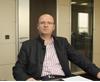
One of the leading manufacturers of Turkish textile machinery, Dilmenler Machinery continues shaping the sector with dyeing and finishing machines since 1982. Having a strategy of competing with global brands, Dilmenler Machinery conducts its activities at the European standards at Megan Dyehouse established for R&D studies. The firm also carries out trainings for clients, representatives and technicians in this plant. Making explanations about this facility to our magazine, the manager of the plant Yüksel Topgül gave important information about the details of the investment.
Pointing out to the fact that the first foundations of Megam Dyehouse were laid in 1996, Topgül stated that the investment was postponed for years due to the fear of negative feedbacks. Emphasizing that the actual aim of the dyehouse is to perform the R&D studies to support the production of Dilmenler Machinery, Topgül said that: “we blended our experience of 36 years and technological know-how in this plant and contributed to our production. Review of new ideas intended for supporting the activities of our firm will enable us and our customers to take more correct steps.”
Alive Machinery Presentations and Trainings Continue
Topgül explained that the plant was originally designed for the training of foreign clients, representatives and technicians and they did not have an intention to compete with the textile manufacturers and dyehouse owners in this concept. Topgül explained their motivation for establishing such a dyehouse as follows: “There is no other firm with private equity which manufactures an equal amount of dyeing and finishing technologies at full efficiency. Different firms in the sector use our machines. We had to visit all factories to show how our machines operate. We had a similar problem for the training of our employees. Now, we can demonstrate all of our machines in operation at full efficiency in this dyehouse. Performance, quality and other criteria of the machines that we sell to our customers can be observed in this plant. We allow our clients to control the history of the fabric thoroughly in the dyehouse which was completely established with the machines of Dilmenler Machinery. This plant can also be defined as a training facility. We train our clients, personnel and technicians in this plant.
Emphasizing that this dyehouse will contribute to the new product development process, Topgül explained that they monitor the machines that they produce and test the steps to be taken in order to develop products, eliminate the existing problems and increase efficiency in this plant. Topgül continued by saying: “With this dyehouse, we and our customers gained a more flexible structure. While the sector typically performs dyeing at 1:8float, we perform dyeing at 1:4 float in this plant with our machines. There is a continuous production here; it is possible to talk about a living dyehouse.”
The distance between the parties selling and purchasing the technology is important
As a result of the R&D studies, an increase was recorded at both production and quality. Topgül stated that the production capacity increased to 17-18 tons/day from 4-5 tons/day and added that: “Owing to Megan plant, our products now meet the needs of the sector optimally. Environment friendly, economic and high tech products provide advantages to the firms. Besides, a close relationship with the client during the production process and direct answers to any questions provide advantages to both sides.”
Making explanations about the investment segments of the enterprise, Topgül reported that they serve in the knitted fabric dyehouse concept where fabrics are dyed as rope at a speed of 20 tons/day. Topgül continued by saying: “Apart from daily 20 tons of knitted fabric dyehouse, we made the investments including 10 tons of printed knitted fabric production, 12- colour two rotation printing and drying machines. Besides, the production of printed and flat fabrics only amounts to 20 tons at a daily basis. We will also put CPB Dyeing machine into practice in the ensuing days.
Our Sales in The Turkish Market Continue
Stating that almost half of the technology produced is for the domestic market, Topgül said that: “Turkey is one of our most important sales points as we work there with 50 % on average. Furthermore, we actively operate in such countries as Bangladesh, India, White Russia, Russia, Uzbekistan and Turkmenistan. We meet the wet and dry round machine needs of knitting and weaving fabric dyehouses. We also serve the customers who will make investment in plants for yarn dyeing and yarn drying as well as fibre dyeing. We can list our machines which are the main need items of Woven Fabric Dyehouses as Aerodynamic DMS03 HT Synchron Dyeing Machines and DMS22 stenter machines.”
Making assessments about the production process of Megam Dyehouse, Topgül explained the production processes of all machines separately. Starting to speak by defining the production process of DMS11 HT Jumbo, Topgül stressed that they manufacture only 22 items of this technology. Touching upon the features of DMS11 HT Jumbo machine, Topgül continued as follows: “We take all kinds of processes including pre-treatment, dyeing and post-dyeing processes of knitted and woven fabrics manufactured out of any and all natural and synthetic fibres and blends under control. At the same time, we provide service with fast, economic and high quality products. DMS 11 HT JUMBO provides practical solutions for dyeing fabrics of various weights ranging from 70 gr/m to 2300 gr/m with different nozzle alternatives. The machine contains AISI 316L which is a high quality stainless steel material with a high resistance against rusting. We, besides, make attempts at reducing water consumption of machines. It a pleasure for us to make the trials of these machines in our dyehouse.”
Machine Should be Known Very Well For Improvement in R&D Studies
Stating that the machine should be well known to develop it in the R&D studies, Topgül reminded that they now have the possibility of designing such innovations in the new working environment. Reporting that the studies should be launched once the production power of the machine is understood, Topgül added that: “The improvement work to be done following this process should be well-planned. Otherwise, we cannot obtain any benefits from the innovations.”
Stating that they could not perform such studies until Megam Dyehouse was established, Topgül stated that: “Feedbacks that we receive from the markets to which our products are sold contribute greatly to our improvement. We can produce successful works in line with the demands of customers. Everybody has different expectations. As Dilmenler Machinery, our biggest expectation is to manufacture ans sell useful and economical products. We closely follow even the momentary operation manners of our products. In short, we conduct significant works not only in relation to the principal features but also the background features.”
We Share Our Production Data With the Clients
Emphasizing the importance of preferring their own machines in the complete investments in dyehouses, Topgül reported that they provide efficient data to their customers in this way. Stating that it is the indicator of power to receive successful results in different dyeing machines, Topgül added that: “We provide a proper data control in complete investments. These data provided for both momentary productions to annual production increase the profitability of the firm. Besides, relevant works continue in our plant. We make attempts at manufacturing the fastest, the most environment-friendly, the most cost effective and the most profitable machines.”
Saying that the R&D centre is open to everybody, Topgül stated that: “We have no secret in our relationships with our customers. Anything we perform in this dyehouse is open to everybody. The production process can be monitored step by step. In this manner, many people can be aware of the product and quality produced in this dyehouse. Many buyers can even make trials to select the most suitable product. Thus, we perform our successful works through partnerships and exchange of ideas. We welcome the personnel sent by the customers buying our products and inform them about the machines. Completing this training successfully, the personnel return to their countries for production.” Describing Megam Dyehouse as a public enterprise, Topgül emphasized once more that they manufacture machines jointly with the clients.