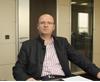
Waster Saving is of Great Importance for Us
Stating that the machine became really useful by enabling us to put the previously determined machinrt design and process criteria into practice in the dyehouse, Topgül added that performance booster of the machine has helped developing all the needed functions and trivial workmanship defects have been eliminated via dyehouse automation systems.
Stating that they ensure 50 % water saving with DMS11 HT Jumbo Dyeing Machine in comparison to its counterparts, Topgül added that: “We reduced the consumption amount from almost 60 liters to 29-30 liters. We can continue the production process with less water. The successful works conducted in this area are of great importance for us. Besides, we maximised the chemicals saving.”
Stenters are Key Elements of Enterprises
Continuing talking about the operations of other machines in the dyehouse, Topgül said that washing of enzyme-applied products through cutting machines is of great importance. Expressing that the cutting machines with padding mangle are now manufactured with the enzyme washing units, Topgül continued by saying: “This also increases the performance of stenter machines. Additionally, this machine has a key role in increasing the product quality and works with tension control for sensitive products. Serving for final processes following the dyeing, stenter machines are one of the key elements of the enterprises and they consume almost half of the total energy used in the enterprise.
Stating that they established natural gas counters, electric analyzers and data analysis systems in the stenters, dryers, and steaming machines and steam boilers using natural gas in the enterprise, Topgül added that: “We follow 67 parameters online though a database system designed for stenter machines. We choose any time interval and monitor the ratios of gas and electric use per kg/product and we can make detailed cost analyses on the basis of type. Besides, we can send the daily reports via e-mail. We ensure a significant amount of energy saving in the dryers and prevent excessive drying by keeping the moisture under control in the end product.”
Smart Machine Concept in Stenter Machines
Stating that they started to apply the smart machine concept in the stenter machines manufactured by Dilmenler Machinery, Topgül informed us that this system would reach the clients by the end of this year. Topgül added that: “The new concept is very useful. The existing machines do not contain database system. We are the first firm to establish such a system in the sector. Therefore, the information received from the machine do not disappear unnecessarily and recorded for efficiency. Feedback of these information which are recorded by time and reported is also of vital importance for the profitability of the enterprise. It also constitutes a significant cost item.”
Heat Recovery System Should be used for Efficiency
Emphasizing that they never experience difficulties in the heat recovery system in the stenter machines produced by Dilmenler, Topgül stated that the actual matter is to use the heat obtained with the preheated hot air in the process. Explaining that giving heat to the right place in a proper manner in the system is of great importance in terms of energy costs, Topgül continued by saying: “When we try to implement this system, as it is compulsory to keep the mass balance at zero, we encounter with a limit in the amount to be used in the machine. In other words, we have no problem in recovering the heat but we have to measure whether the system adds the hot air that we give to the machine into the process and minimises the gas passing through the natural gas counter. In our measurements, we saw that a saving ranging from 6 % to 26.5 % is possible with proper application. In terms of losses, there is a bit different situation. Losses range between 3-5 % per machine. Apart from this, there is a 10 % energy coming out with the hot product. It is not possible to prevent this. And, it corresponds to about 10 % of the total energy.
Emphasizing that heat recovery systems mean a lot for the drying processes, Topgül stated that as total energy amount used in the fixing process is lower than the drying process, the amount recovered in this process is also lower. In the measurements made in a 10-chamber stenter machine, it was observed that 75 % of total energy used in the fixing process with wet material was consumed at the initial 35 % part of the machine while 25 % of the total energy was consumed at the 65 % part of the machine. The preheated air obtained from the heat recovery is also the initial 35 % of the machine. It was observed that when the 65 % part of the machine was used, fixing cabins disrupted the heat stability and fixing process quality of the product was affected negatively.
Our Certified Products are Popular in the Sector
Stating that Dilmenler manufactured a machine meeting the expectations with the open width sanforizing machine, Topgül added that: “There is a principle that we follow in all machines and in all product groups strategically. Our principle includes determining the design criteria of the machines properly, getting approval for the projects of the machine by the assurance enterprises, making production in line with the approved projects and completing the certificates of the team making the production. We pay attention to manufacturing machines which cause fewer problems and are equipped with more durable equipments and devices. In this respect, we elevate the threshold to higher levels every year. We try to increase export to foreign countries and receive fewer maintenance demands for our machines abroad. We can compete with the prices in Europe but this issue is problematic with the Indian and Chinese products although our products are significantly higher quality.”
New projects are on the way
Reminding that they produce important projects in terms of swage block cold bleaching which is one of the most significant needs of dyehouses, Topgül stated that their latest project is Ünteks. Saying that Ünteks was initially designed as washing and bleaching machine of the reactive printed fabrics by Rudolf Duraner and DMS, Topgül reported that they obtained successful results. Explaining that open width continue bleaching and washing machine has been operating on reactive printed products with a capacity of 20 tons/day for nine months and has consumed about 8-22 litres per kg/product on the daily average, Topgül added that its counterparts consume about 25-60 litres per kg/product. Topgül said that this product is among the successful machines of the market and concluded his remarks by saying: “Washing performance reduced to 8-12 litres from around 35-50 litres depending on the reactive dyed product, dyestuff and colour group, steaming fixing quality and type of fabric and fibre. Reduction in the water consumption was followed by the production increase. Considering that 50-60 litres of consumption is regarded as an achievement in the sector, we have made an important progress in this regard.”
Important Brand of Turkish Textile: Dilmenler Machinery
Dilmenler Machinery which manufactures textile dyeing and finishing machines was established in 1982. Growing considerably in a short while, the firm bought its new building in Yenibosna in 1986 and continued manufacturing machines in this plant until 1993. In 1993, the firm started to use its new factory established on an area covering 5 thousand square meters in Vakıflar village, Çorlu. Developing its production volume and technological advancement every year, Dilmenler continues production activities at both İstanbul and Çorlu. An area of 5 thousand square meters was added to the existing plant in 1997 and an area of 7 thousand square meters was added in 2013. Now, the firm conducts the production of dyeing and finishing machines at two separate places. It has also increased its production capacity. In 2010, Dilmenler Machinery established its R&D unit and started to use its additional building covering 10 thousand square meters to this end. Having manufactured various finishing machines since 1999, the firm also manufacture many dyeing machines, dryers and stenters. Among the export markets of Dilmenler, there are India, Bangladesh, Pakistan, Syria, Egypt, Portugal, England, Israel, America, Peru, Chile and Equator.
Dyeing machines which Dilmenler Machinery manufacture include DMS 23 HT Beam Dyeing Machine, DMS 04 HT Yarn Dyeing Machine, DMS 11 HT Jumbo Short Process Fabric Dyeing Machine (RDS) and DMS 03 HT Synchron Air Jet Fabric Dyeing Machine and they provide alternatives for textile manufacturers seeking different solutions. Machines manufactured by Dilmenler Machinery for the Finishing segment include DMS 29 Fibre Squeezing Press, DMS 09 Fabric Reversing Machine, DMS 08 Fabric Preparation Machine, DMS 24 Open Width Fabric Washing Machine, DMS 22 Diltex Fabric Drying and Heat Setting Machine, DMS 05B Egalizing Air Relax Dryer, DMS 05A Jumbo Air Relax Dryer, DMS 18 Dilcompact Open Width Shrinking Machine, DMS 10 Open Width Padding Fabric Cutting, Squeezing and Slitting Machine and DMS 14 HT Rapid Drying Machine.