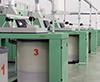
Being one of the important representatives of the yarn machinery lines in the world, Marzoli manufactures systems offering quality and cost advantages to the users with the R&D works it focuses on. With new Galileo line, Marzoli focuses on not only increasing production and reducing energy consumption but also on reducing cotton waste during spinning and increasing quality. The new Galileo line affects cotton end-product cost by 60 %. For the yarn manufacturer, obtaining the same quality with less waste is a great advantage.
Blowroom
Innovative fullers and carding units allow for better opening and perception of the fibres and thus, increase the cleanliness of the cotton. At the same time, they reduce the amount of cotton in good state within the waste. New carder C701, offered by Marzoli, has the largest carding surface now in the market. The carding effect is higher thanks to the lesser amount of fibre distributed to the carding elements. The best perception of short fibres and wastes; lesser waste amount and strip cleaner. Marzoli carder and dredging machine result in 3 % lesser waste on average while obtaining the strip of the same quality. The fact that the strip of C701 is orderly and perfect quality of the paddings manufactured by the new padding manufacturer reduce the length of the waste fibres of CM7 and make it possible to increase the selection of the fibres. A reduction of waste percentage up to 2 % when compared to the processed cotton preserves the same strip order in the traditional lines. New C701 meets the requirements of the technical and technological innovation with its new operation width of 1500 mm and guarantees more production and higher quality compared to most of its rivals.
Roving Frame
Numerous tests conducted by Marzoli with its different clients have shown that yarn quality can be increased through the use of 27 mm cylinders. The special shape in Arcobridge stick and sledge ensures a better and increasing fibre control in the take-up area. With the innovations aiming at reducing errors in the yarns, gross and thin errors are reduced by 40 % at Ne 40 combed yarn. Compact technology keeps fibres parallel following take-up and reduces spinning triangle. Thus, fibres are better spun within the yarn and quality results are obtained.
Lesser hairiness and higher yarn resistance is the most important target of compact yarn. The new yarn spinning line created by Marzoli with new technology machines offers the clients with the opportunity of obtaining the same yarn quality with 4-6 % lesser waste from blowroom to yarn machine or achieving higher quality with the same waste rate.