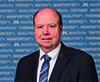
Monforts, an expert in advanced technologies for dyeing, finishing and coating of textiles, was established in 1884. Leveraging its know-how in textile engineering from its establishment to the present, it exhibits fully digitalized solutions through the evolution and increased sophistication of electronic drives and increasingly sophisticated technology. Monforts Montex stenter dryers have a leading position on the international market across all sectors. Mr. Thomas Paffgen, Monforts Regional Sales Manager, make his statements to our magazine. We interviewed Mr. Paffgen about Monforts' operations and the situation in the market in general.
Q. What are the core principles and values you pursue in the sector? What kind of approach do you undertake in environmentally friendly production and recycling?
A. All our technologies are designed to achieve the maximum production with the minimum use of resources – water, energy and raw materials. This is where technology developers like ourselves can really make a difference and where we continue to make progress, since in the past these processes have been energy and water intensive. The latest Montex stenters for example – especially combined with a downstream Eco Applicator – set new benchmarks in terms of energy efficiency and the minimum application of finishing chemistries.
Q. What impact has Covid-19 had on your company when we talk about short range to mid-range targets in general?
A. Initially we were of course forced to make some operational changes, but these were quickly overcome by modern digital technology and everyone adapted to the situation. Now, I would say that the Covid-19 restrictions are no longer such a barrier to business.
Our machine engineering plant in Austria has also been able to continue uninterrupted with no supply problems.
In Turkey in particular, Monforts business has been very positive since the start of 2020 and we have a good number of machines currently at various stages of installation and commissioning – including more than a dozen new Montex stenters.
As the Monforts representative in Turkey, Neotek has remained our essential solutions partner on the ground and has been with us every step of the way. From our German headquarters here in Mönchengladbach, we are providing extensive teleservices involving on-site conferencing, the checking of all the electrical drives and electronics and providing software updates, spare parts, troubleshooting and support. Any problems arising are being very quickly resolved, so although it is not ideal, we are happy with the situation.
One notable project we have recently completed is a new Monforts Thermex dyeing range for Hamle in Çorlu, as part of its ongoing strategy of continuous investment. This valued customer already operates a ten-chamber Montex stenter and two of our sanforising ranges on which it carries out an extensive range of finishing processes. The new line has some very advanced automation features which ensure the machine operators have full control over the entire system.
A change we have noticed since the beginning of 2020 is that many of our Turkish knitted fabrics customers are now looking at technical textiles and investing in coating units, as well as wider width lines.
Q. Can you tell us about your in-house sales activities and successful co-operations over the years? What impact did these partnerships have on your sales figures and production volume?
A. In addition to all the current in-house activities I have mentioned, we have many years of experience in establishing the ideal processing conditions for all kinds of fabrics, in order to achieve optimised production and full repeatability. This comes through working closely with our customers, both at their own plants and at our Advanced Technology Centre (ATC) here in Mönchengladbach. This has proved invaluable in fully assisting our customers to achieve the results they are aiming for. Our close work with regional representatives around the world has also greatly contributed to securing our sales and production volumes.
Q. How successfully have you adapted Qualitex 800 to your production lines and what are the advantages of using this technology?
A. The Qualitex 800 touch panel control system was first introduced for Montex stenters and is now standard on all of our machines, including Thermex dyeing ranges, Monfortex compressive shrinking ranges and Montex®Coat coating units.
It allows all parameters to be easily automated via touchscreen, and many thousands of separate process parameter records to be generated and stored by the data manager.
Since its launch, it has met the highest acceptance and appreciation by textile machine operators and mill managers worldwide due to its intuitive and easy operation.
We have subsequently introduced advanced sensor technologies making it possible to access comprehensive technical machine data from any location using our Smart Support and Smart Check apps. This allows for vastly simplified and targeted analysis for both controlled planning and production, and insights harnessed from the data can subsequently be used to further optimise the production process. At the same time, potential sources of error can be remotely anticipated and eliminated to considerably minimise downtime. This full digital control package is available for all Monforts machine ranges and makes operation smarter, and at the same time, considerably simpler.