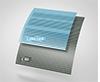
The card C 80 has been completely redeveloped – but it still contains all of the solutions that have been prized by Rieter customers for the last few decades. One look at the innovative technology demonstrates that the C 80 sets new benchmarks in terms of quality, productivity, raw-material yield and ease of maintenance.
At the ITMA 2019 trade fair in Barcelona, Rieter presented the new card generation C 80 for the first time. The carding length of 3.2 meters and the 40 engaged flats spread over the 1.5-meter working width creates a basis for a significant production increase while maintaining optimal sliver quality. Rieter is quite assertive in the production data of the C 80 developed. Based on the statement made by Rieter, in comparison with the current benchmark, the C 80 produces up to 30% more card sliver. This means that the number of cards in the spinning mill can be significantly reduced and noted that, ‘’Where four cards would have been required in the past, now only three are sufficient.’’
Using the central adjustment, the carding gap can be precisely set to within one hundredth of a millimeter – so it is perfectly adjusted to the output and the raw material to be processed. The energy-efficient drives and low exhaust air volume also lead to significantly lower energy costs per kilogram of card sliver produced.
Optimal Sliver Quality Thanks to a Larger Carding Area
The size of the active carding area has the greatest influence over the sliver quality. With a working width of 1.5 meters and 40 flats, the C 80 has an active carding area that is 68% larger than conventional systems. This is the reason behind the extraordinarily high sliver quality provided by the C 80
Raw-Material Costs Savings of 1%
The size of the active carding area has the greatest influence over the sliver quality. The C 80 facilitates a raw-material cost saving of 1% thanks the maximum technological cross-section, as well as pre and post-carding zones that can be equipped individually and configured according to the raw material.This does not sound like much of a saving, but even when only 1% less raw material is required for the same annual output, it has considerable impact.
Thanks to the integrated Q-Package, adapting to a new raw material is quick and simple. It includes low-wear mote knives in the pre- and post-carding zone with differing extraction widths. Inserts can be changed quickly without the need for tools. Four different options are available for the various degrees of contamination. As a result, the raw material can be utilized with maximum flexibility and profitability. With the new card generation C 80, Rieter has set another milestone in carding technology. The aim is to offer the customer the best possible user experience. This is why a large number of C 80 models have already been sold to spinning mills with the highest productivity and quality requirements.
About Rieter
Rieter is the world’s leading supplier of systems for short-staple fiber spinning. Based in Winterthur (Switzerland), the company develops and manufactures machinery, systems and components used to convert natural and manmade fibers and their blends into yarns. Rieter is the only supplier worldwide to cover both spinning preparation processes and all four end spinning processes currently established on the market. Furthermore, Rieter is a leader in the field of precision winding machines. With 16 manufacturing locations in ten countries, the company employs a global workforce of some 4 570, about 21% of whom are based in Switzerland. Rieter is listed on the SIX Swiss Exchange under ticker symbol RIEN. www.rieter.com