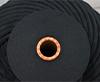
The Autocoro 10 is perfectly tailored to sustainable raw materials, especially those that consist largely of recycled and regenerated materials. These raw materials are ecologically valuable, but with other spinning systems they can be also potential productivity killers. With SynchroPiecing 36, the Autocoro 10 offers a 50% higher piecing capacity than the previous generation, which ensures particularly high productivity, especially when regenerated material is being processed. The new lighting concept results in further efficiency potential. The generally coarser yarns made from regenerated fibres result in short spinning cans, and empty cans have to be exchanged for full cans more frequently. The lighting concept of the Autocoro 10 shows the operator with widely visible colour signals which cans need to be replaced and when, improves the overview of the staff, reduces travel times and promotes more efficient use of staff.
Autocoro 10 –Targeted for Sustainable Raw Materials
Due to the focus on coarser yarns when regenerated materials are spun, full packages have to be replaced with empty tubes much more frequently than with fine yarns. For this reason, the package changing capacity of the Autocoro 10 has been increased by 25% to up to 8 changers. The high material throughput when spinning the regenerated fibres can also lead to increased fibre fly and dust accumulation and, as a result, to shortened cleaning intervals. Here, too, more package doffing units score points, because they prevent fluff from accumulating at the spin box.
The automatic cleaning function of the Autocoro is perfected with its new Vacuum Trash Cleaner, which removes unwanted particles from the dirt channel during spinning. In this way, these rotor-spinning machines automatically stay cleaner when processing all raw materials. The manual interventions required by the operating personnel are reduced, and so are the personnel costs.
Milestone for More Productivity
Automation is rooted in the Autocoro 10, in its DNA. The result: Unique, profitable functions that ensure worldwide higher productivity, such as seamless lot changes during production. Even with only three seamless lot changes per month and machine, the additional annual production of all Autocoro spinning mills worldwide with medium fineness already adds up to over 3 000 40-foot containers with yarn compared to the production of rotor-spinning machines that cannot handle a smooth lot change.
Autocoro Packages Protect the Environment
Autocoro packages are particularly sustainable. Digital winding technologies such as DigiWinding set the benchmark for excellent unwinding properties and higher productivity in weaving and knitting mills. This also reduces the specific area consumption per produced square metre of fabric and knitting, as fewer weaving and knitting machines are needed to produce the required quantity.
In addition, thanks to their design with their straight flanks, these packages reduce transport and packaging costs worldwide by making better use of the space in cardboard boxes and containers and reduce cavities in them. Already when these packages are on the way to the next location for further processing, Autocoro spinning mills save around 5 500 to 6 000 40-foot containers every year, which corresponds to the transport capacity of a medium-sized container ship, plus the savings for in-house transport in the spinning mill.
Autocoro 10 – just switch on and get started
Another great asset of the Autocoro is its outstanding reliability. Set up, switch on, produce. Only the Autocoro is predictable and highly profitable from the first minute of operation – as proven by around a million spinning positions all over the world.