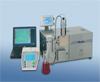
Mathis AG providing test service for the textile industry with its laboratories in Switzerland is well known for its studies dedicated to increase the quality since 1968. The company having a wide production spectrum is one step ahead with its studies covering coating machines and systems. Mathis being present in the South American market with its office located in Brazil also provides service and sales service with its offices in America, China and India.
The departments of the company performing studies with globally important textile players at the headquarter in Switzerland are as follows: R&D Department, Department of Mechanical and Electronic Engineering, Machinery, Software department for the development and programming of the machine and system controllers, Documentation Department, Service and spare parts department, A large test center for customer trials, Spacious goods and spare parts warehouse containing all components required to build the machines and systems, Metal workshop for processing steel and stainless steel sheets, Electrical department for the electrical installation of all machines and systems, Assembly shop in which all machines and systems are fully assembled and tested and Shipping department.
SmartLiquor to Increase Productivity
The SmartLiquor system is designed to help exhaust and continuous dyers to increase the efficiency of their operation. The unit works for all major dyestuff classes, e.g. reactive, disperse, acid, metal-complex, direct etc. and can be connected to any dyeing machine, laboratory or production, as long as there is some liquor circulation or a pad liquor. As of 2012, the system is used in 13 countries by dyehouses, dyestuff and auxiliary manufacturers and research institutions.
Experience has demonstrated average productivity increases of 20 to 25% with existing machinery. SmartLiquor also provides water and energy savings. On the other hand, the so-called ‘Dye Solubility Coefficient’ allows the analysis of dye solubility on-line during dyeing conditions and thus the determination of when the dyes actually start to diffuse into the fibre .For continuous applications, SmartLiquor is particularly suited to eliminate tailing problems in Cold Pad Batch (CPB) and E-Control.
Mathis continuing to its researches with its experience over 40 years keeps getting successful results. SmartLiquor strengthened with extra software enables to include the measurement data into lot-specific optimised processes. The export software minimized the water and energy consumption during the rinsing process.
SmartLiquor being used since 2008 by Masureel located in Belgium increase productivity and provides crucial savings. Fabrice Van Hee, R&D as well as lab-in-charge at Masureel made the following statements: “We are a package and hank dyehouse, processing a variety of fibres, among them polyester, viscose and wool. We connected SmartLiquor to a pilot-scale package dyeing unit in the production area and analyze with its help exhaustion speed and dye compatibility of our recipes. For disperse dyes, we gained some new insights by using SmartLiquor’s dye solubility coefficient. SmartLiquor is no doubt a useful tool for troubleshooting and process optimisation.”
Superdyer