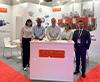
The following week, Fatih Savaşkan, the General Manager of Jenesis Steam Generators, who also participated in the "Boilers and Burners" exhibition held in St. Petersburg in which Gazprom also made a show of strength, stated that they were pleased with the interest shown and added the following:
‘’The Uzbekistan market is a developing one. As the experience and knowledge levels of the investors increase, the interest in our products also increases. Thanks to Uzbekistan’s influence on Tajikistan and Kyrgyzstan, we have also seen shifts in investments in those countries. With the dealership infrastructure we have established in Uzbekistan on the occasion of this exhibition, from now on, we are a representative of our country there as well. On the other hand, I think the Russian market is much larger than many of us envision. To fill the gap created by the exit of foreign companies from the Russian market, there is a tendency to purchase mostly from local suppliers and not be reliant on anyone. However, thanks to the conciliatory policies followed by Turkey, there are also companies that confidently want to procure products from us.
We have also established Jenesis Russia to create an environment of trust in Russia. In addition, we have started active sales and marketing activities. Thus, we planned to increase our export rate in production.
Two weeks after returning from the Russia exhibition, we also participated in the "Enerjisini Üreten Fabrikalar " exhibition held in Tuzla Viaport. In this exhibition, we were at the forefront with our studies on how to use your current energy most efficiently, especially among renewable energy investments. We also made a presentation on "Cascade Steam Production Systems and Electricity Production from Saturated Steam" in one of the panels, which attracted a lot of attention.
Reducing Steam Production Cost
As Jenesis, due to the significant increase in energy costs and since their expectations change according to their needs, we are going through a period in which we are changing the perspective of end users towards boiler rooms.
At this point, high-efficiency and safe steam generation systems have been developed with the custom “Turboblock” internal structure by combining the design of water-tube boilers used in powerplants operating at 50 barg and above or on ships, with the design of steam generators produced at relatively smaller capacities.
Thanks to the Jenesis HUB System, efficiency can reach up to 99% while the occupational safety expectations can be met thanks to the zero explosion risk.
Lower Initial Investment Cost and Flexible Installation
Thanks to its advantages, it has both lower initial investment and operating costs. For example, if we assume that your total steam requirement is 12 t/h, investment for 2 units of 12 t/h steam boilers should be made in case of backup operation, especially in factories operating on a 24-hour basis. However, sometimes a single boiler investment may be preferred while taking the risk of stopping the entire factory in case of boiler failure. In fact, if a capacity increase is planned in the future, it can be planned to invest in a 15-20 t/h boiler instead of a 12 t/h one, since the boiler is not a system that can be purchased repeatedly. In such cases, steam boilers whose capacities are much higher than the actual steam consumption operate at efficiencies that are very different from the catalog values.
Since the HUB System is of modular design, 3 x 4 t/h modules will meet the initial 12 t/h steam need, and it will be sufficient to invest in 4 modules with a total capacity of 16 t/h; one module is considered a backup. If there is a capacity increase in the future, the capacity can be increased as desired with additional 4 t/h modules. In the HUB System, there are modules with different capacities including 1, 2, 2.5, 3, 4, 5, and 6 t/h.
Highest Safety, Zero Explosion Risk
In HUB system steam boilers, the risk of explosion is zero thanks to their water-tube design. Due to the large amount of water stored in Scotch-type fire-tube boilers and the water control systems on it, the explosion risk, which occurs due to erroneous perceptions over time and harmful to both the factories and human lives, has been reduced to zero thanks to the water-tube Turboblock design. By using pipes that can withstand pressures up to 250 barg, even if tearing due to corrosion may occur in the pipes in a long time, no explosion will occur but only water leakage.
Thanks to this feature, the HUB System can be installed even in residential areas and it legally eliminates the mandatory construction of a separate boiler room building. As how the costs of boiler room construction in the first investment are avoided, thanks to the fact that boiler rooms can be installed within the factories, heat losses from long pipes in the plant are also eliminated.
Cold Start-Up in 5 Minutes
Thanks to large heat transfer surface areas, low radiation losses, low NOx burners in Class III combustion, special Turboblock interior design and, condensing or alternatively non-condensing flue gas economizers, 99% efficiency can be achieved.
Conventional Scotch-type fire-tube boilers, which have a risk of explosion, produce steam at the desired pressure in approximately 45-90 minutes at the first start-up in the morning, which we call cold start-up. However, it takes 3-5 minutes to produce steam at the desired pressure with the Jenesis HUB system. In this case, thanks to the Jenesis HUB system, you will not have to pay for the unnecessary fuel costs induced by operating the burner at full capacity for 45-90 minutes to reach the desired pressure. For example, in a factory that operates 12 hours a day and 300 days a year, it is possible to save 250,000 Euros by not burning extra fuel for heating a 10 t/h boiler at the first start-up every morning. However, the cost of a boiler room of 10 t/h will already be around 250,000 Euros.
After the first start-up, when we run a full-capacity Scotch-type fire-tube boiler at low capacities during the day, the efficiency value will drop significantly below the catalog value. However, the small modules that make up the Jenesis HUB system are completely deactivated when they are no longer needed, and as many modules as needed are kept active. In this way, continuous operation at the highest efficiency is guaranteed.
Constant Pressure and Dry Steam Even During Instantaneous Peak Demands
In the HUB system, a very fast response can be obtained at peak demands. Contrary to popular belief, Scotch-type boilers take longer to respond to peak demands. Although the volume in the steam drum of Scotch-type boilers varies according to its capacity and pressure, only 2-3 kg of steam is stored for every 1000 kg/h capacity. For example, 20-30 kg of steam stored in the dome of a 10 t/h steam boiler will be able to supply steam at peak demands for only 10 seconds.
Since the volume of water stored in Scotch-type boiler is high, when there is a peak demand, it takes a long time to heat all this amount of water and produce steam. However, since the amount of water stored is very low in water-tube designs with Turboblok internal structure, they can respond much faster to peak steam demands. In Scotch-type boilers, in case of pressure drop at peak demands, the set pressure can be reached again in 10-15 minutes while in the HUB system, the set pressure can be reached again in a short time like 1-2 minutes.
Thanks to the automation in the HUB system and the simultaneous and continuous control of both temperature and pressure, high-quality and dry steam can be produced continuously. Steam turbines that are used in power plants and supplied by water-tube boilers must be supplied sry and high-quality steam. Otherwise, turbine blades rotating at high speeds will wear out in a short period of time and millions of dollars of damage will occur. By using the same technology, necessary equipment, knowledge and automation as a standard in our production, high-quality and dry, even some superheated steam can be produced when necessary.
Due to the absence of large water volume in water-tube boilers and the possibility of having more heat transfer surfaces with lower volumes because of the Turboblok internal design, they occupy less space. In addition, the boiler room is made smaller thanks to the modular system design in which modules can be placed next to each other, as well as the pumps and panels placed on the body.
Over the last 10 years, the Jenesis HUB system has already started to replace the classic Scotch-type boilers, which have been known for over 100 years and have become a habit. Thanks to this system, the view of the boiler room is changing in all steam-using sectors. It is possible to produce steam at much lower costs by using all the possibilities in boiler rooms with high savings potential.’’