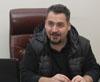
Having an important place among the Turkish nonwoven manufacturers, Salteks continues being one of the leading firms of the sector with its huge experience dating back to 1940s as well as its ever-increasing technologies. Their adventure started with the joint venture of 3 brothers in 1930s and continued when they purchased a wadding machine with the money borrowed from a non-muslim. Engaging in the business of cotton fluffer at the beginning, manufacturers expanded their operation to felt production. With the initiative of second generation executives in 1970s, the company continued operating with the name of Siteks and now, the company holds an important part of the Turkish nonwoven sector under its dominance. As of 1986, the firm has been operating under the name of Siteks and it also continues being one of the leading firms of the nonwoven sector with its company named Salvin.
Salteks is offering sub-industry service with a monthly capacity of 2500 tons in the fields of quilting, furniture, home textile, apparel, automotive, domestic appliances, insulation, construction, filtering, artificial leather, carpet, footwear, hygiene and medical products. Çatalca plants of Salteks cover a total area of 25.000 square meters with a closed area of 17.000 square meters. On the other hand, Çorlu plants of Salvin covers a total area of 50.000 square meters, 20.000 square meters of which are closed. Since 2006, Salteks also holds the title of authorised lap manufacturer of Dacron quilting and furniture products. The firm is the only Turkish enterprise to be authorised to produce laps in accordance with the quality characteristics specified by Dacron for its licencing firms manufacturing pillow, blanket, sleeping and sitting sets.
It Supplies to Many Sectors with its Product Diversity
The product range of the firm includes products for the quilting and furniture sectors, apparel, home textile and decoration, capitone, artificial leather, footwear, automotive, domestic appliances, construction insulation, filtering, medical and hygiene products. Nonwoven textile products of Salteks which are obtained through thermal and chemical binding methods and are given functionality via various finishing processes are used in various fields. They are used in the fields of filling materials, insulation, protective materials, decorative products, fire-proof barrier and capitone. The fabrics manufactured by Salteks in the field of hygiene are preferred as dry and wet handerchief, cleaning cloth, towel, wax pad, make-up removal cloth and pad as well as sanitary pads and personal care products
The firm which makes production in Çatalca with Salteks and in Çorlu with Salvin, has the mechanical needlepunch lines, thermal bonding lines, chemical bonding lines, quilting lines, capitone lines and finishing lines. Besides, the firm serves in the medical field by using many natural and synthetic fibers such as polyester, polypropylene, viscone, cotton and organic cotton. Having a wide product range, Salteks also manufactures construction and insulation materials through needlepunching from 30 g/square meters to 200 g/square meters and through mechanical needlepunching from 80 g/square meters to 1500 g/square meters and up to 6 m width. Our products include many functional features such as being uv-resistant, reinforced, water repellent, low shrinkage, heat and sound isolation, flame retardant, flame barrier, self extinguishing, breathable, etc.
2012 was a fruitful year
The firm which continues its constant growth in the fields of nonwovens and technical textiles and adds new products to its production segment stands out with its appearance as a family company. In the interivew we made with the third generation executive of the firm Salih Şişman in Çatalca plants, we both evaluated the year 2012 and were informed about the future plans of the firm. Emphasizing that 2012 was a fruitful year for the company, Şişman expressed their positive expectations for 2013. “We think that there will be really important developments in 2013 and 2014. Many foreign products were blocked. This development ensured with the additional taxes also affected us. We expect that this positive atmosphere will continue next year. Next year, we expect a turnover increase of 15 % with the new investments.” Said Şişman.
Stating that they worked in full capacity in 2012, Şişman also added that they export almost 30 % of their products. Emphasizing that they mainly operate in the internal market, Şişman stated that such products as felt which are small in volume were directed to exporting. Answering our questions about the export markets, Şişman continued by saying: “We export our quilting product to Balkan countries, in particular. While some technical products are exported to Germany, Dubai, Abu Dhabi, Russia stand out among the target export countries. We sell bead fiber products to Abu Dhabi.” Stating that they supply their raw materials from SASA at home and from China abroad, Şişman added that we are more careful following the fire in 2007.
A 2 % Share to R&D from the Turnover
Emphasizing that they follow the developing market areas through both R&D studies and fair participations, Şişman said that: “We take investment decisions on the basis of these studies. In this regard, we attribute an important share to R&D studies. We conduct the capacity increasing studies with 2 % share allocated from the turnover. Besides, we get informed about the technological advancements by following all editions of such fairs as Techtextile and INDEX in the global arena.”. Making an assessment about the year 2012 in terms of investment, Şişman stated that: “We prefer growing with our own equity capital as a result of a good market research without taking risk as there are no evidence showing how the global and local demands will change. Rather than an agressive growth with loans, we invest when needed by controling the capacity ratios. In this direction, our needlepunch investments continued in 2012. Besides, we modernize most of our machines. Lastly, we increased our production power with our recent mechanical needlepunch investment.”.
Reminding that they manufacture in Çatalca with Salteks and in Çorlu with Salving, Şişman expressed that they made a new cotton investment in Çorlu. Stating that they previously worked on polyester and viscone in this factory, Şişman added that this is a totally brand new investment. Machines will start operating when our mechanical deficiencies will be covered. With these new investments, new and additional adjustments can also be made. For instance, if necessary, we can make studies in the field of bleaching and integrate them to this investment.”. Except for these, Şişman said that a field close to the factory of Çatalca was about to be purchased and they would make an important investment at the end of that process.
Profit Margin Decreased Dramatically in Spunlace and Spunbond
Expressing that they purchased machine from Dilo for the first time, Şişman explained that this machine manufactured at the end of special studies will be peculiar to their factory. Stating that they will make investment of 500 thousand dollars for a product not existing in Turkey in 2013, Şişman said that they will appeal to the export field in particular. Emphasizing that they will make extra investments to diversify their product range, Şişman added that: “We make no more changes in the product range. We already appeal to a great many fields. However, our existing productions focus on the European region. For instance, we prefered air-driven system in the machines purchased to our new production field where we invested in cotton. German, Italian and French machines constitute the technologies of our new investment.”.
Touching upon the problems of the sector lastly, Şişman stressed on the fact that firms make incredibly agressive investments. Arguing that such investments will cause the firms go back, Şişman continued by saying: “In the past, firms would get the return of their investments. However, today, those which try to expand their operation fields in such sectors as spunlace and spunbond will lose in coming years. These businesses have come to an end. Now, profit margin decreased incredibly in these fields. Investments are made but those working with a capacity of 60 % make new machine investment. This meaningless growth also affects all fields of the sector.”.