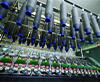
The production of ring yarns from blends of recycled cotton and virgin cotton places the highest demands on the spinning process. The Rieter ring recycling system was developed to meet these requirements, enabling customers to produce fine ring yarns of high quality with a share of almost 40% recycled fibers.
Fiber blends from recycled and virgin cotton are currently mostly processed on rotor spinning machines. The few ring yarns are almost exclusively available in coarse counts and with a recycled cotton content of no more than 20%. The industry now faces the challenge to produce fine yarns with a higher recycled fiber content. Rieter is continuously testing new processes and settings in addition to developing technology components to achieve better results in producing fine yarns with a higher content of recycled cotton.
Cooperation with Recycled Fiber Manufacturer Recover
During several trials, different ring yarns of fineness Ne 30 were spun and compared with each other. They included a combed yarn made from 50% recycled cotton fibers and 50% virgin cotton, and a carded yarn made from 25% recycled cotton fibers and 75% virgin cotton. The Spanish company Recover – specialized in the production of recycled cotton – provided the material for the trials. Black recycled fibers were chosen to better distinguish the recycled fibers from the virgin cotton.
Adapted Settings and Components
The biggest challenges in spinning recycled fibers are controlling the short fibers and reducing neps and impurities. The blending of the two fiber components was done in the blowroom with the precision blender UNIblend A 81 for the best results. The card C 81 can be configured and equipped specifically for the raw material – for example, with clothing sets specially developed for material with a high short fiber and trash content. The new Rieter draw frames RSB-D 50/26 offer enhanced suction for cleanliness, even in the calender area, resulting in longer cleaning cycles and fewer thick places. When recycled fibers are processed, four-fold doubling can be supportive. Here, an additional web nozzle improves web guiding and guarantees fault-free operation with a high short-fiber content. Moreover, recycled fibers can now be selected as an application in the expert system SLIVERprofessional, providing recommended settings for the entire machine based on raw material data.
Removing Disturbing Fibers with the Comber E 90
The comber E 90 can optionally be used in the ring recycling systems. When combing blends of recycled and virgin cotton, disturbing short fibers and neps are removed (Fig. 1). This makes it possible to increase the share of recycled fibers in the blend. The assumption that combing removes a large part of the recycled fibers was disproved. Only the particularly short fibers, which interfere with the process, are combed out of the blend.
In the test with 50% recycled content, the noil extraction was at 24%. At the same time, unevenness and imperfections were both significantly improved (Fig. 2). This quality advantage can also be used to additionally increase the recycled content. Visually, the combed fiber blend with the black recycled material was significantly darker compared to the carded position with 25% recycled content, even after the combing process. In the combed ring yarn, the recycling percentage reached 38%, which is higher than in the carded recycled yarn.
Ring Spinning Machine with Q-Package
For optimal processing of recycled fibers on a ring spinning machine, special fiber feeding in the drafting system is required. Drafting should generally be as controlled as possible. Trials on the ring spinning machine showed advantages for the use of the Active Cradle with a stepped nose bar. For finer yarns from Ne 20 and above, an additional pressure bar (pin) can be used (Fig. 3). The result is an improvement in unevenness as well as a reduction in imperfections.
The ring recycling systems which include the comber are very promising when the share of recycled fibers is increased, and fine yarn counts are produced. Several internal studies as well as customer results validate that combing has a positive effect when processing recycled cotton blends.
About Rieter
Rieter is the world’s leading supplier of systems for manufacturing yarn from staple fibers in spinning mills. Based in Winterthur (Switzerland), the company develops and manufactures machinery, systems and components used to convert natural and man-made fibers and their blends into yarns in the most cost-efficient manner. Cutting-edge spinning technology from Rieter contributes to sustainability in the textile value chain by minimizing the use of resources. Rieter has been in business for more than 225 years, has 18 production locations in ten countries and employs a global workforce of around 5 600, about 16% of whom are based in Switzerland. Rieter is listed on the SIX Swiss Exchange under ticker symbol RIEN. www.rieter.com