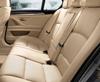
Manufacturers who continuously tend to using materials which are affordable and enhance the quality in the automotive industry seek for innovations on the basis of automotive textiles. Paying importance to the high quality, durability and lightness of the material, the manufacturers use automotive textiles in the carpets, furnishings, internal components, tires, safety belts, airbags and other parts.
20 kg Textile Product in Every Passenger Car
Technical textiles are manufactured primarily for technical performance and functional properties instead of decoration and good appearance. Having a wide product range, technical textiles are divided into many groups. Divided into groups according to their application fields, the technical textiles are widely used in the sectors of medicine, transportation means, construction, filtration, agriculture, sports, furniture, clothes and packaging. Considering the amounts of technical textiles used in the global arena, transport textiles rank second following the packaging textiles. While the consumption amount of technical textiles was reported to be 23.7 million tons in the world in 2010, it is remarkable that the consumption amount of transport textiles was 3.3 million tons in the same year. Automotive textiles are included in the transport textiles, in which there are many textile products manufactured with different raw materials and production methods. In the automotive textiles where nonwoven and knitted fabrics are used, quality and durability come into prominence. While automotive textiles can be used as seat filling fabric, filter fabric, canvas and tire cord fabric, about 20 kg automotive textile is used in a passenger car. Subjecting the technical textile materials used in the automotive sector to the tests related to the break resistance, resistance against abrasion, pilling, light fastness, perspiration fastness and rubbing fastness shows the emphasis put on the durability and quality perceptions.
Distribution percentages of the textile materials used in the automotive sector are as follows: floor mats and carpets (33,3 %), furnishings (18,0 %), internal components (14,0 %), tires (12,8 %), safety belts (8,8 %), airbags (3,7 %) and others (9,4 %).
Furnishings Rank Second
The carpets category has the biggest share in the sector and carpets are used to conceal open and solid parts in the automobile. In some fringed carpets, polyamide yarns are used to reflect the light and conceal the dirts. On the other hand, the furnishings which have the second place among the textile materials used in the automobiles with its share of 18 % vary structurally. These are plain woven fabrics (200-400 g/m2), plain woven velvet fabrics (360-450 g/m2), warp knitting fabrics (160-340 g/m2), raschel double needle bar knitted fabrics (280-370 g/m2) and round knitted fabrics (160-230 g/m2). The plain woven velvet fabrics are the most expensive fabrics to manufacture and they shine out with their maximum quality. Covered with fabric surface, polyurethane foam and light-coloured woven liner, the fabrics don’t lead to creasing and swelling owing to their cover. It has recently been seen that fabrics manufactured with flock yarns are used as car seats. The biggest advantage of this yarn is that it has a high abrasion resistance and a good thermal comfort.
Apart from furnishings and carpets, the other stable structures of the automobile are also covered by textile products. Ceiling coatings, baggage coatings, floor coatings, door and wall panel coatings are listed as internal coatings named as previously shaped structures. Ceiling coatings stand out among the markets with a high growth potential with its annual growth rate of 10 %. Aesthetic appearance, soft touch, dimensional stability, colour fastness, dirt-resistance, sound and vibration insulation and fine structure are the leading features expected from textile products used in ceiling coatings. Nylon and pvc fibres and stripped knitting technique used in the ceiling coatings give a better abrasion and pilling resistance to the product.
Aesthetic Appearance, Robustness and Abrasion Resistance Come into Prominence
Such features as high elongation, high return and shape protection are sought for baggage coatings which are created by using the fabrics having a plain appearance and short piles. Apart from appearance, the baggage coatings are also expected to be firm, abrasion-resistant, robust and easy to clean. In the baggage coatings where generally polyester and polypropylene fibres are used in the production, the nonwoven fabrics manufactured with the needle method are largely used. At the same time, in the floor coatings used in the floor of the automobile for decoration and insulation, a certain degree of hardness and abrasion is sought. Polypropylene nonwoven surface carpets which are currently planked through the method of needle punch are increasingly preferred owing to its price performance. Another sub-category of automotive textiles is the door and panel coatings, where aesthetic appearance and soundproofing come into prominence. In these coatings, nonwoven fabrics manufactured through the method of needle punch out of polyester, polyamide and polypropylene. However, polypropylene fabrics having the feature of light fastness are more preferred.
A significant number of textile products are used in the filters used in the automotive sector. Petrol and oil filters, air filters, cab internal filter, crank filter, engine oil filter and fuel tank filter are among the components where textile products are mainly used. The other fields where textile products were used in the category of automotive textiles are listed as follows: air bags, safety belts, tires. While fibres including polyester, nylon 6 and nylon 6,6, polypropylene and other fibres are used in the automotive textile sector, each one of these fibres is preferred for their different characteristics. Polyester is preferred for its ease of maintenance, abrasion resistance and colour fastness while nylon is preferred for flexibility and brightness. As to the polypropylene, it is preferred for its cost advantage and hydrophobic feature.