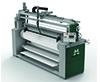
Tekstil Business interviewed Monforts Area Sales Manager Thomas Päffgen for the May issue of our magazine. During the interview, activities in Turkish market and their participation in the WasserSTOFF Project highlighted as major headlines.
Q. Would you give us some information on the machinery range and available technologies of Monforts?
A. Monforts Area Sales Manager Thomas Päffgen: Monforts specialises in advanced technology for fabric finishing based on successive industry developments over many decades and we are celebrating our 140th anniversary this year. We were founded in 1884 in Mönchengladbach in Germany, where we are still headquartered and where our Advanced Technology Centre (ATC) is also situated. All of our our machines have been manufactured at our plant in Austria since1982. Monforts Montex stenters – for processes such as drying, stretching, heat-setting and coating – are the industry standard for the fabric finishing industry, particularly in the sectors of denim and home textiles, providing a number of advantages in terms of production throughput and especially in energy efficiency and savings. The other key technologies in our range include relaxation dryers, Thermex dyeing ranges, Monfortex compressive shrinking ranges and Montex®Coat and coaTTex coating units.
Q. What are the stand out features of Monforts technologies? Which distinctive features of machinery and technology are applied to remain competitive specifically in the denim and home textile market?
A. One major benefit of Monforts dyeing, finishing and coating machines is that they are built to last. Textile companies making major capital investments in new manufacturing lines rely on durability from the company’s production ranges, and it’s for this reason that there are currently an estimated 2,000 Monforts machines in operation worldwide – some of which were first installed over 30 years ago. This doesn’t mean, however, that they can’t benefit from many of the advances in performance and automation that have subsequently been made by Monforts. The retrofitting of specific modules with new control and drive technology – going far beyond the basic replacement of spare parts – can have a significant impact on the performance of an existing line.
Q. What level of progress has been made by Monforts to keep up with sustainability, digitalization and recycling? What measures are implemented to protect the environment and to save resources?
A. We are constantly updating and improving our machines. With the latest Montex stenters, for example, overall energy savings of up to 40% can now be achieved compared to a conventional stenter with no heat recovery or energy optimisation measures. Another example is with the ongoing development of the Thermex universal hotflue line for continuous dyeing, condensing and thermosoling, which achieves unrivalled reliability for manufacturers of denim and home textiles. The Thermex provides exceptional cost-effectiveness when dyeing both large and small batches of woven fabrics and benefits from the Econtrol® process, developed with DyStar, for reactive dyestuffs. This is a quick and economical one-pass pad-dry and wash off process, with drying in the hotflue at 120-130°C and controlled humidity (25-30% by volume) to obtain fixation in 2-3 minutes. Econtrol® ensures excellent reproducibility of all colours, improved dye penetration on difficult fabrics and no risk of the browning of cotton or other cellulose fibres due to the low fixation temperature. As such, it is the ideal process for fast change technology and operational savings – not to forget the savings in water and chemicals.
Q. Which target markets are closely monitored by Monforts? What is the importance of Turkish market for Monforts and which products serve best for this market?
A. We watch all of the major markets closely and gain valuable feedback by working closely with both our network of national representatives and service centres, and, of course, our customers. We are active worldwide and in all of the major textile manufacturing centres – Bangladesh, Brazil, China, India, Pakistan and, of course Turkey. Investment in new technology and capacity expansions are very important to our Turkish customers, in order to stay ahead in terms of sustainable, high quality production. We find that they carefully assess the benefits of each advanced new technology in order to thrive in a sector that is constantly changing and as a result, have adopted ongoing strategies of continuous investment.
Q. Which products and technologies will be showcased at Istanbul Fair in 2024?
A. We will exhibit a Montex stenter chamber with an integrated overhead heat recovery unit at the stand of Monforts partner Neotek. The heat recovery unit is just one of a range of energy saving options the company is now providing for both new and existing line installations and we will be pleased to discuss these possibilities at the show. We will also introduce our latest coaTTex coating unit exclusively dedicated to air knife and knife-over-roller coating. For single-sided application with paste or foam, the versatile coaTTex is suitable for both incorporation into existing finishing ranges as well as installation with new Monforts lines, especially Montex stenter systems. A wide range of coatings can be applied to fabrics for providing functions such as waterproofing, liquid and gas protection and breathability, in addition to foam lamination and coating, including black-out coating.
Q. Would you inform us on the mid-term vision of Monforts in the global markets? Which future-oriented technologies are now being pursued and what are your capabilites and strengths to achieve these in the foreseeable future?
A. The cost of energy remains a major concern for textile manufacturers and it’s an area we are paying much attention to. Last year we introduced the concept of using green hydrogen as a new energy source for textile finishing, drying and related processes and we are currently leading a consortium of industrial partners and universities in the three-year WasserSTOFF project to explore all aspects of this fast-rising new industrial energy option. The target of the government-funded project is to establish to what extent hydrogen can be used in the future as an alternative heating source for textile finishing processes. This is involving tests on laboratory equipment together with associated partners, with the results transferred to a stenter frame at the Monforts ATC. Green hydrogen’s potential as a clean fuel source is tremendous, but there is much we need to explore when considering its use in the textile finishing processes carried out globally on our stenter dryers and other machines. Everybody knows that textile finishing is a high energy consuming process and to make the processes more efficient, we already offer several solutions, but as a technology leader we are also rising to the challenge of exploring alternative heating options to be ready for the future.