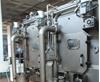
Tachycon was established with an innovative production concept and maintains its product designs and production activities with a productivity-oriented understanding within the scope of the textile industry's needs. Tachyon creates original and innovative designs and realizes them for the textile machineries. Zafer Serttaş being one of the partners of Tachyon, which gets the patents for all the machineries it manufactures and creates difference both in Turkey and the whole world, answered the questions of our Editorial Board.
Zafer Serttaş informed that they determine the needs of the textile industry and then they conduct their studies in terms of the products required and underlined that their aim is to become a trademark known all over the world. Serttaş noted the companies present in the market maintain their production without any innovation for many years and informed that as Tachyon they will design machineries with an innovative perspective and change the known machinery production values. Serttaş said that they give the priority to continuous washing machines and aim to complete the whole product range with a productive rope washing concept required by continuous washing machines.
Serttaş informed that they to become to one being imitated not the one imitating added that they aim to manufacture original innovations by questioning the present perspective and templates in the textile industry. Serttaş noted that they use this innovative perspective in all products they manufacture and informed it is essential to manufacture innovative, productive and economical technologies. Serttaş; "We are trying to do the best we can in order to proceed with secure steps," said.
Tachyon Realizes Environmentally Friendly Production
Serttaş pointed out that as Tachyon they adopted an environmentally-friendly production concept and informed that they give great importance to sustainability for the machineries they manufacture. He also underlined that they try hard to create designs that can meet the expectations of the machine operator to the company owner.
“The most important point that is focused on our products is to keep ecological side effects at minimum," said Serttaş and noted that the rope washing machines provided to the market by their company is the most productive machine at present in the world and added that they provide savings by 60% compared to their competitors.
“We Focused on the Design of Machines Consuming Energy Efficiently”
Serttaş informed that they develop several products and projects in order to provide energy savings and recycle energy which is one of the biggest costs in the textile industry. Serttaş, “Despite recycling products used in all industries and enterprises, a great deal of losses cannot be prevented. Thus, we decided to focus on the design of machines consuming energy efficiently,” said.
Serttaş underlined that they design better machineries than their European competitors and informed that thanks to their machines they will provide crucial advantages to textile companies in the national and international markets. Serttaş noted that their projects dedicated for the textile machinery industry continues and informed that they will get the feedbacks of their studies in a short while.
“Our R&D Studies is supported by TUBITAK”
Serttaş informed that their studies is supported by TUBITAK thanks to the machines they manufactures with R&D studies and added that they were granted with subsidies for their research and development activities. Serttaş informed that their products are accredited by European Union Environment Funds and added that their machines can be purchased with an option of 2 years’ time without payment and 7 year-term.
Pluvia Rope Washing Machine
Pluvia Rope Washing Machine providing water and energy savings up to 60% compared to all machineries in the industry, including its European competitors provides the required pressure, and speed required for the washing process and the patent belongs to Tachyon. Thanks to this technology the machine provides important productivity return and the nozzle inlet is manufactured from special design plastics in order to enable water flow. Pluvia Rope Washing Machine specially designed in order to increase the washing effect is enriched thanks to the pressurized air channels installed within the water column and the water and air. Thanks to this, the penetration of the water inside the fabric is increased and consequently maximum washing effect is obtained. Thanks to the movable J-Box feature of Pluvia Rope Washing Machine, the fabric amount in each chamber can be adjusted precisely and one by one.
Thanks to the adjustable level elements within chamber, the water amount to be transferred to other chambers can be adjusted as required at Pluvia Rope Washing Machine and the difference of levels in the inlet and outlet level of conventional machines thanks to the overflow. Thanks to the squeezing cylinder of Pluvia Rope Washing Machine, the required squeezing forces needed to squeeze the fabric in rope format was calculated and designed. The cylinder coating material and harshness is specially designed for the fabric in rope format and squeezing cylinder system is available at every chamber so, the chamber water and chemicals which were relatively dirtier are not mixed and this is eliminated mostly. Thanks to its modular, flexible and ergonomic structure, Pluvia can determine the number of chamber needed for the process
CyTherm Hot Cylinder System
CyTherm enables an increase by 20 to 30% in the machinery capacity by reducing the fabric humidity after padding in stenter process. CyTherm enabling savings in stenter investments eliminated the padding squeezing cylinder problems. Thanks to CyTherm the natural gas consumption is reduced by 20-30%. The steam used instead is generated in coal chambers and consequently the total energy cost is reduced.
At CyTherm application, the front side of the fabric does not contact with the cylinder so the fabric does not shine. CyTherm provides fast heating and cooling and a loading cell is used for synchronization. CyTerm is manufactures from stainless steel material and thus is protected from the corrosive effect of the steam. CyTherm designed so as to cover a minimum volume can used at 90% of the cylinder surfaces.
FlubbEr Ram Chimney Filtering System
Thanks to FlubbEr Ram Chimney Filtering System that cleans stenter fixed gases with wet or dry filtering systems (ESP) poisonous gases can be eliminated up to 98%. Thanks to the integrated economizer system, the natural gas consumptions can be reduced by 20-30 %. FlubbEr can be de-activated if required as it is connected to the main chimney with an automatic valve.
eCOLess Color Elimination System
eCoLess being the non-chemical and biological waste water color elimination system is coming to the forefront with its environmental-friendly, user and enterprise-friendly features. eCoLess generated from metal electrodes used as cathode and anode has a crucial place in the market with its low-cost in investment and enterprises. eCOLess that operated with the principle to enable color elimination by converting all organic compound within the waste water to CO2 and H2O by pumping industrial wastes to the color elimination system and giving electrical current to the system. At the same time, reduce in all parameters influenced by organic wastes can be seen. At eCoLESS no residues or mud is generated and many factors such as Ammonium azote, KOI, BOI, color, odor and pathologic bacteria count can be reduced.
RamEko Air and Water Economizers
As classic stenter machines have an atmospheric system, a fresh amount of air penetrates to the chamber while the waste gas is extracted from the chimney. Consequently the cold air having penetrated inside the machine prevents the fabric being heated inside the first chamber. There is no cold air penetration at RamEko Air Economizer so the fabric is heated as per the normal process
RamEko Air Economizer provides energy saving increases up to 20% at cotton process, up to 25-30% at blending, up to 40-50 % at polyester and up to 60-70% at tulle. As the process speed increases with economizer in stenter machines, the energy consumed per product/kg is reduced. The savings rate obtained with economized is by 35-40%.
The water economizer is used for heating the clean water with the waste heat in the chimney. With a water economizer 175 m3 of water can be heated up to 70 degrees per day. It can be adapted to the stenter with a full automation.
The water and air economizers can be activated without any operational intervention and adjustment and all instant values can be followed from the operator panel and the savings rate can be monitored both instantly and cumulatively.