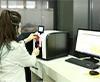
Şahin Balcıoğlu, Chairman of the Board of BLC Group, said, “As BLC Group, our artificial intelligence-based technology, which we developed with our two global business partners, enables us to fulfill the work orders lodged at the production facility with the highest efficiency. We will continue to invest in artificial intelligence technologies that triple our energy efficiency and with zero errors in production. The target of our R&D is waterless dyeing and production with less consumption.”
BLC Group is one of the prominent actors of the textile industry in Turkey with its R&D investments. The success of the group, which directly or indirectly results in export of 85% production to the world's fashion giants, lies behind its investments in technology, digitalization and in sustainability. Recently, BLC Group taken on an approach to optimize its business planning and to enhance customer satisfaction with the artificial intelligence-based automation system it has developed with its two global customers. BLC Group Chairman of the Board Şahin Balcıoğlu said that thanks to the artificial intelligence-based technologies that they have developed with two key players, they are able to fulfill the work orders lodged at the production facility with the highest efficiency.
Added Competitiveness
Explaining that the system also allows customer-based customizations in product quality level, Balcıoğlu said, “We aimed to further excellence our performance in cases where our customers direct their attention. Our new artificial intelligence-based system has also contributed significantly to our core promise of reducing our unit costs by increasing production quantities, adding competitiveness to our company.”
Energy Efficiency Has Been Tripled
This artificial intelligence-based new system developed by the BLC Group R&D team also makes a significant difference in standardization of production and works with environmentally friendly approach. Şahin Balcıoğlu, Chairman of the Board of BLC Group, says, "With our efficient combustion systems that we have developed for energy saving, we have increased the efficiency of the energy resources we use by more than 200 percent, that is, three times, and in this way we have both reduced damage to the environment and taken important steps towards protecting natural resources."
Error to Near Zero with Simulation
The importance that the textile giant attaches to automation in production played an important role in the emergence of production simulation technology. Balcıoğlu also said that by applying pre-production simulations, they can monitor performance of their products at their last stops along with the processes that need to be verified. Explaining that they were able to reduce their margin of error to near-zero levels in this way, Balcıoğlu explains, “In addition, these technologies have eliminated many indecisive stages, thus ensuring the continuity of our production plans.”
Rising In Production Technologies
BLC Group, which carries its power in textile to production technologies with the many technologies it produces today, continues on its way in developing new processes and producing different production equipment. Among the new technologies that BLC Group has brought to the Turkish industry so far are machines with zero carbon footprints, equipment with high efficiency and production capacity, technologies that make traceability transparent. Balcıoğlu said, “The production vehicles with new technology, implemented by our R&D team, come out of the project stages and come to life with each passing day.”
The Future Target Sets On Waterless Dyeing and Production with Less Consumption
Explaining that BLC Group will continue to invest in technology and artificial intelligence-based production systems and contribute to more competitive and sustainable production, BLC Group Chairman of the Board Şahin Balcıoğlu expressed his goals for the upcoming period as follows: “Our team, working under the leadership of our R&D department manager and BLC Group Board Member Emre Can Balcıoğlu, continues to work for innovative solutions in continuous improvement and production processes. The applied artificial intelligence production module is one of the leading systems in this field. In the next period, it will be on our agenda to achieve waterless dyeing, production processes that use less energy and chemicals.”