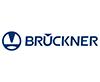
Who would have thought after the last ITMA 2019 in Barcelona that the world would change so drastically in a very short time, that a virus would force the whole mankind to stay at a distance and that Europe now also has to experience a war. Add to this the global supply chain problem, extreme price increases in many areas and general uncertainty about the future development of the markets. Such times of crisis are challenging, but also reveal opportunities.
A Lucrative Textile Production Process
The German machinery producer Brückner used exactly these chances and repositioned itself during the pandemic period. For more than 70 years, the family-run company has been specialized in individual finishing concepts for textiles, technical textiles, nonwovens and floor coverings. The current challenges in the textile industry are serious. The clear increase of the energy costs and the general uncertainty of the energy supply as well as political requirements make a profitable textile production more and more demanding for many companies.
Brückner responds to this with a newly developed stenter concept with double heating system. Depending on availability, the lines can be operated with gas or oil, but also other combinations with steam or renewable energies are possible. This means that production delays and machine downtimes can be avoided as far as possible. In addition, Brückner has developed intelligent assistance systems for its machines that support the machine operator in using the best possible process to operate the line as energy-efficiently as possible. Further energy savings are possible with new energy-efficient motors or heat-recovery and exhaust air cleaning systems. This also helps to avoid harmful emissions.
Brückner's Enhanced New Technologies
But many textile producers are also focusing on reducing chemicals. For this purpose, Brückner’s further developed ECO-COAT minimum application unit can make a decisive contribution. Knitted and woven fabrics, but also nonwovens can be finished on one or both sides via different fabric paths. With the minimum application via an engraved roller, a single-sided application of up to 100 g/m² can be achieved. A double-sided and higher application quantity is achieved, for example, by impregnation in the nip. Irrespective of the selected fabric path, a very small liquor reservoir means that only minimal quantities of waste water are produced when changing batches or liquors, and the use of chemicals can also be significantly reduced. In addition, less water has to be evaporated in the subsequent drying process than, for example, in the case of impregnation in a water bath, so the energy requirement is significantly reduced.
On the two upcoming trade fairs ITM in Istanbul and TECHTEXTIL in Frankfurt in June, interested customers could personally get an idea of Brückner's new developments. This includes e.g. the new OPTI-COAT 2in1 coating unit which combines the advantages of application via floating knife and knife-over-cylinder in one system. Due to its design, the unit offers good accessibility for maintenance and cleaning work and delivers excellent coating results.