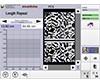
The choice of patterns for textiles knows no limits. More and more sophisticated materials are being used to this end, varying greatly in density or elasticity. This presents an increasing challenge for textile manufacturers to produce straight weft and straightened patterns. Here, the alignment according to the design often plays a greater role than the weft insertion. The German company Mahlo GmbH + Co KG solves this problem with its improved Patcontrol PCS-20 system for pattern recognition and warp control.
To ensure that customers receive the quality they want in patterned goods, textile manufacturers must adhere to the tightest tolerances in terms of parameters such as pattern repeat or pattern distortion. After all, nobody would accept distorted patterns in carpets, textile printing, woven goods and knitwear. The Patcontrol PCS straightens bow and skew distortions in technical textiles just as reliably as in terry cloth, e.g. towels, printed clothing fabrics or flocked articles. Even goods that cannot be detected with conventional scanning systems, such as lace and rustle curtains or mesh fabrics used for example in sports shoes, do not pose a problem for pattern recognition. For years Mahlo has been providing reliable support for textile manufacturers with the Patcontrol PCS. The new version PCS-20 now facilitates the production process even more.
Camera and lighting technology further developed
The system uses camera technology to detect the position of the pattern and automatically and continuously determines the pattern repeat, measures the product width, and – together with a straightener – straightens the product distortion based on the print pattern.
New long-life LED lighting generates the maximum brightness on the market, thereby extending the scanning range for darker goods. Improved cameras allow brightness control by gain and exposure time. With the Generation 20 system, more than two cameras can also be connected per measuring point. This allows a higher resolution and an even more accurate result to be achieved. A Gigabit connection allows the transmission of large amounts of data. Using a mounting aid, the exact camera adjustment can be done easily and quickly. A compact interface box at the measuring point integrates the Patcontrol PCS-20 even more easily into the existing plant.
As with all current Mahlo systems, pattern recognition is also integrated into the mSmart digitisation concept. Users, machines and processes are networked with each other and meet all the requirements of Industry 4.0.
Area of application
- Straightening of curtain and lace fabric as well as repeat measurement and control of the feed roller
- Straightening of woven and tufted carpets before a coating process
- Straightening of terry cloth (e.g. towels)
- Fine straightening of printed goods
- Report detection and sorting
- Continuous width measurement
- Logging of repeat and warp on carpets
- Residual distortion straightening of carpets at the stenter frame outlet
- Special evaluations and measurements on technical textiles
Advantages of the new generation Patcontrol PCS-20
New camera technology
- Higher resolution – more than 2 cameras per measuring point possible
- Gigabit connection
- Brightness control
- Easy camera adjustment
- CMOS technology
New LED lighting
- Larger scanning range through maximum brightness on the market
- Longer service life
Easy integration through compact interface box
Current Windows 10 operating system
The Patcontrol PCS-20 ensures the textile manufacturer complete monitoring and logging of the actual product quality. The new generation of Patcontrol thus makes an important contribution to increasing quality, efficiency and profit. Its use brings companies even closer to 100% 'Right First Time'.