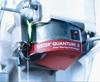
In addition to the fluctiations observed in cotton, as the quality management gained importance, the manufacturers are now being affected by the economic difficulties more. USTER®, which is the sector leader especially with the technologies it has developed in yarn quality management, comes to İstanbul to share its solutions with the Turkish textile manufacturers. With USTER® HVI 1000, the company that will participate in ITM, which will be held on April 21-24 at TÜYAP, ensures quality yarn production at the lowest cost. It is underlined that the superior technology of USTER® helps the Turkish yarn manufacturers to cope with the economic problems.
While the international buyers demand high standard yarns, Turkish yarn manufacturers have to struggle against cotton contamination, visable polypropylenes and the other problems caused by the other foreign substances. These problems and the fluctiations observed in the raw cotton costs make it difficult to solve these problems.
The experts state that since the cotton prices countinue to fluctuate, the yarn manufacturers should be careful about providing quality yarn without harming their customers with unwanted price increases in yarn. It is stated that considering the unstable structure of the market, the most effective quality method in yarn production offers a great advantage and stability to the manufacturers. USTER® is stated to have the know-how and specialist support to help the yarn manufacturers to cope with the untability in the cotton market. USTER® applies the production disciplines ensuring a higher quality, lower waste and a more strict cost control.
Managing the Quality Control from the First Minute
With the combination of laboratory and testing and monitoring solutions through the process, USTER continues to offer solutions for the whole quality management process. More importantly these solutions ensure quality in every step of the production from raw cotton to the finished fabric.
Today, when supply and price are the determining factors in the selection of raw cotton, the spinning mills tend to get the maximum value from the yarn they purchase. Consequently the companies may engage in the process of faulty production. USTER® HVI 1000 is a device, necessary in solving these problems. The machine that provides the users with the opportunity to optimize and manage the bale arrangement at the beginning of fiber preparation, ensures the highest quality yarn with the lowest cost and with the existing raw cotton.
USTER® AFIS PRO 2 Has a Critical Importance
Minimizing the fiber damage, optimizing the quality and reducing the amount of waste by making the correct machine settings between the roving frame and the blowroom are all of vital importance. USTER® AFIS PRO 2 single fiber test allows th user to control machine settings and maintenance cycles by measuring the material at each process through the blowroom, carding, combing and roving equipment.
Inadequate control of the raw material throughout these preparatory phases can lead to expensive mistakes later. USTER® AFIS PRO 2 puts spinners in control of their raw material, providing detailed test data on neps, seedcoat neps, short fiber content, fineness, maturity, trash and dust – all critical yarn quality parameters.
Smart Clearing Technology Balancing the Quality and Productivity
In a competitive yarn market, the yarn manufacturers want to avoid customer complaints and claims for substandard quality. More expensive raw material prices make this need even more pressing. USTER designs these solutions to safeguard the yarn manufacturers from this situation. In addition to the fiber quality circle provided by the USTER® HVI 1000 and USTER® AFIS PRO 2, the latest-technology yarn clearing options of the USTER® QUANTUM 3 has the feature of completing the picture by monitoring every meter of yarn during automatic winding.
These smart clearing features offered to the manufacturers help the user to remove the disturbing defects. The machine prevents from overengineering the yarn quality and by this way, lower number of cuts and an optimum balance between quality and productivity are ensured. It also helps achieving more efficiency with fewer cuts. USTER® QUANTUM 3 brings a new feature to the yarn quality. In order to ensure the best balance between the spinning machine and productivitiy needs, the system checks, analyzes and reports how to adapt the yarn clearing limits in the winding machines. Since the introduction of USTER® QUANTUM 3, a great number of orders have been placed for winding machines and it is stated that in the upcoming moths the unit installments will continue anyhow.
The new capacitive, optical foreign matter sensors are among the main features of USTER® QUANTUM 3. These sensors are able to see everything in more detail compared with the old generation clearing systems. With its strong processing electronic, the system can see for the first time the whole body of the yarn. The yarn body consists of nominal yarn and tolerable natural variatons. The new foreign matter sensor has multiple light sources through which it can detect all kinds of colored foreign fibers. It also helps distinguishing between troublesome colored foreign fibers and vegetable matter. The powerful contamination package of USTER® QUANTUM 3 is completed by a new polypropylene clearing feature. Thanks to the technological developments, as a result of several researches, USTER® QUANTUM 3 has shown that it increase the PP detection rate according to the existing industry standards.
The only thing that carries the system one step further is not just the sesor technolgy, but also the new central clearing unit with a 14 inch touch screen and a larger and faster memory of USTER® QUANTUM 3. This unit can establish a real-time relationship with the new generation USTER® QUANTUM EXPERT data system. By this way it becomes possible to compare the clearing settings changed in a winding machine and to synchronize them in similar yarn lots.
Other Advantages for the Spinning Machines
Uster Technologies is the only company to offer ‘Total Testing’, which has an unmatched correlation of laboratory and online tests to provide ideal process optimization. Online testing gains importance day by day for the yarn spinning facilities in Turkey to maintain their competitive power. Thanks to ‘Total Testing’, USTER® efficiency, offers the best in both techniques; effectiveness, comprehensiveness and consistency. The main aim of ‘Total Testing’ is described to continuously develop the production processes of the spinning facilities. This means detecting the deviations and optimizing the process to minimize waste, while achieving a consistent quality.
In order to optimize both productivity and quality, the ideal quality system combines the quality measurement with the developments in the spinning. With these innovations offered by USTER®, the productivity level can be increased by 3-6 percent by decreasing wastes, cuts and breaks. Due to the fact that it is hard to estimate the raw material prices and more importantly because of the fluctiations in the cotton prices and the inconsistencies, today ‘Total Testing’ is more useful than ever. Besides, with USTER®‘s QUANTUM 3 modern clearing technology, it is now easier to use the system.
USTER® is known for its structure recognizing the importance and dynamism of the Turkish yarn manufacturers. The company wants to support the Turkish spinners to help them in optimizing their use of costly raw material. USTER has started to provide its customers healthier and direct services after moving its Turkey office from Istanbul to Adana.
USTER® TESTER 5 For Fancy Yarns
India is one leading denim manufacturer of the world. Arvind, One of the major players of this market, gives importance to fancy yarn effects to create the denims the fashion business demands. Nitin Chokshi, Chief Manager, Quality Assurance within the company, stated that the company has built an expertise in the design, production and quality control of fancy yarns. Chokshi also stated that they help the other companies within the sector in this matter and added that testing is vital, to evaluate the relationship between cotton fiber parameters and the slub creation process for a continuous and reliable control of the yarn production process.
Chokshi added that they trust the technology of USTER in this process and added; “USTER's Fancy Yarn Profile tool, as part of the USTER® TESTER 5, provides tangible benefits on a daily basis. Considering its ability to evaluate fancy yarn characteristics, their relationship with the manufacturing process and their effect on ultimate fabric appearance the Fancy Yarn Profile from USTER gives great confidence in controlling the yarn quality,” said Chokshi.
The Fancy Yarn Profile has a precise sensor technology to measure and analyze slub yarns. Specially-tailored software to provide users with detailed reports on all important characteristics of the yarn. Aspects such as slub length and frequency, mass increase and decrease at critical points are accurately calculated to determine numeric values for yarn quality
With this latest software, which allows the yarn to be checked for periodic faults, a spectrogram with removed slubs is displayed. Mass diagrams can reveal potentially damaging long distances in the yarn where slubs are missing. Data from scatter plot can be combined into 3D graphics showing mass increase, slub length and frequency. Overview information from the system can be followed with a daily quality control report, including fabric appearance. and details of any loss of production efficiency in knitting or weaving. The device playing an important role in denim production can mix the differences in slub types and yarn counts and works such as mixed effect patterns by the Fancy Yarn Profile, which is a part of USTER® TESTER 5.
About Uster Technologies Ltd
Uster Group is the leading manufacturer of high-tech products for the textile industry in the field of quality measurement and certification. In addition to providing testing and monitoring instruments, the group offers services and systems allowing quality optimization in the entire process of the textile production. In addition to the final finished fabric output services, it comprises cotton and wool, all synthetic fibers and crude textile fibers such as filament yarns. Uster Group determines the benchmark that is the basis for the textile trade at assured levels of quality in the global market. The Group’s aim is to further develop the Know-How systems on quality, productivity and costs in the textile industry.
The Group is headquartered in Uster, Switzerland and continues its activities through a worldwide market organization complemented by technology Centers. The company has sales and service subsidiaries in the technology markets in Uster (Switzerland), Knoxville (USA) and Suzhou (China).