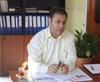
Supplying innovative technologies for the textile sector and mainly for the denim segment, Burteks Tekstil offers both its machine lines, spare parts and accessories and also after-sales solutions to its customers. Morrison Textile Machinery, UKIL Machinery, West Point Industries, Oerlikon Daytex Sanforizing Blankets are among the important brands represented by the company. While talking about their works, Recep Bekdemir, General Manager of Burteks, underlined that his experiences in this sector contributed him a lot.
Making evaluations on the sector, Bekdemir said that in 2011 the textile sector was dominated with modernization movements rather than the brand new investments. Bekdemir stated that revisions are made in yarn and weaving segment and Burteks experiences a modernization in terms of product range in the sector. “The textile manufacturers tried to modify and optimizde their machines. As Burteks we are planning long-term projects. Some of these projects have been completed in the denim sector and some of them will continue in 2012. I believe that 2012 will be a better year for us. When people see the future they make investments,” said Bekdemir.
Arguing that the textile sector will not come to an end in Turkey and Turkey will not turn away from the textile sector either, Bekdemir complained about the limited amount of share that is planned to be allocated for the textile sector regarding the export figures targeted for the year 2023. Related with the issue Bekdemir said; “However as a result of the pressure by the textile industrialists, the necessary regulations were done and on the grounds of the difficulties that have been faced with, additional taxes have been applied on the imported products. If you do not maintain the textile production, the current account deficit increases and you are faced with employment problems. As a result of the growth achieved in the textile sector, an incredible employment capacity is created. Performing production in all fields is the only way out for Turkey.”
We Represent 14 Brands
Stating that they represent 14 brands well known on the global scale, Bekdemir remarked that some of these brands includes machines and some of them includes accessories supporting the machinery. Bekdemir added that Burteks mainly focuses on denim preparation, dyeing and finishing technologies and weaving preparation and accessories. “Morrison, which we’ve been working with since 2003, is a locomotive company for us. Together with Morrison, we’ve got a really good position within the market. Despite any kinds of price pressure, Morrison has maintained its quality standars and is continuing production in South Carolina, America. Morrison, which included the Denim ( Ball Warper) Rope Winding and Rope Opening ( Rebeaming) machines in its production line after 2009, when West Point and L. Griffin stopped their productions, became the only company offering single source Indigo Rope Dye Dye technologies,” said Bekdemir.
Bekdemir reminded that the new generation Ball Warpers and Rebeaming machines can be found in Orta Anadolu Group in Turkey, in DNM Textile factories, which are the investment of Colin’s Group in Egypt , Envoy Textiles and Partex Denim Limited in Bangladesh, LNJ Denim in India, Chonband Company in South Korea and in Mou Fun in China.
Morrison Performs Production Without Sacrificing Its Principles
Bekdemir remarked that despite many European brands, which moved its productions in India and China due to the production costs, Morrison continued all its production in America and conducted cost-cutting studies in both environmental and sustainable solutions and finishing processes. “The matter of water and environmental is now more important than ever before in the sector in general. With the innovation made by Morrison, it will be possible to perform a waterless finishing process by using gas. The project, which has a high recovery rate in association with the gas usage, has been completed and the piloting applications began and we know that successful results have been taken, said Bekdemir.
Bekdemir emphasized that in addition to the machine quality, Morrison draws a successful graph also in the after-sales services. Bekdemir added that the brand deliveres the orders between 3 and 6 months depending on the type of the machine. Bekdemir underlined that the spare parts can be supplied in just one day by air and stated that the Morrison machines do not need too much spare parts. Bekdemir explained the reason for this by saying; “Morrison stands out with the quality of its machines. For example while the frame of the European machines is 2 cm, this figure is about 4 cm in our machines. On the other hand, the rollers of the European machines are coated with chromium-nickel whereas our machines are made of stainless steel. Due to the technical superiority our machines seem to be expensive than the European brands but considering the maintenance and spare parts requirements they are more economic in the long term.”
SanforTrol System Automatically Calculates the Shrinkability
Bekdemir argued that today the developments in the machines are done on the software and control systems rather than on the general principles. He gave the SanforTrol mechanism in the S8 sanforizing machines that provide the fabrics with unshrinkability feature as an example to this. “The general principle of all sanforizing machines that give shrinkability feature to the woven products, is the same with the technique used in Mr. Snaford Cluett’s first machine with rubber blanket. All the following developments were done on the softwares and control systems. The mechanism called SanforTrol reads and regulates the machines’ shrinkage figures itself automatically. It eliminates human intervention and leads the whole process. This process is normally completed by the automatic controlls, same with the ruler controls, made in every 3-4 meters. The ruler control made manually is applied in every 1000-15000 meters at best and controls shrinkability values. SanforTrol applies this test in every 3-4 meters repeatedly and records the results in the system in figures and graphs. It also controls the values set in the machine (speed and pressure) in order to eliminate the variations. Besides it always keeps the temperature and the moisture in fabric at the desired level,” said Bekdemir.
The Korean UKIL Expands Its Target
Recep Bekdemir stated that the other brand represented by Burteks is the Korean based company, UKIL. Bekdemir said that the company stands out in the sector with cotton sizing machines, synthetic sizing machines, serial warping machines and conical (Sectional) warping machines Bekdemir remarked that after it was established in 1977, UKIL achieve d a growth in the market. He added that they will quickly develop their new relationship with UKIL and will strongly launch the brand at ITM İstanbul in April.
Stating that in addition to the machine brands, they also represent strong brands of spare parts and accessories, Bekdemir gave Oerlikon Daytex Sanforizing Blanket as an example. Bekdemir stated that thanks to its sanforizing blankets made of natural rubber, Oerlikon Daytex is the market leader. “Oerlikon is a very big company and its Daytex Sanforizing Blanket production is performed in America. Sanforizing process, which is very important, is the latest finishing level applied on the fabrics. The life of the blanket changes between 6 months and 2 years depending on the unshrinkability values demanded by the companies. Despite all the difficulties, last year we’ve achieved very good figures in sales and reached the market share the product deserves,” said Bekdemir.
Recep Bekdemir remarked that in addition to Morrison, UKIL and Oerlikon Daytex will be exhibited along with their innovative solutions at the booth of Burteks Mümessillik at ITM İstanbul.
Denim Fabric Consumption is at a Low Level in Turkey
About the sector, in which they supply technologies - primarily of Morrison - for denim production, Recep Bekdemir said that compared to the other developed countries, denim fabric consumption is very low in Turkey, where he stated that 1-1,5 meters of denim fabric per person is consumed each year. This figure, which is 8-9 times higher in the developed countries, equals approximately 100 million meters of denim fabric in Turkey. Despite the fact that denim fabric spread from rural areas to the big towns in the countries such as America or England, the direction of this spread was from the towns to the rural areas in Turkey.
Bekdemir stated that in the investments, the target of the denim sector is the export market rather than the domestic market. Bekdemir said that some of the manufacturers work only for foreign sales without providing products for the domestic market. Bekdemir emphasized that the issues of sustainability and low cost started to stand out in the denim sector. Bekdemir added that Turkey is as successful as Europe in denim finishing however that it will cause problems in the future if Turkey can not create brands in this field. Bekdemir underlined that the companies should give importance to the R&D projects and added that the companies that diversifies and perform high value added production will always succeed.
Burteks Grows with Experience
Bekdemir, who is a chemical engineer, stated that he served in the chemical sector for long years and then entered the textile sector with textile chemicals and dyestuffs and that later he met Vasıf Tuzlacı, after whom he turned to the field of textil machines. Bekdemir emphasized that he combined his own knowledge and what he learnt from Mr. Vasıf Tuzlacı and won his position within his working life. Bekdemir reminded that Burteks Tekstil has been active since 1995 and that he believes that it will be honored to serve the textile sectors for many years.