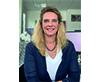
In our correspondence with Verena Ruckh, Head of Advertising and Marketing Department of Brückner, a company that has been manufacturing complete lines for textile finishing for many years, any topic of interest was taken into agenda. Brückner, one of the specialized firms that maintains its business conduct in its own premises in Germany, sustains its position as the market leader. Brückner, which offers customer-oriented solutions with the various technologies it owns, continues to serve sector representatives successfully with machinery range.
Q. In which areas do you operate as Brückner? Can you tell us about your products and services in general?
A. BRÜCKNER, established more than 70 years ago by my father, is world-wide leading group of companies in the development and construction of complete lines for textile finishing. In the beginning our core competence was the stenter for classic textile finishing. In the meantime we enlarged our portfolio considerably. The headings summarizing our activities are: continuous lines, machines and know-how for drying, finishing, surface treatment and coating of web-like materials. This includes all types of finishing lines for classic textiles but also lines for coating and finishing of floor coverings, nonwovens or glass fabric. In order to serve our customers as well as possible, we naturally also offer comprehensive services, such as energy consulting, technological consulting, worldwide service and digital systems for easier machine operation.
Q. What is your opinion on the dramatic changes in manufacturing methods available with fast paced technology and constant innovation? How successful have you been in pursuing change and implementing it in your operations?
A. About three years ago, we built a completely new production plant in Germany to keep up with this trend. In our new production plant we are able to act clearly faster and more flexible; large and heavy machinery components can be assembled and moved much easier and we automised a major part of the production steps. Our location in Germany is very important to us, as the know-how of our employees is also very valuable for us in automated processes. Our product portfolio is very large and our flexibility is very high, therefore the proximity of our own research and design divisions, of other partners in the development of our products such as universities and research partners to our production is very important. Short distances and regular exchanges ensure the high quality of our products.
Q. Would you inform us on the level of water and energy savings achieved by choosing Brückner coating and finishing systems? Where would you place yourself in the industry amongst competitors pursuing sustainability and recycling in their mills as well?
A. Finishing is probably the most energy-intensive process in the textile value chain. For this reason, we began developing energy-saving systems and promoting environmentally friendly processes many years ago. In the development of new machines, resource and energy-saving aspects are now fundamentally at the forefront. There are many starting points which we have already implemented and from which our customers can also benefit and thus increase their competitiveness. We offer our customers various assistance systems to use the lines as energy-efficiently as possible in order to achieve significant savings in heat and electrical energy. Our proven split-flow air system also leads to higher production output with reduced energy consumption. In addition, our plants are equipped with energy-saving drive systems and, on request, heat-recovery and air pollution control systems. With our optimized heat-setting automation and dwell time control, energy can be saved again while productivity is increased. Above all, however, we offer our customers technological advice and training - whether in our Technology Center in Leonberg or directly at the customer's site. Often, when we look at the production processes with the customers, we discover further savings potential for the entire plant, which, if implemented consistently, can lead to a significant reduction in energy and working time in the individual operations.
Q. Can you give us some information on future strategies of Brückner? What stage are you in to achieve them on a global scale?
A. As you know the next ITMA will take place in 2023 and of course every ITMA is a key event for the global textile industry. Until then, we will introduce even more energy-saving products to our customers, which we are already working on today. At the same time, we are continuously working on an even better remote service for our customers, because the effects of the pandemic have shown that many things can be done online, even the commissioning of machines. Predictive maintenance of the lines will also be a big topic in the future. After all, regardless of the price of a machine - it only costs extra when it is down and unable to produce. Therefore, continuous and expert maintenance, supported by remote service, is an important standard for the future.
Q. How would you evaluate 2020 for your company? What gains and losses you experienced in 2020? Would you assess global markets and turkish market in 2021?
A. The year 2020 was eventful in many respects - firstly because many customers did not know how their customers would behave and thus cancelled or postponed orders, and secondly because we also had to digitalize our work even more than before in a very short time. In addition, there were delivery interruptions from subcontractors who were unable to deliver on time because of Covid. We ourselves never had any interruptions, but were able to deliver all orders as planned thanks to a great deal of flexibility. The Turkish market has developed very positively after a short period of restraint. Through our very experienced service technicians in Turkey, we have always been able to provide competent support to customers, and have even received one of the largest orders for carpet coating in 2020!
Q. Would you like anything to add...?
A. The cooperation with our Turkish customers is always very positive, because the companies have very well trained personnel, who can also properly use the quality and productivity of our machines. Many European textile manufacturers are currently relocating their procurement to Turkey, and the close proximity and the competencies already mentioned guarantee fast, reliable and high-quality deliveries. This in turn is only possible thanks to the high-quality textile machines installed in Turkey. We would be pleased if we could support and accompany even more Turkish customers in their production changeover to high-quality products in the field of classical and technical textiles. Here we could contribute our many years of experience and know-how profitably for both sides. We are convinced that the textile manufacturers in Turkey offer excellent potential for this in every respect, be it technically, financially or from a sales perspective.