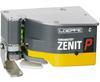
Loepfe, which manufactures electronic yarn clearers running in an optical basis for the winding machines, has been making innovations for 50 years for increasing the yarn quality in the sector. In the statement he made to us, Erol Karakaş, Authorised Officer of Loepfe Brothers in Turkey, emphasized that ‘quality’ is important for Loepfe. Karakaş underlined that as a result of the developed ‘quality perception’, the company continues its production in Switzerland. Karakaş added that today the electronic yarn clearers are indispensable in staple fiber production. “The primary goal of Loepfe, which combines the principle based on optical control technology and the knowledge and experience it gained for many years, is customer satisfaction,” said Karakaş.
Karakaş mentioned the importance of optical technology in the yarn clearing process and stated that with optical measurement and image measurement of the yarn, results are taken as closest to reality. Karakaş remarked that as the compact yarns have gained importance, optical measurement has also become more important. “It has been obvious that in addition to the usual quality requirements, the irregularities in the yarn hairiness and the increases ocurring on some parts should be eliminated in this type of yarns. And this can be done only through the measurements carries out by optical systems. Another benefit of this optical measurement principle is that the cutting values are independent of the changes that may occur in the climate of the facility and it can work on any kind of fiber and splice method,” said Karakaş.
Clearing the Colored Impurities Gained Importance
Underlining that clearing the colored impurities in 100% cotton yarns has become a fundamental requirement, Erol Karakaş said that the other requirement is to clear the contamination and colors caused by fly generated between the unopened fibers and machines during the final winding of dyed yarns and winding of the dyed melange yarns. .
Karakaş stated that Loepfe is still the leading company of the innovative colored measurement sensors, put on the market by the company in 1991. Karakaş added that unlike many other systems, these sensors do not read the reflections directly from the yarn. Karakaş talked about how the system works using the advanced electronic and software technologies; “The sensor within the yarn is illuminated on both sides by 8 leds. The amount of the innumination applied on different directions is adjusted separately for each network by using microprocessor and specific algorithms. By this way the wasted yarn within the illuminated sensor is equalised actually to the base value. The sensor that measures the yarn as a wasted base, detects the slightest color change on the yarn accurately. The measurement done on a broad area, ensures obtaining a stable performance at difference winding speeds and now the only thing that the operator should do is the selection - according to the quality and cutting number needed - of the faults, which are shown after counted in 128 classification zones.”
Demands of the Professionals Differs
Erol Karakaş underlined that the yarn quality is very important criterion for the finished product and added that different yarn buyers have different expectations from quality. “For example in addition to the companies, which regard 3 faults as the limit for 20 kg of knitted fabric, there are buyers that tolerate more faults, which includes yarn, knitting or other kind of faults. The disturbance caused by the same yarn fault differs according to the different knitting/weaving reports or at different fabric weights. Of course this depends only on the final users intended use. Hence a t-shirt made of 100% cotton can be sold at a price between 10 YTR and 200 YTR,” said Karakaş.
Karakaş stated that Loepfe Zenit electronic yarn clearers digitally show the true strucutre of the yarn and he added that all irregularities – thick or thin - in the yarn are counted in this process and the operator is given the chance to regulate the limits he desires by using the the data and the advanced test modes. Karakaş emphasized that the aim is not to limit the cutting number. He continued by saying; “Any kind of abnormality that may occur in the process, may cause increases in particular classimat zones that you suppose to be ‘yarn structure’. If these abnormalities are not prevented, complaints arise about quality and in such cases you have to make cuttings much higher than your ideal cut expectation. Variable raw materials and production conditions require active control and adjusting.”
“In this process what is important is how many faults you can not cut, rather than the number of faults you cut,” said Erol Karakaş and added that for that reason the most important thing for Loepfe is to follow the production process closely and to provide the facilities with the necessary and sufficient trainings and
Great Interest for the New Generation Sensors
Loepfe, which has been performing production in Switzerland, managed to attract interest with the new generation P2 sensors. The product that was introduced at ITMA Barcelona, offers real and rational solutions on the winding machines with Yarn Master® Zenit C and on the Open End machines with Yarn Master® 3N1 and 1N1. P2 sensor eliminates the ‘polypropylene’ problem, which has been causing great troubles in the facilities especially in the recent years. Thanks to its renewed hardware and software, a great decline has been achieved in the number of unidentified cuts while the clearing performance increased considerably.
Zenit C Series, equipped with universal optical measurement sensors, can control all staple yarns with the same measurement head between a range of Ne 4 - Ne 320. Besides natural or synthetic, raw or dyed yarns and different tying methods can be controlled with the same measurement heads.