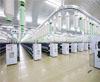
One of the companies setting technological standards in yarn production, Oerlikon Schlafhorst is to showcase its innovative products at the India Itme exhibition. Bombay Exhibition Centre is to host the event on December 2 to 7. Oerlikon Schlafhorst, offering significant benefits for cotton producers, aims to increase strength with technological spinning machines in the Indian market. The Company is to reach its customers with the machines of Autocoro 8, BD 448, Autoconer X5 and Zinser.
Fierce competition in the global arena leads companies to focus on efficiency in cost and production. In this sense, Oerlikon Schlafhorst aims to offer all global spinners, especially the Indian market, their technologies, with their own solutions. In a prominent position in the field of spinning machines in the Indian market, Oerlikon Schlafhorst is known as a company preferred by Indian manufacturers. According to a statement made by Oerlikon Schlafhorst, Indian yarn manufacturers achieved an increase of 25 percent in production using Oerlikon brand machines.
Staff Cost Decreases with BD 448
Oerlikon Schlafhorst unleashed a revolution by spinning a yarn at a rotor speed of 200,000 rpm. with Autocoro 8 a year ago. In addition, offering cost advantages in spinning, the machine is preferred by many companies in terms of production efficiency. Performing production at a very high level of productivity with the new model belt-driven machines, the spinning mills aim to improve their rotor speeds up to 10 percent. Another machine the company is to exhibit at the exhibition is BD 448, one of the most important technologies in its class. Pointing out that they saved up 7 percent in the staff costs with this machine, Oerlikon Schlafhorst authorities guarantee reaching the highest operating speed within a maximum of ten minutes. Ensuring energy savings by 10 percent compared to the previous generations of BD, the machine provides facilities for performing yarn spinning process including the thicker yarns up to the number Ne 1 with high efficiency.
Safe Automation for More Efficiency
Automatic doffing is becoming increasingly standard in terms of costs. It is becoming increasingly difficult to find suitable staff for this job, especially the spinning mills. Waiting times and machine downtimes adversely affect the efficiency of the enterprise. With the technology of automatic doffing, Zinser guarantees high-level work in terms of economy and efficiency to companies. Zinser CoWeMat is defined as the most reliable and the most affordable doffing technology. Frequency inverter control central drive within the technology offered by Oerlikon Schlafhorst allows synchronized operation of the both drives. This mode of operation significantly increases efficiency. During doffing, a photocell follows the process for a smooth working process. If a malfunction occurs, the machine automatically stops and interrupts production. Pneumatic outer grippers with a precise take-up and three-point grip grasp the bobbins and tubes securely and precisely at the tube tip. Thanks to the technique of grasping the bobbins at three-point, the possibility of damage to the yarn on the bobbin is prevented. In connection with the yarn breakage technique of the spindle of Zinser, these outer grippers stand out with their suitable structure for high tenacity yarns. The ring spinning machine can be linked directly to the winding machine. This direct link permits perfect harmonization of spinning and winding capacities.
Asia Market-Oriented Technology; ZinserImpact 71
The company is to present Autoconer X5 V and ZinserImpact 71 at India ITME exhibition. ZinserImpact 71 technology produced by Oerlikon Schlafhorst is arbitrarily presented with Zinser CoWeMat, the fully automated doffer. Customers get a chance to have a significant reduction in spinning costs. The new generation machines ZinserRing 71 and ZinserImpact 71 aim to meet the market needs of today's Asian textile industry. Oerlikon will try to create a difference with Autoconer X5 machine at India ITME. The quality package of the Autoconer X5 sets the benchmark for individually and flexibly adaptable package quality with maximum productivity. Autoconer X5 is defined as the ideal complement to the traditional spinning technology, and provides value increase in terms of flexibility, quality and productivity.