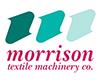
Denim still preserves its position in the fashion industry as one of the indispensable fabrics nowadays. The innovative uses of denim fabric effects the development of technologies from spinning to weaving.
Burteks Tekstil’s General Manager Mr.Recep Bektemir shared the developments in the denim industry with our editorial board and gave information about Morrison Textile Machinery and Ukil Machinery Co.Ltd’s denim technologies offered to worldwide brands.
As the denim industry grows, technologies dedicated to denim also changes. What kind of specific technologies do you provide to denim manufacturers with the brands you represent?
Denim has dramatically changed in our era in terms of fabric, so have changed the market demands. Now the designer determines the type of the denim fabric, not the manufacturer. If we look from this perspective, we can assume that it is essential to adapt the technologies in the denim industry to this process. The processes applied in the denim fabric production have really changed in terms of dyeing and finishing treatments and obtaining different fabric types with new applications. Some adjustments are made on machineries to implement these changes. For instance, different knitting shapes such as stretch and super stretch are used in denim fabrics. That is to say, there are many denim types, in which stretch is used in warp or weft or in both of them. Today, it is very difficult to find rigid, non-elastic fabric in jeans stores in Turkey. All these changes lead to several changes in machineries
Morrison Textile Machinery takes two aspects into consideration while adapting to these changes. The first one is to create the required structure to manufacture these types of fabrics and the second one is to upgrade the automation without dependence to individuals. In the past, other companies used to do the automation while Morrison provided machineries for the customers. However, for the last 10 years Morrison has started to do the automation of its machineries. In addition to required devices and control units used for automation, all the automation software is provided by Morrison, too. This software can also be connected to the general plant automation of our customers.
Morrison machineries are defined as “expensive” compared to its competitors. What is Morrison’s difference, what are the advantages provided to customers in denim industry?
The technology, sustainability and quality provided by Morrison are reflected in the price, thus it is regarded expensive. However, it should not be forgotten that these factors are quite important so as to not be ignored. The machine manufactured by Morrison in 1986 and the one manufactured in 2017 can operate side by side without any problem. Thanks to the additional modernization studies made, these machines can become sustainable. If a company can still the same machine in 1986 and 2018, this is a great success which means that the products can easily be adapted to changing market conditions.
Our customers Kipaş Denim, Bossa, Tüsa Denim and Çalık Denim decided to carry out their production by adding 2017-2018 version Morrison Rope Dyeing and Preparation Machine to its current machineries, thus they have repeated their liability and trust to Morrison and its technology. After so many years, the new version of the same machine will operate side by side. Morrison creates difference both in quality and technical specification with the production realized in America, South Carolina.
Can you give us information about the patented Peak Washer technology providing cost advantage and Morrison’s approach in sustainability?
Peak washer is a technology increasing water savings and rope opening performance. This technology provides 30-40 % water, waste water and energy savings. Even with a low quantity of water, it offers a better washing effect. As you know, sustainability is a very important issue in the world. Global ready wear companies prefer to work with companies using sustainable technologies. We even know that there are companies deciding on the water consumption in fabric production. In that point, Morrison provides crucial advantage with Peak Washer.
What is the difference between Indigo Rope Dyeing technique and Slasher?
Several yarns are turned into rope in rope dyeing machine and they are processed in whole. Whereas in Slasher machine, yarns are processed as warp tulle. Squeezing, immersion and ventilation/oxidation processes are applied to yarns in both systems. Squeezing is performed with a pressure of 10 tons in Morrison Rope Dyeing Machines while this is performed with a pressure of 3 or 5 toms in warp dyeing. As ropes (several) are in bundle in rope dyeing, there is no problem in squeezing but in Slasher, the geometry of the yarn will be corrupted if you squeeze with a heavier weight. In addition, as the rope bundle is a greater mass, the penetration of the dye is higher. This consequently enables deeper (darker) color possibilities.
Another difference is in terms of waste yarns created during dyeing; for instance, you received a short fabric order and you work on slasher. The yarn path of the machine is around 750 meters. After the type changes, the remaining last 750-meter yarn left on the machine is normally useless and 750 meters of dyed yarn is sent to waste. Thus, a higher rate of product loss is created in short order production. For example, on an order of 3 thousand meters you lose 25%. How can you profit with a loss of 25%? If you also consider the waste to be added during the weaving and finishing process, how much profitable can be a production conducted under these terms? This problem results due to the system of Slasher.
No waste is almost generated in rope dyeing process. There is a guide from polyester yarn in that machine. For example, the guide is attached to the end of the ropes as braiding in a production of 3 thousand meters. When the production reaches the end of the machine, the guide also reaches its position in the machine and then the machine gets ready for the next type. Due to all these advantages, worldwide and local denim fabric manufacturers prefer Morrison Rope Dyeing machines.
There are new local manufacturers having started to build slasher and sizing machines in denim industry. Has Morrison’s price strategy in Turkey changed the penetration of these brands to the market?
Morrison doesn’t determine its prices according to other manufacturers in the market. The primary criteria are sustainable quality and the follow-up of technological developments. Production and service quality are not sacrificed in price determination. Morrison offers special prices according to the machine specifications when selling a machine in Turkey. We provide the best that we can for each customer
How are the sales of Morrison in the Turkish market?
Morrison achieved a good sales level in 2017 in Turkey. Morrison’s philosophy in sales is realizing sales without any sacrifice from production quality, sustainability and service quality. In addition to rope winding, rope opening, finishing and sanforizing machines are in the portfolio. 2017 was quite successful for Morrison’s sales in the whole world.
Can you give information about Ukil Machinery Co. Ltd company whom you represent?
Ukil is one of the most important weaving preparation machinery manufacturer in Asia. At the same time, it is a company manufacturing Morrison’s rope opening machines. Besides, the company manufactures cotton and synthetic sizing machines, and warping machines like serial warp, conical warp.
What are the main features of Ukil that the Turkish market opts?
Ukil works hard to enter the market. The machines are quite good in terms of price and quality. The sizing machine has a special tank that can perform 3 dipping and 3 squeezing. Thus, it is pretty easy to have the sizing substance penetrated all over the fiber. Nowadays, there is one sizing machine in operation at İskur Denim and the second one was sent for delivery. Ukil gets stronger day by day in the market.
Have you defined a target for 2018 as Burteks Tekstil along with the companies you represent?
We will continue our studies for 2018 as well as conducting the after sales services for the sales realized in 2017. We have projects in operation in Turkey and Uzbekistan. In addition, we are also expecting the continuation of investments from Bossa, Çalık Denim, İskur Denim. I hope 2018 will be a productive year for our company.