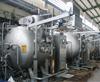
Monforts continues to sell stenter all over the World. One of the leading scarf manufacturers of Germany, V Fraas has purchased a Montex 6500 stenter at its Zhangjiagang factory in China. Purchasing Montex stenter in order to meet the growing demand, the company manufactures cashmere and wool scarves at the same time.
Fraas is to speed the production of wool and cashmere with this new facility; and the company aims to increase quality in production and energy costs. In the sector since 1880, Fraas operates in the heart of Upper Franconia in Germany. The company's product line is composed of a wide range of products with high quality fabrics, gloves, shawls, capes, scarves, woven. Private Labeling division of the company manufactures for other leading clothing and accessories brands.
Working in various parts of the World with a design team, Fraas is doing market and trend research in leading cities such as New York, Paris, Düsseldorf and Shanghai. Within the context of its own production work, the company produces about 10 to 12 million scarves and other textile accessories annually in its manufacturing facilities in Germany, the Czech Republic and China. Having started operating in 2003 in Zhangjiagan, the company has managed to increase the number of its stores to 70 in China since 2009. Juergen Pittroff, executive director of operations of Fraas which is in the region with German capital entirely, stated that initially they aimed to produce warp knitted and woven scarves; however, in time they decided to purchase stenter for scarf production.
Emphasizing that they made the decision to expand in 2006, Pittrof underlined that they decided to purchase stenter for wool and cashmere in 2009. Pittrof said that there was no difference between the new machine they purchased and the stenter produced in Germany; and he continued as follows: “At first we had some doubts but we were satisfied in terms of quality and reliability; and this was enough for us to make a fast decision. The stenter is operating for four days a week, with one 10-hour shift per day. Production is gradually rising. We aim to increase our market share considerably with the new stenter we use.”
Monforts is to Recount Efficiency at CINTE
Monforts is to present the works it developed in terms of energy at CINTE Techtextil China 2012 which will be held on October 22-24 in Shanghai. With the study complying with the ‘Blue Competence’ initiative introduced by the German Engineering Federation (VDMA), Monforts aims to provide energy saving in textile finishing and dyeing. Monforts always works to reduce emissions and improve sustainable living conditions in the new machines. Increasing costs of energy needs and all the materials used in production are forcing the companies to find cost-effective solutions. In this sense, Monforts continues to work with full force. Designed as a new heat recovery module, the Montex 8000 stenter, working with a fully automatic cleaning system for heat recovery, comes forward with a reduced infeed distance of knitted fabric. Fluff sieves for efficient cleaning, vacuum system and further enhanced visual attributes to facilitate the tele-service opportunity are among the remarkable features of Montex 8000.
A new heat recovery module ‘Eco booster HRC’ with a fully automatic cleaning system is introduced, replacing the earlier modules, manually cleaned, tubes system. Featuring a ‘honeycombed’ design, the machine automatically cleans the machine during operation and this makes uninterrupted operation possible. Consuming less material, showing a stable operating performance and failing less thanks to the cleaning filters, the system can be integrated into the roof of Montex. The system does not need extra ventilation assembly.
Another prominent feature of the machine is that it is equipped with vertical chains carrying a heavy load in order to meet market needs. These chains are known to be suitable for heavy knitted fabrics, nonwovens and technical textiles. In addition, the machine gives its own segment a different perspective with fluff collection feature. Each new rotating ‘disc type’ sieve is equipped with a vacuum cleaning system. Mounted on the machine, these discs collect fluffs and ensure machine productivity with an efficient cleaning. The new stenter is also available with a reduced infeed distance between the infeed roller and the needling point for knitted fabrics. Reduced by 60 mm, the distance prevents eventual edge curling. Providing 30 per cent energy-saving with energy towers, Monforts technology works with five integrated heat recovery modules.
A particular Solution for Coating with ECO Applicator
Monforts ECO Applicator has been developed as an alternative to the impregnation system with a history of 70 years. While there is around 65 percent chemical use during the processing of cotton in the impregnation system, only required amount of chemicals are available in the Eco Applicator system. Due to the high volume of bath in the impregnation system, more chemicals have to be used for the fabric. However, the amount of chemicals can be controlled precisely depending on the prescription in the new system.
Thus, providing 20-30 percent less chemical usage, the system also saves energy by 40 to 45 percent. In this system, the liquor can be applied to the fabric in 3 different ways, on one side of the fabric, on both sides of the fabric, two different chemicals on the two sides of the fabric. Using Trough (Flat) and cylinder techniques, the system applies only required amount of liquor / coating contacting with the fabric with a new cylinder. The application field includes felt finishing, coating materials and medical textiles, nano-coatings, and fabric softener.
Monforts Fully Supports Blue Competence
Informing about Blue Competence launched by the German Engineering Federation (VDMA), Monforts Textilmaschinen GmbH & Co. KG. Vice President of Marketing Klaus A. Heinrichs underlined that they were providing full support to this initiative. Heinrichs pointed out that they had no hesitation in participating in the initiative; and he added that they started studies on energy management much earlier, and set targets.
Reminding that for many years textile finishing had operated with chemical and thermal processes, Heinrichs said: “The energy costs are high, and the use of chemicals absolutely essential. But with innovative ranges and intelligent ancillaries, Monforts has succeeded in optimizing these processes.” Heinrichs listed their 3 products that exemplify the Blue Competence initiative as follows: Econtrol, the ECO Applicator, Energy Tower and ECO Booster.
Klaus A. Heinrichs said that chemicals were used to fix the dyestuffs on the textiles during textile dyeing; and he added that classic processes for the dyeing of cotton textiles included 250 grams of salt per litre of treatment fluid. Stating that when calculated for three-shift operation, up to 500 t of salt was required annually, Heinrichs said that for the dyeing and cleaning process with subsequent washing, a total of around 1545 kg of chemicals were required for dyeing processes. Heinrichs expressed that besides the use of these high volume chemicals, an immense amount of energy was also required for the subsequent drying process.
Noting that together with Dystar, one of the leading producers of dyestuffs, Monforts had developed the Econtrol process for pure cotton textiles, Heinrichs said that the dyestuff was fixed during drying with this process and steaming process was not needed. Remarking that only 20 gm. of salt was required per liter now, Heinrichs said that the dyeing result was available after just two minutes and not only after 12 to 24 hours. Heinrichs indicated that for fibre blends, Monforts had developed the Econtrol TCA process together with Dystar, and he added that it enabled polyester and cotton to be dyed simultaneously and not in two process steps.
Energy Costs Fall, Productivity Increases
Heinrichs said that the ECO Applicator was a unit significantly reducing the initial moisture content before the drying process, and he continued as follows: “As a rule, the fabric is transported through a trough containing the finishing and dyeing liquor. The ‘wet’ fabric is then dried by means of a stenter. The drying energy is a major cost factor. In the ECO Applicator, the liquor is applied very thinly by steel rollers. As a result the new unit achieves a maximum energy yield - because moisture that is not applied to the textile fabric does not later have to be dried. Savings in heating and electrical energy of up to 65% are possible if the initial moisture content in the textile is reduced from 70 to 40%.”
Dealing with Energy Tower and the ECO Booster as the last example, Klaus A. Heinrichs noted that the Energy Tower with a versatile and flexible design is used within the principle of heat recovery. Heinrichs underlined that the module drews in the exhaust air from the drying process and returned it via heat exchangers to the range so that the air was preheated to around 90°C and only had to be heated to 150°C, therefore the high drying temperature was reached more quickly and energy costs were reduced. Heinrichs said: “The Eco Booster HRC can also help to minimize the energy costs when using stenters. By contrast with purely static heat exchanger modules, the new module actually cleans the stenter during operation; eliminating standstill times for maintenance. Only 100 liters of water are used for cleaning. The Eco Booster runs fully automatically, therefore it reduces costs of operation.
Heinrichs remarked that Monforts was a trendsetter in the field of textile finishing technologies, and he added that energy efficiency was an important global topic with textile producers faced with the challenge of coming to terms with volatile energy and raw material prices and the ecological demands of retailers and ultimate users. Heinrichs finished his words as follows: “More efficient technology may cost more, but the procurement costs account for less than 20% of the life-cycle costs if you take the total costs for energy into consideration. The payback period for the Monforts technology generally lies in the order of 18 months to two years. Anyone who would like to work with more efficient and energy-saving technology comes to us.”