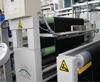
A. Monforts Textilmaschinen GmbH, which has proven its expertise in textile finishing, has been the most important supplier of the global market for a long time. The headquarters of the 128 year old company, which has an important place among the German machinery manufacturers, is located in Mönchengladbach, the home of various industrial businesses. Monforts, one of the important supporters of TexCellence, combines its expertise in textile finishing with the original qualifications of NRW region. Monforts manufactures textile machines and lines for the finishing processes of the woven and knitted products and exports 90 percent of its production. With its approximately 100 representatives across the world, the company has a strong position in these markets.
Monforts, which performs an intensive R&D process for innovative technologies, offers solutions to the textile manufacturers both in the sale and after sale processes. The company also supplies original spare parts for the machines and lines sold all around the world. With the ‘Direct Ship’ parts programme, the demand for spare parts is met as soon as possible. The product range of the company has been supported by innovations in order to maintain the higest level of quality and efficiency in all stages of textile finishing. The company offers stenters, relaxation dryers, continuous dyeing facilities, shrinking facilities, denim finishing facilities, technical textiles/coating, automation technique, exhaust air cleaining services and heat recovery systems to the textile manufacturers.
Montex stenter is used in the fixing, finishing and heavy duty finishing processes of the knitted and woven fabrics. In Thermex dyeing facility, the dyeing, condensation, thermosoling and continuous Pad-Batch (Econtrol) processes stand out for the knitted and woven fabrics. DynAir relaxion dryer is used in relaxing shirinking, drying and thermobonding of the knitted fabrics open or in tubular form, or of nonwovens. Compressive shrinking and sanforising processes are applied on the woven and knitted fabrics on Toptex rubber belt shrinkage machine.
Monforts has developed the signed MONFORIZED for the textile manufacturers who finish their fabrics on Monforts machines. The company that has developed Monforized to set international standards, helps the products produced at this quality standard to gain both a high market price and an increase in value.
Stenter Technology Never Stops
Monforts, which continuously adds innovations to the Montex stenters in line with the developments in the finishing sector, offers TwinAir system in addition to the PLC control technology ‘Qualitex’, which has proven itself both in woven and knitted fabrics. The innovations that Montex Stenters have brought are as follows; ‘Masterguide’, which allows optimal setting of the operation process, integrated weft straightener, pinning device, V-Steamer, Selvedge gluing device and Glue Flue for the glued selvedges.
The machine is run through the direct gas heating, oil heating, steam heating combined electric – steam heating, hot water heating system and electric heating system. Exxotherm, the high-efficiency indirect gas heating system, provides lower investment costs and a higher efficiency. In the software of the stenters, Q-Soft is used for production planning and documentation with a central interface. Hercules chain can operate for long years without the need for greasing in Montex stenters, which High-tech Stenter Chains are included in,
The Twin Air Plus System, which increases the economic and ecological performance of Montex stenters, can be included in the system depending on the customer’s request. Cadstream E, which offers the most suitable solution for the frequently changing fabric widths, ensures a higher production speed with the same energy input. With the new integrated heat recovery system, Monforts uses innovative concepts in its machineries for more economy and more ecology for the advantage of its customers. The waste heat produced in the thermal process and contained in the exhaust air is discharged via the exhaust air ducts integrated into the stenter chamber directly into the air/air heat exchanger. The new Monforts heat exchanger is integrated into the roof construction of the stenter without the need for a secondary installations.
Dynair Relaxation Dryer Decreases the Costs
Dynair Relaxation Dryer, another important product of Monforts, has an important place in finishing. The modular twin-belt dryer has been designed for relaxation shirinking of knitted fabrics with feed in either open/wide of tubular form. In this form, a special air guidance system with dynamic plusating air currents allows the fabric to glide through the dryer in a sinusoidal wave.
Monforts has developed DynAir 6000 with new accessories to ensure a better fabric finish and less maintenance costs throughout the finishing processes of knitted fabrics with feed in open/wide of tubular form. Qualitex 540 or Qualitex 740 is presented as conventional control system in Montex DynAir, which is a dryer with tumbler-like characteristics.
Thermex 6500 for Continuous Dyeing
Monforts’ continuous dyeing machine Thermex 6500 is described as a modern system in this field. The system preferred for economic solutions in the dyeing processes of the long and short batches, performs continuous dyeing, condensing and thermosoling with highest reliability and at highest fabric speeds. The system is combined with the infrared segment as a pre-dryer in thermosoling and condensing processes, for drying processes after dyeing and for pre-drying. With its innovative technology, Thermex performs thermosoling and wrinkle-free drying without migration.
New Standard in Shrinkage : Monfortex & Toptex
Monfortex and Toptex shrinkage units designed for the finishing processes of the woven and knitted fabric including denim, are preferred by the finishers worldwide. With this system, reproducible minimum residual shrinkage values are achieved. It has been certified that Monfortex &Toptex surpass the international shrinkage standards in most cases.
Monforts Participates in DTG 2012 with Its Solutions for Savings
Monforts, which has an assertive position in the Asian market, attaches great importance to the fair and organizations held in this region. An DTG 2012, Bangladesh’s greatest fair of textile machineries/technologies, that will be held on February 9-12, 2012, Monforts focuses on the products providing energy saving. The local representative of the company in Bangladesh will exhibit innovative equipments for the knitted fabric sector at the booth of Bengal Technology Company. Ergonomic applicator and soft coating solutions, the new Econtrol T-CA and Montex 8000 stenter are among the technological products that are going to be exhibited.
Montex 8000, which has introduced to the sector at ITMA Barcelona, held in September 2011, includes various innovations for the knitted fabrics, nonwovens and technical textile applications. With ECO Booster HRC integrated to Montex 8000, energy saving of 30-35 percent is ensured. A successful result can be taken by using a ECO Booster HRC module, which is a standard feature of all Montex stenters, in a stenter with 8 chambers. The Heat Recovery module, incorporating an automatic cleaning system and included in ECO Booster HRC, increases efficiency by eliminating the start and stop interruptions. The researches that Monforts has been conducting for 10 years, have shown that 60 percent of the total costs consists of energy consumption. In line with these researches, the company developed the heat recovery systems integrated to the stenters.
Monforts’ new Eco Applicator has been developed as an alternative to the padding system that has a 70-year history.
In the padding system the chemical use reaches up to 65 percent while, in Eco Applicator system, this amount depends on the amount needed. Due to the high liquor volume, in padding system much more chemicals are needed to be used on fabrics. In the new system, the amount of the chemicals used can be controlled precisely according to a prescription. By this way, the system, which provides 20-30 percent less chemical usage, also provides energy savings of around 40-45 percent. In this system the chemical liquid can be applied on the fabric in 3 ways; on one side of the fabric, on both sides of the fabric and two different chemicals on each side of the fabric.
Monforts’ Energy Tower, which is one of the up-to-date products of the company, has been developed for retrofitting the existing stenters or hotflues. Taking advantage of the high temperature of the exhaust air, the product, launched with the slogan ‘Stand Alone’, heats the fresh air passing through the heat recovery system. The system ensures savings of up to 30 percent in energy costs.
Calendar of Events for 2012 Focuses on Asia
Monforts, which has an important share within the market and which produces innovative technologies in the field of textile finishing for all kinds of woven, knitted, denim and technical textiles, includes important events in its calendar of events for 2012. These events, which focus especially on the Asian market are as follows; DTG Exhibition on February 9-12, 2012, in Dhaka, Bangladesh, MEGATEX Exhibition on March 1-3, 2012, in Lahore, Pakistan, VDMA Symposiums on March 3-5, 2012, in China, Techtextil Russia on March 12-14, 2012, in Moscow, Russia, ITM Exhibition, on April 21-24, 2012, in İstanbul, Turkey, Asia’s greatest machinery fair, ITMA ASIA, on 12-16 June 2012, in Shanghai, China, IGATEX Exhibition, on October 3-6, 2012, in Lahore, Pakistan, India ITME, on December 2-7,2012, in Mumbai, India.