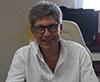
Our editorial board interviewed Mr.Mustafa Gümüş, the General Manager of Gümüş Enerji providing modernization solutions and manufacturing machineries for the textile industry since 1997. Mustafa Gümüş described modernization as “reducing the energy used, increasing the production quality”. Mr.Gümüş informed about the development process of Gümüş Enerji’s position in the market starting from the conversion of machines running with hot oil into natural gas.
Energy Saving System
Mustafa Gümüş, who is a mechanical engineer, continued his activities in the industry they have been present with hot oil and steam, mechanical installations since 1997 by starting his own company. With the introduction of natural gas and its use in the industry, the industry has started the modernizations which can be briefed as heating hot oil machineries with natural gas directly. Mr.Gümüş states that thanks to this system, an energy saving up to 40-60% can be achieved within the enterprise and continued his words: ‘’98% of the machineries in Turkey were running with hot oil as there was no natural gas. International manufacturing companies wanted high amounts and at least one month to perform the conversion with the arrival of natural gas to our country. Thanks to our successful studies we have achieved to realize the modernization of more than 1,200 machines. I have never thought that so many machines would be converted when I first started this business,’’ he said. The success of the company’s modernization enabled the company to work with Turkey’s leading textile companies like Sanko, Menderes Tekstil, Bossa and Yeşim Tekstil.
No Boiler Room Investment
The company having started to manufacture partial machines during modernization studies realized that the imported private burners are not sufficient and that they imported with high prices. Mustafa Gümüş ‘We explained that there were problems in the systems of the imported burner, but they didn’t listen us or they didn’t respond to our demands. Consequently, at the beginning of the 2000, we started the production of process burners,” he said. The company, who tried for two years to get the necessary permissions, continues to manufacture burners with Goldflame brand for many industries such as textile, tiles, steel and glass. Gümüş ‘’ Subsequent to our studies dedicated to lead our industry, we realize the heating by directly burning the natural gas in dyeing machineries,” he said. Gümüş giving information about the patented system of the company indicated that in the past, the heated steam was used to heat the flote in dyeing machines and noted that thanks to their systems, the mills no longer make investment for boiler room in addition to saving energy, and that as a result, with the conversion at a mill already having a boiler room, an energy saving at high levels is achieved. Gümüş, “Our system is compatible with all brand and type dyeing machine. When you buy a machine, you don’t get an exchanger, you don’t do the steam and condense return lines. When you get our system, you don’t need to install a boiler room.’’ Gümüş underlined that the boiler rooms in dyeing mills are not only places to generate steam for dyeing machines and indicated that they also have studies for hot oil boiler rooms and that they developed a low-pressure steam generator as well as informed that they have this project implemented at Universal Tekstil. ‘’We run the system with a rope dyeing at Universal Tekstil.”
New Generation Steam Feeder
We can generate a direct low-pressure 300 degrees steam and heat the machine with this energy. Consequently, we have been working with our system on dyeing machines very effectively. We managed to solve the open end machines in that way. Can you imagine that? We got the support of TÜBİTAK and created a new generation steam feeder and it doesn’t need steam. That is what we mean with extraordinary new generation,” he said. Gümüş giving information on energy efficiency; “On traditional steaming systems, you generate the steam outside (in boiler rooms), you bring it in and by conditioning it there, you have to obtain the right steam. Trying to adjust the pressure of the steam, whose pressure is changing, can lead to serious losses. As pressure changes, temperature changes and as temperature changes, the machine’s working conditions change. The amount of the cooling water changes. All these variables influence your production quality and the tissue, the printing color on the fabric change,” he said. Another advantage of our system compared to traditional systems is that even a machine is going to operate, this machine will need steam and steam needs to be generated in the boiler room for only one machine, however, with the system they manufacture, without the need of a steam feeder, you can directly work on the related machine. Mustafa Gümüş also claimed that they also provide great contribution to companies about workplace safety and energy savings in addition to investment costs.
Gümüş; “We obtain hot steam having a base field of 2 m and a height of 3,5 m just 1-2 m close to the machine, with only half bar pressure and without any danger. I install it just close to the machine and there is no pressure and consequently there is no danger. You just run the machine. You don’t need to run the whole mill. You are not obliged to run the steam chamber and the boiler room feeding the whole mill. You need three machines and if you only run those three machines, then you save lots of losses,” he said.