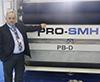
Pro-SMH stands out with the production of slasher, sizing and direct warping machines which are widely used in dyeing indigo dyed warp yarns for denim fabrics. Pro-SMH had received a great deal of interest in the denim sector with its slasher indigo machine, which was designed to work at 2 meters.
Bringing a new breath to the sector with slasher machines that they produce, Pro-SMH will break new grounds in the sector with the new machines they are about to finish for denim and fabric finishing processes.
Cüneyt İşman, one of Pro-SMH Founder Partners, said they have offered slasher machines providing high quality, efficiency and velocity for weaving preparation processes as a result of long R&D studies, and he answered the questions of our publishing group about their existing machinery line and new studies they have carried out.
"We produce at the world class quality standards in terms of product quality", says İşman and continues, "We attached great importance to R&D works in the production of our machines. We have produced unique machines for which we can give a guarantee of use for many years. Especially we took a very important step in software and metallurgy. All materials used were selected according to the function of the machine and the place used. All of the used iron and stainless metal components have long life blends. We have been providing our customers with quality guarantee for many years since the machines we manufacture are assembled with superior technology and excellent workmanship."
Noting that they have been producing with years of experience in weaving preparation machines for the industry sector, İşman stated they are the reason for preference with the confidence they give to the customers. "We have been conducting this business for about 25 years. We have been in the production of machines that serve companies worldwide for many years and we started to manufacture machinery as people coming from this very industry. The machines we have produced are not that easy to manufacture. We have a substantial experience in our management team thanks to their past in this sector. We have been working with 24 countries for long years. We have been providing service, spare parts and upgrade modifications. The trust of the clients in us increased significantly thanks to these works of many years. We are now a preferred company in the sector thanks to the experience we have in in machinery, technology and market.
Pro-SMH Signature In Denim Sector
Stating they sold 4 slasher indigo, 12 sizing machines and 8 direct warping machines during the last one and half year, İşman said they sold sizing and warping machines to countries such as Egypt and Bangladesh. "We have completed the installation of 2 out of the 4 slasher indigo machinery we have sold so far and they started to operate. We are going to deliver 2 more within this year. We have 9-10 projects we have been negotiating with apart from these machinery", explains İşman.
“There Is No Machine Group That Cannot Be Produced In Turkey”
Stating that domestic machinery manufacturers are supported by institutions such as KOSGEB and TUBITAK within R&D studies, İşman emphasized that there is no machine group that cannot be produced in Turkey when necessary support is received. "There are prominent supports. It is now up to us and industrialists. There is nothing that cannot be achieved in the whole machinery line of the textile sector. It is very important to believe that we can do it. When we decided to manufacture this machinery and share it with our German friends, they laughed at us. But today, we produced 4 indigo, 12 sizing, 8 warping machines in one and a half year. We succeeded in producing all of these from scratch by creating our own infrastructure and our own supplier chain from scratch. We continue to work successfully.
Ground-Breaking Innovations In Denim Sector
Manufacturing ground-breaking machinery thanks to their technological infrastructure and properties in Turkey, Pro-SMH breaks new grounds yet again with 2-meter working width in the slasher dingo machine. "Currently, we are the only firm that can produce and operate an indigo machine with double head and 2-meter working width. As of today, we started to manufacture and install the slasher indigo machine of 2.20 meters width", says İşman.
İşman further explains the advantages of the machine as in the following: "Our machines have double heads. We made systems and software that enable more synchronous and more precise operation. Since our machine is equipped with automatic calibrating system, it can operate again without requiring any calibration after processes such as grinding and coating. Since it keeps this calibration constantly, it reduces the start and stop breaks at the beginning of each party in minimum, thus reducing the time loss in the party and enabling it to be finished within a relatively shorter period. When the machine we called Flying change stops, we reduce the possible loss of production to the smallest level thanks to a system that removes the waste from the inside.
Sharing their targets for 2018, too, İşman suggested economic and political fluctuation and actions has affected the sector and they, as industrialists, would continue to provide a convenient environment to enable foreign money to flow to Turkey. "Despite all the challenges, we, as the industrialists of this country, continue to do our best. We have also experienced hard times like this before, but we believe the textile sector in Turkey will continue to grow for many more years to come", comments İşman.
"In addition to Slasher, we are now preparing for warping processes. In 2018, we will introduce new types of weaving pre-processing machines. If everything goes smoothly, we may organise some studies on warping dyeing during KTM 2018. We are planning to finish our warping machine until ITMA 2019 Barcelona Exhibition", explains İşman, providing insight into their new studies they are planning to carry out in 2018.
There have been very important developments in dyeing technology. I can assert that we come up with innovations that will change the denim market. One of these is our ultrasonic work. We also have a nitrogen study in the same field. We can say that our ultrasound studies have come to an end. Our first machine will be launched within 4 weeks. I strongly believe we have revolutionised denim and fabric finishing. Now that we have seen the results, we are planning to experiment the operating conditions. Should we succeed, we will break new grounds, revolutionising denim and fabric finishing segment", concludes İşman, suggesting they will also offer innovations in the dyeing technology.