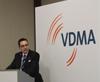
Sebastian Stolle, the sales manager of August Herzog Mascihennfabrik GmbH, made a presentation with the title ‘Technical Braiding: High Technological Braids in Textile Technique.’ During the presentation which received extensive attention at the conferences by VDMA in Istanbul and Gaziantep, Stolle introduced both the organizational structure of Herzog and the technologies they developed. Pointing out that textile products with technical function were different from apparels and they were high value-added textile products, Stolle said: “For example, in the automobile industry, technical textiles are in textile, geotextile, insulation materials, packaging and protective clothing.” Indicating that 90-95 percent of the braids used in these areas were technical braids, Stolle stated that in Turkey, braids were in the areas such as fishing, mountain climbing, yachting, medical, sports, insulation and composites.
Stolle said that interweaving three or more yarns is generally referred to as braiding, and he outlined the characteristics of braid as follows: high flexibility, high torsional stiffness under load, fiber security by means of locking, equal load compartment along the product, excellent
linking feature, elasticity / negative elasticity, 100 percent reproducibility and load reduction. Giving double braid as an example, Stolle stated that this braid was preferred in security needs such as safety and climbing ropes.He explained that these braided ropes made by PA had features such as high security, pulling loads (static) and fall absorbing (dynamic). Stolle said that double rope was used in order to pull the highest loads with the help of high-tech materials, and he added that these products provided weight savings in high stretch. Pointing out that another usage area of double braids were fishery, he continued: “In fishery, for big fish, strong ropes are used for heavy loads. In different applications, braided cords are made of high-tech materials to move the highest loads.”
Stolle stated that braids were also used for thermal insulation, and he added that these braids were produced with sleeving made from glass and different coated materials. Stolle stated that here sleevings were made from monofilament wires and many electrical components were available. Pointing out that braids were used to strengthen hose and pipes used under pressure, Stolle said: “This braid is suitable for all hoses and hose materials, and for different yarns and wires; it can be reinforced by wire or fabric and used in different cut sizes. It is suitable for many types of ventilation.”
Stolle said that they developed technologies for the production of transport, mooring and marine ropes, and he added that using synthetic yarn provides greater advantages than cable. Stolle said “Deep-water research requires longer and more powerful ropes.” and he gave information about the braiding technique and the production of carbon fiber. Stating that these braids were extensively used in marine, medicine, aircraft, sports, aerospace and automotive, Stolle said that in all these segments were significant brands among the customers working with composite.
3 Dimensional Braiding Technologies from Herzog
Sebastian Stolle indicated that they developed 2-D, 2,5-D and 3-D braiding technologies, and he touched upon the development of horizontal and radial braiding; and he continued: “With our machine RF 1/288-100, braiding is performed with 288 and 144 bobbins which can be set to radial braiding. Production cores are used in the manufacture of composite profile. In RF 1/64-100 model, on the other hand, braiding is performed with adjustable 32 and 64 bobbins. It has a braiding body and discriminant function for indoor production.
Stolle also explained composite equipment parts during his presentation. He said that these parts were made of carbon cores and high module fibers, and he gave collision box of Mercedes LR Mc Laren and front and rear bumper holders of BMW M6 as examples. Stolle called attention to the increase in the rate of use of braiding technology in medical applications. Stolle said that their technologies were used in medical suturing in various diameters and lengths, arthroscopic instruments, cables and stitches, and stents and similar products.
Close-up: Aug, Herzog Maschinenfabrik
Stolle said that Herzog, one of the most important technology producers in braiding and winding, was founded in 1861; and he added that the company’s head office was in Oldenburg, Germany and the company was managed as a family company for 5 generations. Stolle gave information about the work of the company: “More than 500 different machine models and materials have been developed for different applications. We put our signature under turn-key projects as well as single machines with 135 high-quality employees. As Herzog, we produce specially equipped machines as well as the standard machines for our customers.” Indicating that Herzog had a worldwide network of sales and marketing, Stolle noted that the company Klip Kimyevi Maddeler was their representative in Turkey.
Performing all the production in Germany, the company covers mechanisms and the structural parts for braiding machines, and composite parts such as ship rope, compressed hoses and pipes in the fields such as sports, filtration, automotive, aerospace, marine and medical.