D fibre distribution in the material plain with varying mass and thickness. The 3D-Lofter applies an aerodynamic webforming process segmented across the width in increments of ca. 30 mm.
In addition, IoT solutions on the basis of Siemens software and technology are in demand for better production line efficiency, control of parameters, quality and ease of operation. Sensors help to monitor safety and quality of machine elements as well as the textile product. Not only preventive maintenance but predictive maintenance is the issue.
Q. Would you briefly mention about the product range of Dilo Group?
A. Mr. Johann Philipp Dilo, CEO- DiloGroup offers complete lines for the production of nonwovens as the specialist and leader for needling lines, but also for other consolidation technologies like thermobonding, thermofusion, water entanglement and chemical bonding which DiloGroup offers together with the relevant range of partners. A typical needling line we offer includes bale opening, blending, card feeding, carding, crosslapping and various types of needling for any fibre and product.
Q. Would you share your own assessment about the current position of non-woven technologies with the progress it has made? Would you exemplify medical and especially hygiene industry in this context to clarify the topic in more detail?
A. Mr. Johann Philipp Dilo, CEO- With regard to the relative importance of various webforming and consolidation technologies for the nonwoven industry, it is clear that needling has been for many decades the most versatile for any staple fibre product and has held the leading position. In recent years, however, a higher growth rate is associated with water entanglement technology which has further increased during the current pandemic situation with high consumption of medical and hygiene material. Dilo is offering together with our partner SICAM complete lines for this water entanglement sector as general contractor.
Q. Adding to the compact manufacturing lines offered to the market, would you give us some information about the specific solutions and technologies integrated into your manufacturing lines?
A. Mr. Johann Philipp Dilo, CEO- Most needling lines to process staple fibre apply card/crosslapper solutions for webforming. DiloGroup engineers design solutions adapted to the customer profiles of need and requirements with regard to production rate and quality. The complete array of equipment from bale opening and blending, including airsystems engineering for dust filtration, carding and crosslapping machines hold a prime position with regard to speed and web uniformity. Likewise the needlelooms of any needling mode, size and speed create a superior surface quality by newly developed needle distribution schemes developed by our special software with the aim to avoid visible stitching patterns. All machines in the line have been designed for the long term with a high degree of reliability, low energy consumption and ease of maintenance. Special devices help cleaning of the machines from fibre preparation to webforming and needling and keep maintenance low with the operation computer aided to assist line operators.
Q. Where do you see your cooperation both in Turkish and in Global markets while taking into consideration machinery produced?
A. Mr. Johann Philipp Dilo, CEO- Dilo machines are made in Germany. Their development and production requires many well-trained associates with long experience to provide the necessary service, spare parts supplies, monitoring of electronics and performance by tele-diagnostics and supervision by our team of service technicians. Turkey is a large and important country for the production of textiles which has increased its share considerably during the last years. Turkey is among those countries who have a special feeling and knowledge for nonwovens and their production. It is therefore foreseeable that in the long run good growth rates can be expected for the Turkish nonwoven industry.