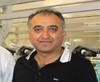
Being one of the most important yarn producers of Kahramanmaraş and Turkey, Kipaş Holding Company has continued to improve its production volume in 2011. Kipaş Holding Company reached 300.000 spindle rings, 20.000 rotor open-ends and has been continuing its production in many other textile segments as well as yarn.
With its 120.000 m² closed plant, 335 weaving machinery, 1500 workers, the Holding Company produces 20 million meters of non-denim and 30 million meters denim fabrics a year. Kipaş fabric production facility, which provides 10% of Turkey’s yearly yarn production, has a wide range of products including all fibre group fabrics, particularly cotton fabric.
Being Kahramanmaraş’s first Holding Company, Kipaş produces 300 tons of yarns a day with its 200.000 m² closed space, 5 ring yarn factories with a capacity of 205.000 spindles, 3 open-end yarn factories with a capacity of 20.500 rotors, and 2000 experienced workers. Yarn production facilities, which are associated with Kipaş Holding Company have always ranked among the most prominent yarn suppliers in the sector with their invariably high quality production, prompt delivery and their structure which puts the client on the focus. The Group Manager of Kipaş Holding Company Yarn Operations Ahmet Duygal talked to Textil Dünyası about their operation.
The 30% of the production is exported
Ahmet Duygal pointed out that they have a product range that can provide for all the need for yarn in the sector, and that they produce ranges such as carded, hosiery, compact, core spun, shantung, open-end, synthetic and blended, dyed, plied and technical yarns. Duygal also implied that the yarns that Kipaş produces are presented to knitting and weaving producers who manufacture men’s, women’s and children’s clothing, denim, furnishing fabric, sheets, home textile, blanket, sportswear, towels, casement, canvas, duck, industrial fabrics and technical fabrics. After stating that they directly export the 30% of the production, Duygal went on to say: “The 30% of the production that is left after the thirty-percent-export is used in our denim and non-denim production, and the rest 40% is sold to other domestic exporter companies. In 2011, our production volume as a group has reached to 300.000 spindle rings and 20.000 rotor open-ends. Last year, we have accomplished 75.000 tons of carded, hosiery and, compact production and and 40.000 tons of open-end yarn production. The 10% of the yarn production in Turkey is provided by our group.”
Duygal reminded that they use Rieter, Marzoli, Zinser, Trützschler and Schlafhorst brand machinery in their yarn operations and said: “We produce 121 tons a day with one hundred sixty 205.536 spindled ring machines; 132 tons a day with forty seven 17.592 rotor open-end machines.” Duygal underlined that raw materials are provided primarily by suppliers who provide high quality products and fast service, according to their costs and added: “We provide our needs from domestic and foreign markets according to our area of use.” Duygal went on: “As a firm that constantly follows the developing technology, with a national awareness that doesn’t compromise high quality we prefer to buy domestically produced fibre if the fibre to be bought is produced domestically and provides service that is suitable to our purchase policy. We provide fibres that are not produced domestically –such as cupro, tencel and viscose fibres- from foreign markets.”
Ahmet Duygal also answered our questions about foreign machinery purchases: Machines produced in European countries that catch hold of the technology are preferred. The machinery purchases made according to our high quality, fast production policy are also a result of this policy.” Duygal underlined that they achieve high quality rates with the production made by technological machinery and said: “For this reason, as Kipaş Holding , we purchase the latest technology for our new investments as well as the modernization of our existing machines.”
We got our payments in cash during the time of crisis
Duygal also stressed that the sector suffered globally from time to time and continued; “During the global financial crisis, we weren’t affected much as the structure of Turkish banking system is solid; but as a precaution, we tried to make our sales in cash as far as possible. As we made our sales in cash or with a maximum 60 days instalment, we didn’t have a cash flow problem. Because we didn’t want to face a possible financial cash flow problem. Parallel with the relief in the finance sector in 2011 following this cash flow problem, we made new investment decisions. We didn’t focus these decisions that we had made on one sector but extended them to various fields like textile, energy, paper and cement.”
R&D Activities Should Gain Speed
Duygal underlined that the additional taxes brought by the government during the times after the crisis had a quality that prevents current deficit, and said that the domestic labour and energy as well as the Turkish currency became more valuable. Duygal, who also commented on the future of yarn production, completed his words saying: “As done in Europe in the previous years, for the sake of the development of yarn sector, exporting the machines that completed their economic life to the countries that are in the East of Turkey should be facilitated. Import of the used machined in the country needs to be reduced as much as possible and speeding up the research and development activities is of critical importance to improve the high productivity and quality concept in the yarns that are currently being produced in Turkey increasingly. This is an important factor for the new textiles to extend. As we all know, textile is a vast accumulation of knowledge and a huge expense that needs to be supported by R&D department after it reaches a particular infrastructure. And encouraging this is crucial.”
*********
Kipaş’s History of Milestones…
- 1986, The First Open-End plant in Kahramanmaraş
- 1989, The First Fabric Weaving Plant in Kahramanmaraş
- 1992, The First Yarn Twisting Plant in Kahramanmaraş
- 1994, The First Yarn Dyeing Plant in Kahramanmaraş
- 1996, The First Woven Goods Dyeing Plant in Kahramanmaraş
- 1997, The First Ready-made Garment Plant at Factory Level Bozkurt in Kahramanmaraş
- 2003, The First Denim Plant in Kahramanmaraş
- 2006, The First Holding Company in Kahramanmaraş