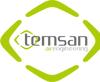
Temsan Makine which is one of the first firms which come to mind about air-conditioning in Turkey and in the world started its business in a small atelier by manufacturing agricultural machines and spare parts in 1960 and continues its operations in its plants covering 50.000 square meters. Cem Kesim, Member of the Governing Board of Temsan, which continues the success they obtained in the sector of climatization and air-conditioning in the textile sector with D-Plus and Maritaş answered the questions of Textile Magazine Group about the Slasher dyeing machine they introduced to the textile sector.
Temsan stands out as the first firm manufacturing Slasher machine in Turkey. The slasher machine manufactured by the firm as patented was put into use in Maritaş Tekstil last month. Although planned as Tübitak R&D project at the beginning, it was completed as an independent R&D project after one-year work. Providing information about the machine and system they developed, Cem Kesim, member of the Governing Board of Temsan, stated that they conducted works to decrease - even slightly - external dependency of investments in denim production at the end of R&D works and they produced the Slasher machine as a Turkish engineering project from mechanics to software and added that the system they developed provides users with the opportunity to purchase and use optional capacity. While slasher machines available in the market can reach production capacities up to 700.000-750.000 per month, this machine can make production up to 1.300.000 m per month thanks to the optional purchase possibilities. While the machine reaches this capacity, operation costs increase only by 12 % and this is advantageous especially for commercial collection manufacturers. The machine also provides the opportunity of operation with up to 16 becks in practice thanks to the design flexibility. Another distinguishing feature of the machine is that it is the machine with the longest oxidation path among the dye becks. Based on its experience about the impacts of climatization techniques on yarn and fiber, Temsan Makina designed a special air conditioning system for this machine and increased oxidation quality by up to 4 %. With its English and Turkish software, it is user friendly and it is easy to adapt.
He also stated that they operated the Slasher machine first in Maritaş Denim factory with which they carried out the R&D project and they wait for KTM 2017 to be organized in April in order to launch the system.
Kesim added that, “As Temsan, we produce projects special to the firms. There is no standard in machinery and air conditioning works that we carry out. Each project is different. We are specialized in industrial air conditioning in the textile sector. When we decided to manufacture Slasher dyeing machine, the feedbacks we received motivated us. Wherever the brand of Temsan is present, our responsibility is bigger. We constantly need to make the better and the one of higher quality.” Kesim stated that they have already become the leader of Eurasia in the air conditioning sector with both production capacity and quality and service speed and market share and they have given a new impulse to the market with the Slasher machine.
Denim in the World; Kot in Turkey
Based on the work pants manufactured out of canvas for gold diggers by an American named Levi Strauss in 1850, the Genovese sailor style pants were produced out of denim. Jeans were named after this city and became the trend-setting cloth with the highest production amount. These fabrics named as denim or blue jeans were offered to the Turkish consumers by an entrepreneur named “Muhteşem Kot” in 1960s. Since then, the surname “Kot” became a common name for denim fabrics and pants manufactured out of these fabrics.
Turkey Ranks 4th in Denim Fabric Production
It is estimated that the production of denim which is among the most popular fabrics realizes as billion meter/year. In the Asian continent where almost 75 % of the global denim production, China is the country having the highest denim production capacity. Latin American countries rank second, India ranks third, Turkey ranks fourth, Pakistan ranks fifth and Bangladesh ranks sixth.
Turkish denim sector which has reached an annual production capacity of 668 billion meters is intense mainly in Kahramanmaraş, Malatya, Kayseri, Bursa, Adana, Tekirdağ, Uşak, Edirne and Bartın.
Innovative Technologies in Denim Production
Increases in the use and production of denim bring innovations to the production technologies in this field as well. There are 3 common methods in the colorization of indigo-dyed warp yarns in denim fabrics. These methods are called as slasher, roop dyeing and loop dyeing. Although indigo dyed warp yarn can also be obtained through dyeing techniques, they are not preferable.
Slasher dyeing stands out as one of the most important methods among these methods thanks to its speed, effectiveness and first investment cost advantages. Slasher dyeing is performed as a continuous process where yarn groups in a creel containing 300-400 warp yarns per beam are firstly subjected to pretreatment (wetting, causticization, sulfur dyeing) and then dyeing and washing processes and process is terminated following the drying and sizing processes. Besides, ventilation (oxidation) among becks is among important process steps.
In Slasher dyeing, the indigo dyestuff known as CI Vat Blue 1 is used. This dyestuff does not dissolve in water and becomes solvable after reduction. The machine where this dyestuff is made consists of creel, pretreatment-dyeing-washing becks, oxidation and sizing parts. While the number of becks in the machine is optionally selected, machines with up to 12 becks are available in the market. Number and structure of these becks are influential especially on the depth of the color obtained. Another important point for these machines is the ventilation/oxidation part. The height of this part and the length of the path that the yarns follow in this part before diving into each beck are also influential on both depth of the color and wet fastness obtained afterwards. Yarns obtained with this dyeing method are yarns ready for weaving and also offer great advantages in terms of the speed and ease of production.
Yarns wound on the weaving beam from the slasher dyeing machine are transferred to the weaving section without the necessity of further process. Indigo dyed yarn used as warp yarn is usually transferred to the finishing section after having turned into raw fabric with white weft yarn. In the finishing section, unlike classical non-denim fabrics, flat finishing process also known as partial mercerization is applied on raw denim fabrics and fabric becomes end product.
It is known that there are about 20 slasher dyeing machines in Turkey. For the world, this number is thought to be around 300. When the potential of denim production in Turkey is considered, machinery investments in this field gain more importance. Domestic investments planned for the production of slasher dyeing machines in particular support this sector to gain more added values. Turkish textile machinery manufacturers have already started accelerating their initiatives in this field.