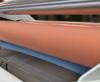
Offering significant savings in terms of production costs, Benninger Küsters introduced its new system which requires less use of chemicals, water and energy for the textile sector. With the newly developed Küsters S-Roll technology, short and full-length knitted and woven fabrics can be dyed at lower costs. Thanks to this system which offers really important advantages especially at woven and knitted fabrics, dyehouses gain high production flexibility and the same results can be achieved even after years with the dyeing formulas enabling the users to maintain the same colours.
With the developed cold Pad-Batch (CPB) method, the Pad-Batch dyeing process conducted with reactive dyes is carried out with the impregnation process created within the padding mangle. In this way, the factors occurring independently from the machine during the process of dyeing are minimised. The system, which ensures that the dyestuff is applied to the whole fabric in a smooth and equal manner after a short notice when the dyestuff interacts with the liquid, prevents the impacts on the dyeing conditions due to different absorption values obtained in the fabrics with different fibres and yarn thickness values, fabric tension, weft distortion, different moisture values, temperature of the liquid, features of the dyestuff and dyestuff migration occurring at the edges during the drying process.
Reproducibility
Thanks to Küsters S-Roll technology, the dyeing process ensures that the fluid is applied to the entire fabric surface in a perfect and equal manner and to the “edge-centre-edge” parts at different qualities. Owing to the reproducibility feature of Küsters S-Roll, pressure deviation is electronically conducted throughout the whole cylinder in a controlled way. Besides, “Blue Nip” cylinder coating also found in the former models has been developed and the necessary application conditions and the materials to be dyed can be adapted to one another in an ideal and long-lasting manner.
Cost-Effective Production
Contidos dosing system offering additional production safety during the dyeing process and 24-cycle cooling and heating management system increases ease of use and reproducibility of the dyeing padder. In order to prevent the formation of “dead spaces” in the dye back, which is one of the common problems encountered in the dyehouses, fluidity conditions are tested in consideration of the different speeds and fabric qualities with computer-aided simulations. Besides, it is attempted to minimise the factors influencing the result of the dyeing via “mini U-flows” developed in the system.
When compared to the exhaust dyeing method Küsters S-Roll dyeing method offers such advantages as reduction of the amount of water used in the dyeing process by a significant rate per kilogram of fabric to be dyed, use of fewer electrolytes, low tension, lack of necessity for enzyme process since no pilling occurs on the fabric and stability of the fabric weight. These advantages increase the quality of the dyeing process and accordingly, textile products in addition to resulting in economic benefits. Furthermore, clients always have online access to the Competence Centre of Beninger AG by using Telelink system for immediate technical support and thus, productivity values can always be controlled.
Benninger Achieves Saving up to 25 %
Erdinç Dinçer, Chairman of the Governing Board of Benninger Dinçer Mümessillik that strives at offering all kinds of information and technical support to the Turkish textile market in terms of correct machinery investments and acts as the distributor of Beninger Küsters in Turkey stated that: “Benninger has become, after purchasing Küsters, capable of offering all kinds of machinery concept in terms of the dyeing and finishing solutions for open width woven and knitted fabrics.” and added that: “Preferring the machines of Beninger means achieving savings in production when reducing profitability rates of today are considered and total production cost is analyzed. Machines of Benninger provide such advantages which will reduce production costs considerably as use of fewer chemicals, less water and energy. In particular, a saving up to 25 % is possible in relation to the use of chemicals.”
Trying to offer all kinds of information and technical support to the Turkish textile market in terms of correct machinery investments, the firm continues its studies on technical textiles and open width knitted fabric systems. Touching upon the purchase of Küsters Tekstil in 2007 within the scope of these studies and investments, Erdinç Dinçer added that: “Buying Küsters which was world’s leading technology provider in terms of machinery and plants for textile wet finishing, Beninger incorporated the firm completely. Gaining more strength with this purchase, Beninger has become capable of offering all kinds of machinery concept in the field of dyeing and finishing solutions for open width woven and knitted fabrics in textile.”