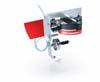
Powerful manufacturer of textile quality control technologies USTER ® will meet with clients in 2nd hall at the booth 214B in ITM fair. The company will especially share important information about its MN100 technology which is offered as a solution against neps in yarn. The errors that occur in the process of yarn production create a serious burden in terms of cost and this situation forces the manufacturers to find a solution. Offering practical keys to companies for these problems, USTER ® offers comprehensive solutions to the problems with its new MN 100 nep measurement device. This effective nep measurement device allows to control the manufacturing process with the methods of imaging system. The manufacturer minimizes the error rate of the final product by closely following the whole process.
What makes the USTER®MN100special is its range of application across processes from raw material through roving. The USTER®MN100is based on the industry-standard AFIS®and offers many of the same nep measurement advantages. It is a tool spinning managers can use as the basis for key decisions about quality, maintenance, and process settings.
Small Device With Big Impact on Production Cost Optimization
The nep diversity causes that the manufacturers experience serious problems about transaction costs. The efforts of companies to increase profits with the sustainability of high productivity and quality constitute one of the most important issues to find a solution. The control charts provided by the USTER® MN100 give an overview of all processes, to identify machines that are not optimized, as well as checking the effectiveness of maintenance programs. Savings can be realized through less machine downtime and lower usage of materials, by controlling maintenance cycles with the help of the USTER®MN100.Vital in ring spinning is the size distribution of neps in the roving being fed to the ring spinning machine. The errors disappear as a result of the fact that MN100 measures the roving material and determines the average nep size.
Its operation capability and practical interface makes USTER ® MN100 an ideal tool for the daily monitoring and control process in laboratory. Proven hardware and software are behind the accuracy and precision of the USTER®MN100, making it a reliable tool you can count on to improve the consistency of your yarn quality.Another advantage of the USTER®MN100is that the system produces data comparable to the world reference benchmarks, the USTER®STATISTICS, as it uses the AFIS® standards. It is possible that the test results correlate to USTER® STATISTICS AFIS® neps/gram for benchmarking purposes.
Minimizing the Error Rate With Classimat 5
Presenting creative solutions to yarn manufacturers with its newly developed technologies, USTER® offers a key advantage for classification and prevention of errors with its CLASSIMAT 5 technology. It is expressed that the most important innovation offered in Classimat 5 is to visually detect the problems which can negatively affect the quality of production.
With the device developed by USTER, while fault classification based on the well-proven analysis of thick and thin places remains fundamental, it must now also cover critical parameters such as foreign matter, count variation, periodic faults, unevenness and hairiness. USTER® CLASSIMAT 5 incorporates all the features of USTER ®QUANTUM ® Classimat and USTER ® Classimat 3 which are previous versions of CLASSIMAT. This product also offers the possibility to detect coloured foreign fibres, herbal substance and the content of polypropylene with powerful new sensor having multi-colour light source.
The most important innovations of Classimat 5 technology include classification of periodical errors, analysis of limits based on cleaning index, classification of irregularities in terms of imperfection and hairiness, the possibility of making comparisons with USTER (R) STATISTICS 2007 as well as respective company data of users, comparing the yarns coming from different parties or suppliers and quality ranking, technically most advanced USTER (R) sensors, reliable measurements irrespective of machine or test rate changes and lastly the unique mounting module with special manual and voltage control.
Incredible Sensitivity in Detecting Errors
YARN BODYTM (yarn structure) concept is considered to be the best approach to detect the irritating faults. USTER® CLASSIMAT 5 shows thick and thin points in YARN BODYTM (in yarn structure) with a numerical classification. With this technology, the colored foreign substances are graphically shown with the numerical representation when the degree of pollution is shown. With its new technology, USTER ®offering many advantages makes difference by classifying the problems of polypropylene for the first time. Besides, all the errors which had been previously classified into 23 different categories are now classified into many more categories. with Uster® Classimat 5, errors can be detected in 45 different categories. as this new technology optimizes the cleaner's settings, irregularities experienced in the yarn production process can be controlled effectively and eliminated during winding.