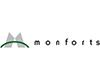
During our interview conducted with Mr. Ahmet Kılıç, the experienced Manager of Neotek Tekstil that has been executing as the Turkey and Turkmenistan representative of Monforts since 2016, he explained the underlying reasons on why Monforts; standing out as one of the leading machinery manufacturers in Germany, reinforcing its expertise in the fields of fabric dyeing, finishing and technical textiles with the importance they place on R & D activities, is being so highly preferred by the Turkish textile industrialists as well as the innovations that they are offering to the sector.
Welcoming our Pubishing Group Tekstil Dünyası at his office, Mr. Ahmet Kılıç, executing as the Manager of Neotek Tekstil, answered our questions on various topics ranging from the superior technology of Monforts, to the sales generated in Turkey.
Monforts machinery stands out among the foreign brands that receive a great deal of attention in the fields of dyeing and finishing, especially in the Turkish textile industry where investments in the recent years have been heavily made on the denim industry. Mr. Ahmet Kılıç indicating that the Monforts stenter and sanforizing machine were the most in-demand machinery of the denim industry also stated that as a Monforts privilege they were selling the sanforizing machine as a complete line to their customers in the denim business. In his assessments Mr. Kılıç quoted as follows; “The stenter and sanforizing machine are the primary machinery we are offering to the denim industry. We also supply the sanforizing machine as a complete line to the denim industry, which we sell individually under normal circumstances. Our customers can purchase the complete line from Monforts with the essentials that make up a sanforizing line, consisting of; a singeing machine in the front side, washing boxes in the back side, a weft straightener, a cylinder dryer and a sanforizing machine. Recently we sold such a line to the company DNM Tekstil for their plant in Egypt. The installation process is about to begin. Once again throughout the year we despatched 2 stenters and 1 sanforizing machine to the company Arta Tekstil. In addition to this, one stenter to Çalık Denim and one stenter as well as a sanforizing machine has been sold to Kipaş. Moreover, companies’ executing in businesses related to denim, such as Emin Tekstil, Hamle and Korat, whether it be their stenter lines or sanforizing lines, are completely operating with Monforts.”
“Monforts is the Only Machine That Delivers the Desired Outcome in Production”
Mr. Kılıç, pointing out that quality and providing centralized solutions constituted as the key elements regarding the customers’ interest for Monforts, continued his wordings quoted as follows; “When we observe the machines operating in major companies’, why do our customers prefer Monforts? Because unquestionably Monforts is the only machine that conveniently offers the features they are looking for and the only machine that provides the desired outcomes they want to obtain in their production processes...Alongside to this, due to the fact that denim fabrics are very heavy and unique fabrics, the most important element is the chain. Let’s tell anonymously, but we hear from many companies’ that when the machines of competitor firms are a just a little overdriven, they tend to go off the rails. Today, both cord fabric manufacturers and denim manufacturers across the world are mainly using Monforts.”
With its machines that bring quality to the forefront, Monforts, by also focusing on energy efficiency, contributes to the reduction of operating costs and to the sustainability of nature. Mr. Ahmet Kılıç stating that particularly the innovations devoted to energy savings and efficiency also constituted as another factor for preferring Monforts, explained the innovations taking place within this area, quoted as follows; “Monforts has significant practices on energy savings. As an example, Monforts machines have a 150 mm of insulation panels on its side walls. This is just like the sheathing of buildings. Owing to this insulation, heat loss is minimized. Furthermore, another significant feature of Monforts is that we are using the exact insulation panels used on the side walls on the grounding. All of this provides approximately 5 percent in energy savings. This is what differentiates Monforts. We are able to dispatch the ready insulation panel and conduct the installation immediately. These are measures to prevent heat loss; apart from this our machines incorporate a special program. This program, which we call automatic thermo-fixing, as you predetermine the desired temperature for the relevant fabric, the system then automatically adjusts the fan speed of each running chamber by lowering or increasing the speed range. In addition to this, it also determines the speed of the machine. The machine operates at optimum values and that’s how the heating circulation continues. Moreover, the moisture content of the exhaust air is measured so as to avoid the hot air that hasn’t reached to sufficient humidity levels to be removed.”
Energy Savings Up to 35 Percent with Eco Booster
One of the systems developed by Monforts for energy saving and heat recovery that has been introduced to the sector, is the Eco Booster unit, which operates fully automatic and features an automatic self-cleaning system together with an additional exhaust air cleaning module. Mr. Kılıç answering our questions regarding the heat recovery provided by the Eco Booster, quoted his wordings as follows; “The Eco Booster systems operates fully automatic. As an example, the heat recovered from the final 6-chamber stenter is connected with the fresh air in the 8-chamber stenter. Just imagine the energy that is needed to heat the air that has entered with a temperature of 20 degrees and on the other hand the energy required to heat the air that has reached to a temperature of 50-60 degrees. In the fixing process the Eco Booster saves energy of up 35 percent, where as in the drying process it enables energy savings up to 20 percent.”
Mr. Kılıç stating that the interior structure of the machines constituted as an important element with respect to the heat recovery process, continued his wordings quoted as follows; “The interior structure of all Monforts stenters contains a side-wall between the chambers. You can only see a space for the fabric to pass through and for the chain to operate. The advantage offered here by Monforts is this; you can conveniently adjust the heat-settings of the chambers at different temperatures.”
Mr. Kılıç also adding that the heat recovery process was provided via the concealed exhaust air ducts along the operating machine quoted his wordings as follows; “In stove-heated houses the heating stove would be setup in one certain room, and then for the other to be also heated the stove pipe would be extended throughout the house. The concealed exhaust air ducts resembles this. The exhaust air produced in the first chamber is circulated throughout the machine via this concealed roof construction system, and for example if this is a machine containing 10 chambers then it will discharged from the 8th chamber. In this way, the exhaust air contained within the chamber continues to heat the machine. Unlike other stenters exhaust air is not discharged from every chamber and there are no air ducts that resemble octopus arms on the roof construction.
Mr. Kılıç explaining that they were using the Monformatic program in order to measure the temperature during the thermo-fixing process so as to ensure that the exhaust air was discharged at the point it reached to the required moisture level, where no further drying was applicable anymore, also indicated that all Monforts machines were connected to the central Tele-Service via an internet connection when a mechanical malfunction occurred and owing to this the breakdown maintenance was conducted within the shortest time.
Lesser Chemicals, Lesser Water Consumption with Eco Applicator
Mr. Ahmet Kılıç, stating that via the Eco Applicator they were offering significant advantages in finishing processes, explained the advantages of the machine, quoting his wordings as follows; “The main principle of Monforts Eco Applicator, is to apply less moisture during chemical applications. As you know, when the fabric enters the stenter initially it is wetted in the padder. The fabric is then padded through the liquor for the second time. But no matter how hard it is squeezed; normal chemical finishing padders do not reach to a level below 70 percent. The Monforts Eco Applicator has a kind of kiss-roller, used for chemical applications and mainly as a replacement for the padder. The liquor is applied to the substrate by a thin coating using steel rollers. But we do not wet the fabric 100 percent. We only apply the necessary amount of chemicals to the fabric. As a result the wet pick-up rate of the fabric can be adjusted between 20-80 percent. Moreover, we do not pollute the environment with waste water and utilize less water.”
Mr. Kılıç indicating that many firms in Turkey had started to use the Eco Applicator stated that this had provided companies’ with a significant amount of savings in water as well as chemicals.
“It’s Not Likely To See Anyone Doing Everything In Perfection”
Mr. Ahmet Kılıç emphasizing that Monforts was a brand specialized in the fields of dyeing and finishing technologies, indicated that they found the competition created with the Turkish companies’ entrance into the sector beneficial. Stating that only companies’ that had the ability to create awareness within the sector would be able to proceed, Mr. Kılıç quoted as follows; “We believe that competition benefits both the customer as well as the manufacturing companies’ that take part in the competition. Because via competition, not an aspect of low-performance, on the contrary a real sense of quality is created.”
Mr. Kılıç continued his wordings as follows; “Monforts is very successful in providing excellent customer service, high quality of the products that are being sold and in terms of customer satisfaction. Monforts also owing to its 130 years of experience within its field of expertise is very successful in its production. Although Monforts has often taken place as the highest priced company, our customers have always preferred us and have been very satisfied with the quality of our machines. The contribution in the production process of Monforts’ Monfongs plant located in China is also reflected in the prices. Monfongs can produce 400 machines per year. In Germany we produce around 60 - 70 machines. This contains stenters, sanforizing machines and the Thermex machine for continues dyeing.
Mr. Kılıç also referred to the fact on some companies producing a wide variety of machines. “Every company has certain types of machines that are successful. I am especially highlighting what I am about to say; It’s not likely to see anyone doing everything in perfection” states Mr. Ahmet Kılıç, and adds quoting his wordings as follows; “For example, I as Monforts cannot produce a cylinder dryer better than Wumag, everyone has its own expertise area. If a company is at the point where their objective is to make money through the production of a fabrics control machine, I really don’t have any clue regarding how successful they will be in producing a stenter machine.”
“We Surpassed Our Targets in 2017”
In his final wordings sharing his assessments on the sales generated in 2017 and their targets for 2018, Neotek Tekstil Manager Mr. Ahmet Kılıç stated as follows; “We surpassed our targets in 2017. I can say that we received more orders than expected. Other than the ones sold for weaving fabrics and for denim, to Çorlu and Çerkezköy we sold 5 stenter machines to be used in the knitting field. With respect to our expectations for 2018, is for it to be better than 2017.”
Mr. Kılıç adding that they were able to provide machines to their customers at more affordable prices via Monfongs production facility taking place in China also stated that for their Monforts customers who do not want to go without the machines produced in Germany, the same quality, sales and service continues to always be provided from Germany.